NEWS
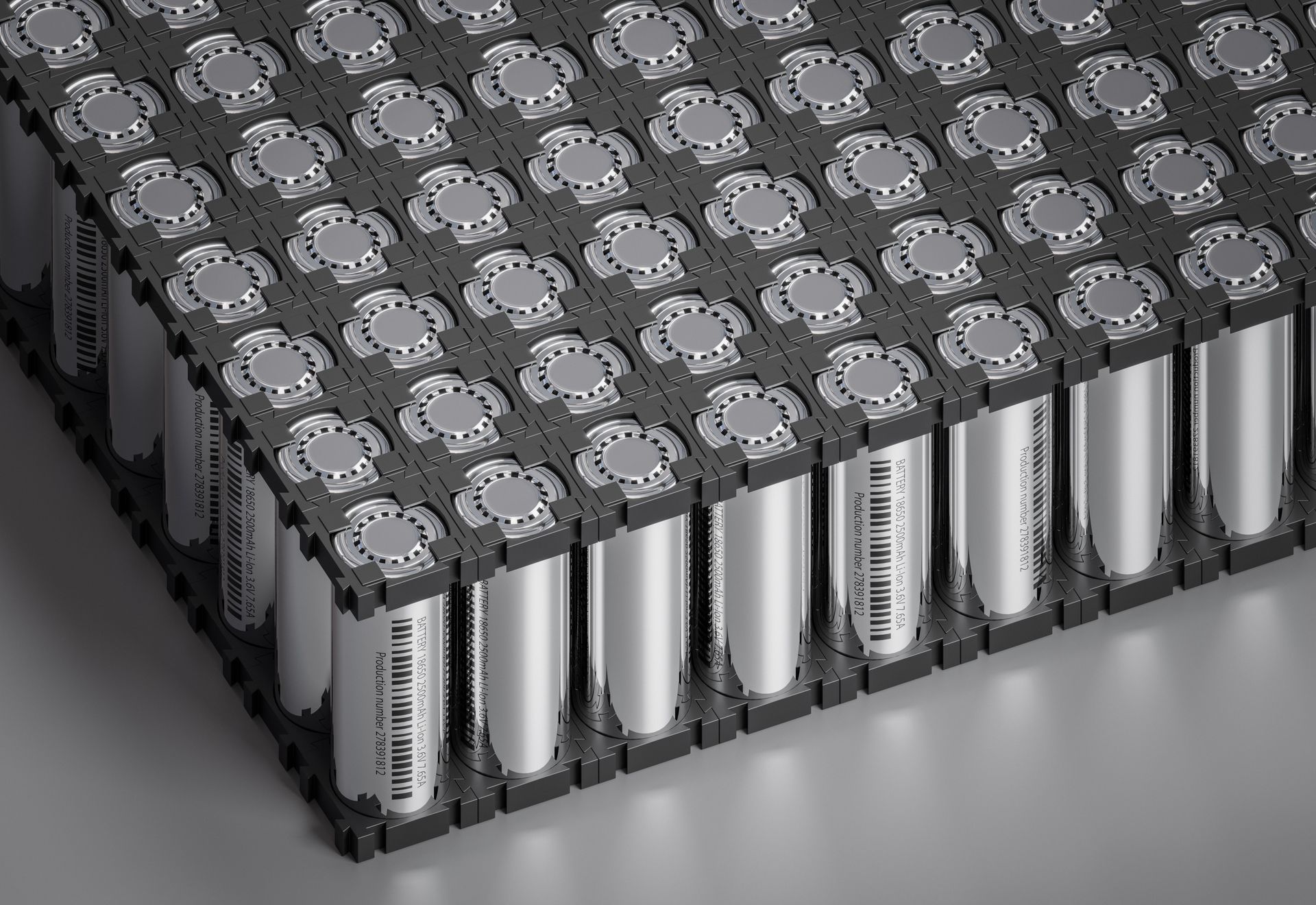
Chaired by former Defence Secretary, Lord Hutton, the new Commission will address the UK’s urgent need for domestic battery manufacturing across energy, defence, transport, and tech sectors Lord Hutton has launched a Policy Commission on Gigafactories to support the UK’s ambitions for economic growth and sustainable industries. This Commission brings together senior cross-party political figures and industry leaders with deep expertise in government, policy, manufacturing, energy and national security. Its members include three former Cabinet Ministers, and two respected industry experts – combining political experience with frontline sector knowledge. The Commission will consult with stakeholders from across industry, government, academia, and investors, and will publish its findings and recommendations early in 2026. The Commission will produce recommendations on how the UK can scale up its battery manufacturing capacity – a critical requirement to achieving net zero, generating economic growth and securing high-quality green jobs. The Commissioners are: Rt Hon Lord John Hutton (Chair), former Secretary of State for Defence Rt Hon Greg Clark , former Secretary of State for Business, Energy and Industrial Strategy and Chair of the Society of Chemical Industry, and currently Chair of the University of Warwick’s Innovation District Dr Isobel Sheldon OBE , founder of Oak Polytech Rt Hon Baroness Lindsay Northover , Member of the Lords Science and Technology Committee Rt Hon Sir Oliver Letwin , former Minister for Government Policy and Chancellor of the Duchy of Lancaster, currently Senior Advisor to the Faraday Institution Dr Ian Constance , CEO at Advanced Propulsion Centre UK The Commission comes at a pivotal moment for the UK as the Government negotiates new trade deals and is expected to launch its Industrial Strategy in the coming weeks. From energy independence to electric vehicle production, national supply chain resilience to our trading relationship with China and the USA, the need for increased battery manufacturing cuts across many major policy priorities facing Britain today. The Faraday Institution , the UK’s independent institute for electrochemical energy storage research, skills development, market analysis, and early-stage commercialisation, will serve as secretariat to the commission. Lord Hutton of Furness, Chair of the Commission, said: "Batteries are no longer just a tech issue or an energy issue – they are a national strategic imperative. The UK cannot afford to remain dependent on foreign supply chains for such a vital component of our economic and energy future. This Commission will ask the difficult questions and provide bold but realistic and politically deliverable recommendations to put Britain on the front foot." Professor Martin Freer, CEO of the Faraday Institution, added: "Britain has world-class battery science and growing industrial ambition. We are pleased to support this Commission, which is about turning that potential into national strategy – one that boosts jobs, strengthens our energy and tech sectors, and protects the UK's strategic autonomy."
March 18th, 2025 – Altilium, a UK-based clean technology group focused on supporting the transition to net zero, is pleased to announce the successful production of the UK’s first EV battery cells using recycled cathode active materials (CAM) at the UK Battery Industrialisation Centre (UKBIC), the UK’s national battery manufacturing scale-up facility. The breakthrough marks the first time that recycled materials have been used to produce new battery cells in an industrial environment in the UK and marks an important step towards the development of a circular economy for EV batteries. The pouch cells were manufactured at UKBIC's state-of-the-art facility in Coventry using Altilium’s recycled EcoCathode™ NMC 811-2036 CAM, produced at its recycling facilities in Devon. By recovering these critical metals from end-of-life EV batteries and Gigafactory waste, Altilium is not only reducing the UK’s reliance on imported raw materials, but also cutting the carbon footprint of battery manufacturing, making EVs even greener. The battery cells will now undergo comprehensive validation studies with a leading automotive OEM, supporting their regulatory and sustainability targets. Under the EU’s Battery Regulations, new EV batteries sold into the EU will need to contain minimum levels of recycled lithium, nickel and cobalt from 2031, with further increases in 2036. Altilium’s battery cells are the first to be manufactured in the UK complying with the new regulations. The recycling process begins with the dismantling and shredding of end-of-life EV batteries to produce a fine powder know as black mass. This black mass is then processed using Altilium’s EcoCathode™ process, which is able to recover over 95% of the critical battery metals, including lithium. The cathode metals are then upcycled to produce a high-nickel NMC 811 CAM, ready for re-use in a new battery. Dr Christian Marston, Altilium co-founder and COO, commented: “This milestone marks the first time full battery circularity has been achieved in the UK, from recovering critical minerals, including lithium, from end-of-life EV batteries and upcycling them into a high-performance cathode, to manufacturing a new battery for validation with a leading UK automotive OEM. Through this collaboration with UKBIC, we are moving beyond the emerging black mass recycling industry and ensuring that these critical battery materials remain in the domestic supply chain. Having access to a manufacturing facility like this allows us to scale up and develop this innovative work, which is helping to position the UK at the forefront of sustainability and decarbonisation.” Ameir Mahgoub, UKBIC’s Head of Product Engineering, added: “We're delighted to have been part of the team creating the UK's first battery cells made using CAM containing recycled material. This pioneering project could be just the start of a journey that sees the UK becoming less reliant on imported materials and create a new market in recycled EV batteries. We look forward to collaborating with Altilium on this exciting project as they take it forward.” By demonstrating at-scale manufacturing of battery cells using recycled CAM, the collaboration with UKBIC is helping to advance commercialisation of Altilium's technology, paving the way for supply deals with automotive OEMs and battery manufacturers and de-risking investment in further scale-up, including construction of the UK’s largest planned commercial plant for EV battery recycling and CAM production. Altilium's planned ACT4 recycling plant in Teesside will have capacity to produce 30,000 tonnes of CAM a year – enough to meet nearly 20% of expected UK demand by 2030. The scale up of Altilium’s recycling operations will also deliver wider benefits for the UK economy and the environment. By developing a domestic, sustainable source of battery raw materials, Altilium is helping to meet the growing demands of new green industries, such as EV manufacturing, while reducing the UK’s reliance on mined raw materials and supporting the transition to net zero. Independent analysis of Altilium’s recycled materials has already revealed improvements in quality compared to mined materials, as well as significant reductions in climate change impact and cost: According to research carried out by Imperial College London, Altilium’s recycled EV battery materials can match, and even surpass, the performance of virgin mined materials, enabling longer battery life, faster charging times and lower costs. Lifecycle analysis (LCA) by Minviro has found that cathode materials produced using Altilium’s recycled materials could be up to 74% lower in climate change impact compared to using primary mined materials from a Chinese supply chain.  About Altilium Altilium is a UK-based clean tech group that will reshape the UK and European automotive supply chain by offering high volume, low carbon domestic sources of cathode and anode materials from recycling waste streams already in circulation, such as end-of-life batteries. The company’s proprietary EcoCathode™ process converts end-of-life EV batteries and manufacturing scrap into domestic, sustainable, battery precursors, cathode active materials (CAM) and cathode precursor (pCAM) for direct reuse in new batteries. Altilium’s first mini-commercial plant recently commenced operations in Plymouth while its planned Teesside plant will be one of the largest EV battery recycling facilities in Europe. The plant will have the capacity to process scrap from over 150,000 EVs per year, producing 30,000 MT of CAM, enough to meet around 20% of the UK’s expected needs by 2030. The company is backed by SQM Lithium Ventures, the corporate venture arm of the lithium business of Sociedad Quimica y Minera de Chile (SQM), and Japanese trading and investment group Marubeni Corporation. For more information go to www.altilium.tech For media inquiries contact Dominic Schreiber: dominic@altilium.tech About UKBIC UKBIC is the UK’s £200m national manufacturing battery development facility, providing manufacturing scale-up and skills for the battery sector. The purpose-built facility is where businesses develop their battery manufacturing processes at the scale they need to move to industrial production and where those working in the industry can develop new skills by working on the production line, alongside UKBIC’s specialist teams. Created with an initial investment of £130m, an additional £74m has now been committed by UK Research and Innovation to enhance the facility by installing a new pilot line to bridge the gap between UKBIC’s larger scale offering and small-scale demonstrators available elsewhere. Funding is also being used to support the construction of a new battery development laboratory, a clean and dry zone, and cell cyclers. Opened in July 2021, the Coventry-based facility can be accessed by organisations with existing or new battery technology, or companies looking at entering the industry. UKBIC doesn’t retain customer IP. UKBIC’s construction was part-funded through the West Midlands Combined Authority and was delivered through a consortium of Coventry City Council, Coventry and Warwickshire Local Enterprise Partnership and WMG, at the University of Warwick.
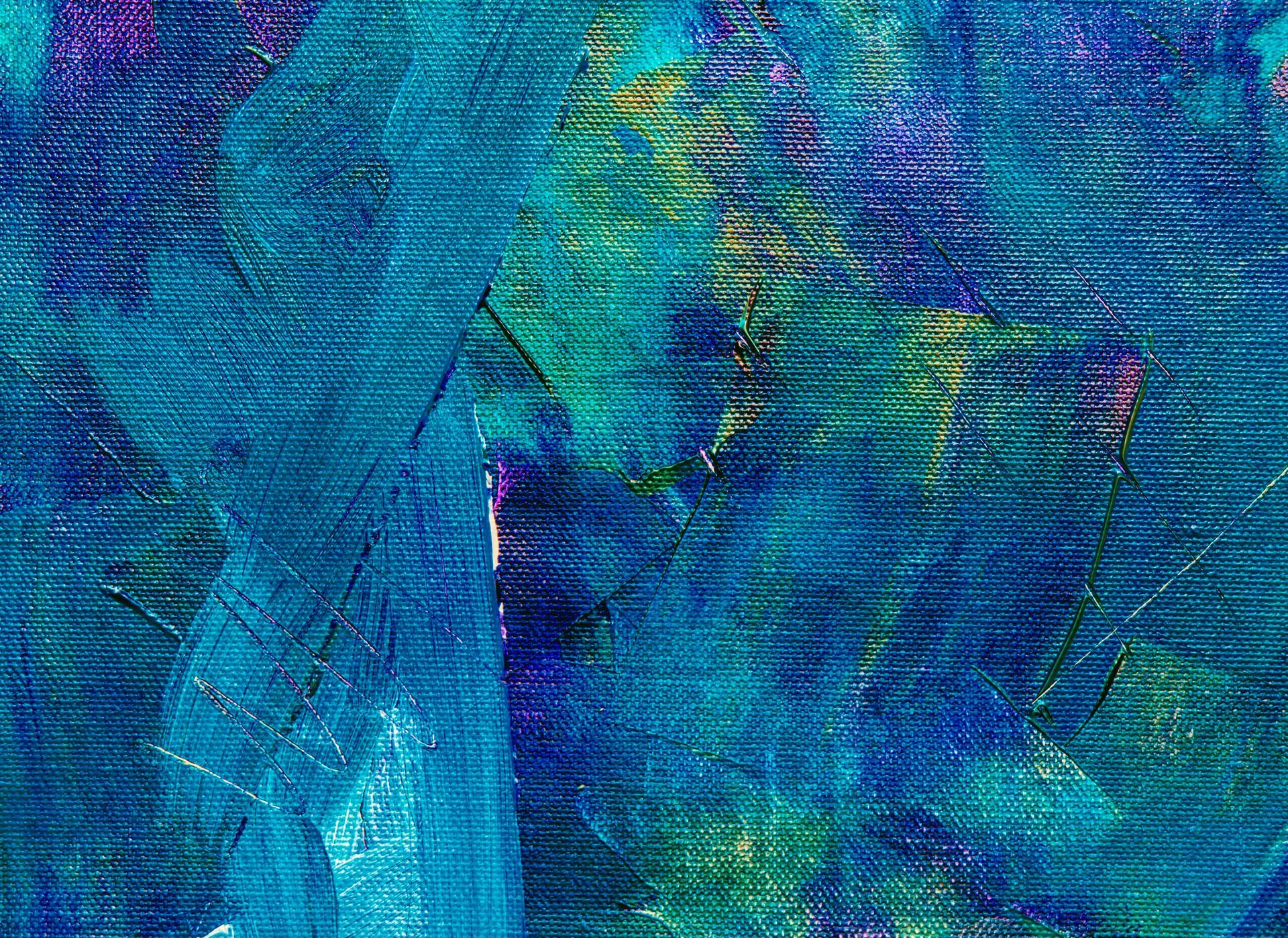
Ben Walsh and Thomas Bartlett, Co-Interim Faraday Battery Challenge Directors, Innovate UK, Martin Freer, CEO, Faraday Institution, Sean Gilgunn, Managing Director, UK Battery Industrialisation Centre, lay out their thoughts for the Faraday Battery Challenge in 2025 as it builds for the future.  As we approach a new financial year, we’d like to let UK industry partners know what to expect from the Faraday Battery Challenge in 2025, how we’re keeping momentum going, and the various ways and places you can connect with us. We are working hard with Government to establish the next phase of the programme to support battery innovation in the UK. In the meantime, funding is still available for UK battery innovators . The Advanced Propulsion Centre UK (APC) has a call open for late stage, automotive collaborative R&D projects until 14th March 2025. APC and Zenzic are also partnering on a new business accelerator – Mobilise – to provide opportunities for ambitious SMEs developing zero-emission and connected and automated mobility technologies, products, services or solutions. Applications close 19 March. The APC runs zero-emission vehicle funding competitions throughout the year, so please check their website for updates. The Faraday Institution continues to consider applications for Industry Sprint projects , Industry Fellowships and Entrepreneurial Fellowships . Sprints aim to solve a commercially relevant research opportunity identified by an industrial partner. Entrepreneurial fellowships support start-ups looking to create new businesses and commercialise battery technologies by providing seed funding, business support and mentoring.
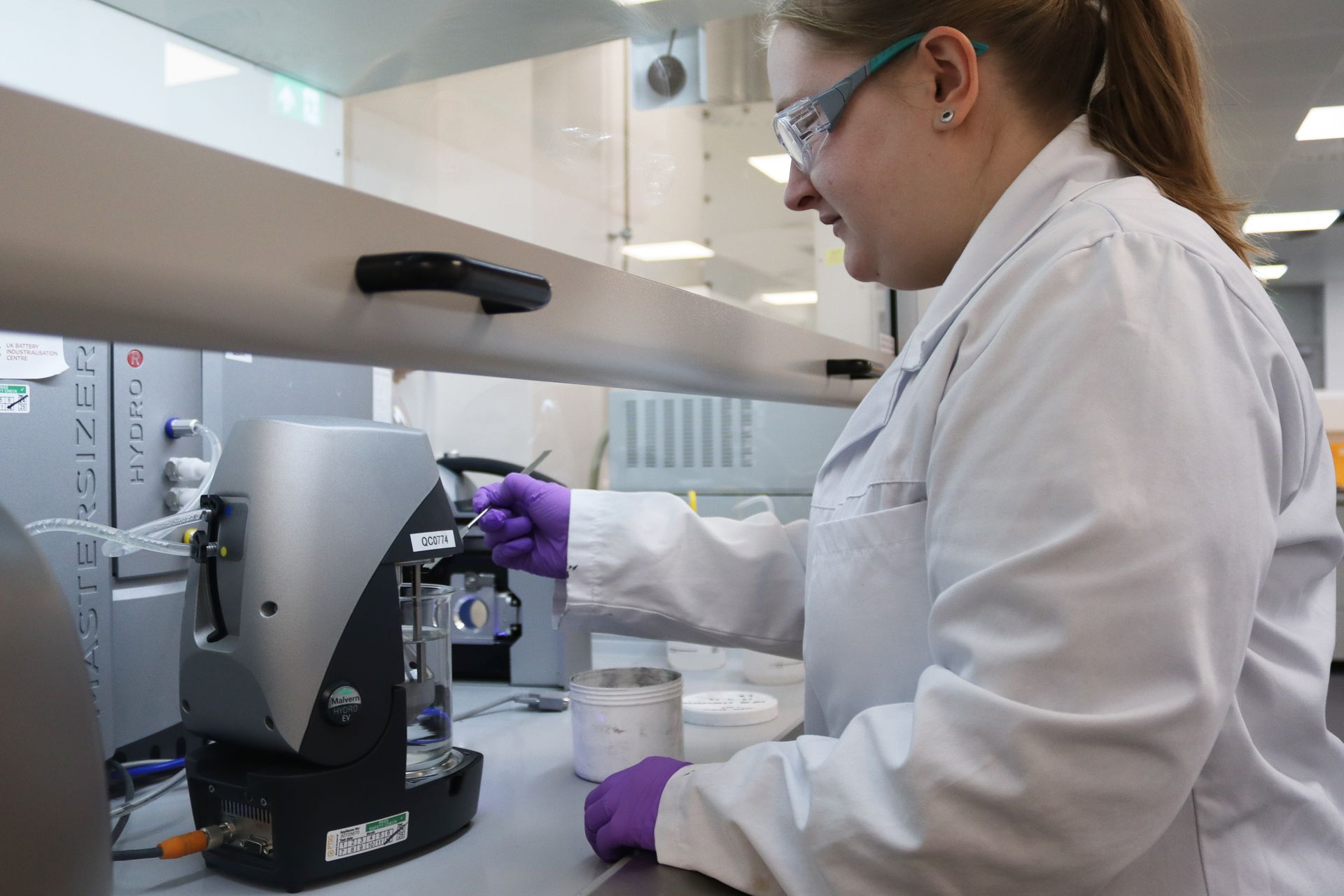
The UK Battery Industrialisation Centre (UKBIC) has opened its new upgraded and extended Battery Development Laboratory (BDL) which has greatly increased the facility’s capabilities in key areas of battery materials characterisation, cell analysis and forensic activities. The new laboratory allows customers from all over the world to come to UKBIC to have their materials and cells analysed and tested in real-time. The enhanced capability will provide vital data to customers during the lifespan of the battery cell scale-up journey.
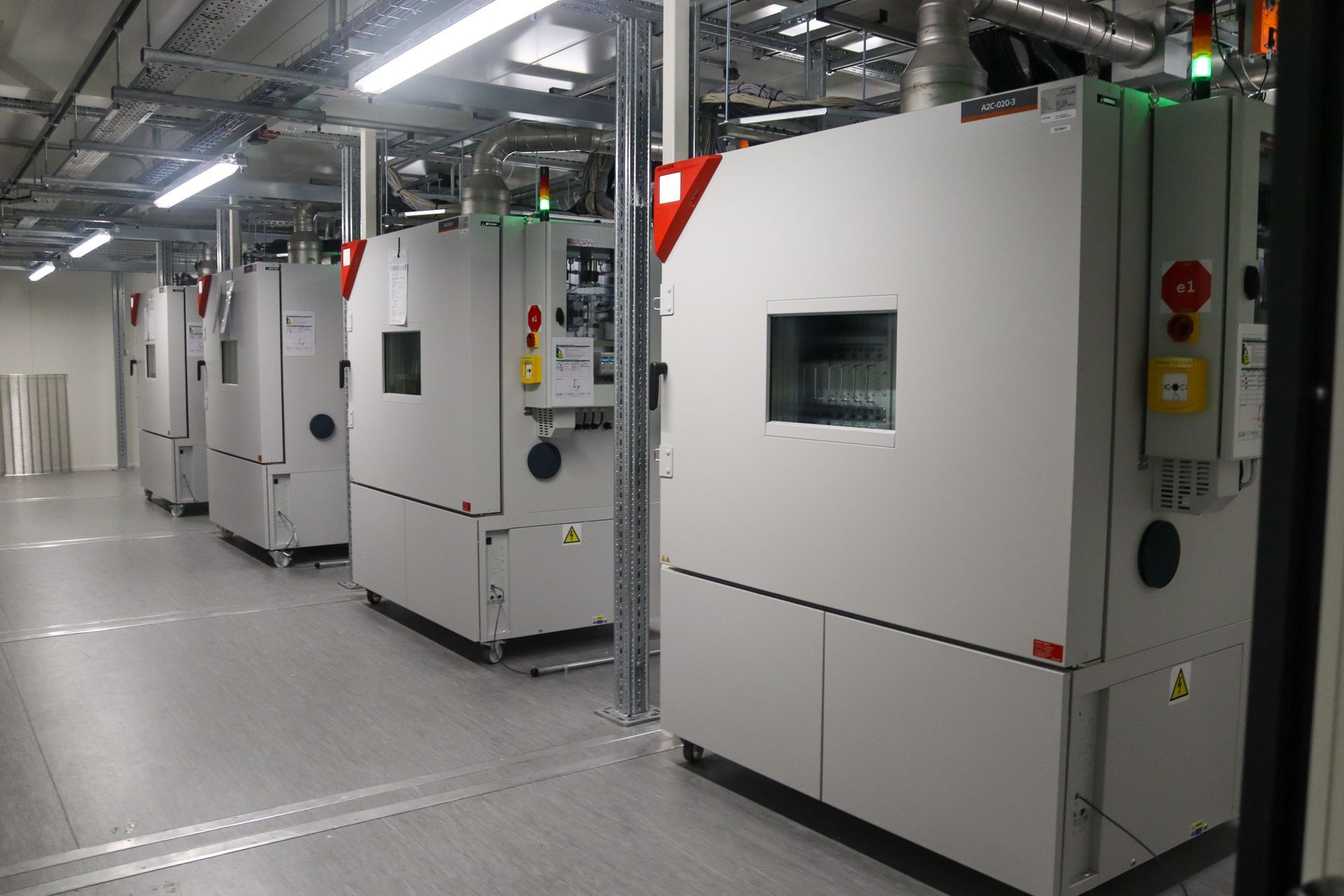
New specialist equipment for battery developers and manufacturers is now operational at the UK Battery Industrialisation Centre (UKBIC). The cell cyclers and environmental chambers installed at the Coventry-based battery development facility enable developers to continuously charge and discharge cylindrical and pouch cells, and measure how many cycles a battery cell can deliver over its life. Housed inside a 135m² air-conditioned unit, the cyclers feature custom-made racking and cell fixtures designed to perform high-accuracy cell characterisations in different environmental conditions. The 15A cylindrical cell cycler has 192 channels and the 100A pouch cell cycler has 96 channels. The cyclers include extended lifecycle testing, in Binder EUCAR* hazard level 6 chambers that can be environmentally controlled and measured, and the ability to give customers the opportunity to try out new chemistries, to validate cell designs and trial new cell materials, all in one location. Sean Gilgunn, UKBIC’s Managing Director, said: “The cell cyclers will be a huge asset to the UK battery industry, helping us become a one stop shop for.” Richard LeCain, UKBIC’s Chief Technology Officer, added: “The new cyclers will help make UKBIC’s world-class scale-up facilities an even more attractive proposition to battery developers, allowing performance to be independently validated and risk to be reduced.” The equipment is the first in a series of upgrades to UKBIC, totalling £74m. Funded through the Faraday Battery Challenge by UK Research and Innovation, other enhancements in the pipeline are: An expanded battery development laboratory, which is due to be operational in early 2025; A clean and dry zone where customers can rent areas for their own development and testing purposes, which is also due to open in 2025; and A flexible pilot line to bridge the gap between UKBIC’s industrial scale offering and small-scale demonstrators available elsewhere, which will open in Summer 2025. The Faraday Battery Challenge is a £610m investment programme which supports world-class scientific technology development and manufacturing scale-up capability for batteries in the UK. The Challenge supports world-class scientific technology development and manufacturing scale-up capability for batteries in the UK. -ends- * EUCAR is the European Council for Automotive R&D of the major European passenger car and commercial vehicle manufacturers. EUCAR facilitates and coordinates pre-competitive research and development projects and its members participate in a wide range of collaborative European R&D programmes. Notes to editor: To arrange an interview, please email richard.robinson@ukbic.co.uk or phone +44 (0) 7503 628892 UKBIC is the UK’s national manufacturing battery development facility, providing manufacturing scale-up and skills for the battery sector. The purpose-built facility is where businesses develop their battery manufacturing processes at the scale they need to move to industrial production and where those working in the industry can develop new skills by working on the production line, alongside UKBIC’s specialist teams. Created with an initial investment of £130m, an additional £74m has now been committed by UK Research and Innovation to enhance the facility by installing a new pilot line to bridge the gap between UKBIC’s larger scale offering and small-scale demonstrators available elsewhere. Funding is also being used to support the construction of a new battery development laboratory, a clean and dry zone, and cell cyclers. Opened in July 2021, the Coventry-based facility can be accessed by organisations with existing or new battery technology, or companies looking at entering the industry. UKBIC doesn’t retain customer IP. UKBIC’s construction was part-funded through the West Midlands Combined Authority and was originally delivered through a consortium of Coventry City Council, Coventry and Warwickshire Local Enterprise Partnership and WMG, at the University of Warwick.
The UK Battery Industrialisation Centre (UKBIC) – the national battery manufacturing facility providing manufacturing scale-up and skills for the battery sector - in conjunction with Warwickshire County Council, is set to offer a free of charge two-day training course in battery manufacturing. Participants who work for a company based in the county, and are aged 50 and above, can apply to Warwickshire County Council’s New Direction – 50+ Skills Investment Fund, for a place on the fully funded Introduction to battery manufacturing training. In addition to this, there are fully funded places available for anyone in full-time employment through the Skills Escalator Fund. To be eligible, you must be a small to medium sized business or self-employed and based in Warwick and Stratford with Nuneaton & Bedworth and Rugby coming soon. Training must be completed by March 2025. Both grant schemes allow five places per company. Jonty Deeley-Williamson, Head of Learning & Development, UKBIC, added: “It’s fantastic to get such brilliant support from Warwickshire County Council to boost skills across the county in battery manufacturing. These courses will give employees who work for a company based in the county a helping hand to work in the growing battery manufacturing sector.” By 2040, the Faraday Institution estimates that the battery industry could support 170,000 jobs nationally in the automotive industry and a further 100,000 jobs in battery manufacturing and the wider battery supply chain. Significant reskilling and upskilling programmes will be needed to cater for the 35,000 jobs in gigafactories and 65,000 jobs in the battery supply chain that could be created. Louise Stolz, Future Skills Business Support Advisor, Warwickshire Skills Hub, said: "Warwickshire County Council’s Future Skills Fund is a multi-strand programme, designed to develop work related skills and knowledge for new and existing employees, in new and emerging technologies, such as battery technology. It’s great that Warwickshire businesses can now access courses with the UKBIC in Battery Manufacturing and really supports the work Warwickshire Skills Hub are doing around the future skills agenda. The next Introduction to battery manufacturing is being held on 22 and 23 September. Anyone wishing to find out more about training at UKBIC and the free training courses should contact: training@ukbic.co.uk  Notes to editor: To arrange an interview, please email richard.robinson@ukbic.co.uk or phone +44 (0) 7503 628892 UKBIC is the UK’s national manufacturing battery development facility, providing manufacturing scale-up and skills for the battery sector. The purpose-built facility is where businesses develop their battery manufacturing processes at the scale they need to move to industrial production and where those working in the industry can develop new skills by working on the production line, alongside UKBIC’s specialist teams. Created with an initial investment of £130m, an additional £74m has now been committed by UK Research and Innovation to enhance the facility by installing a new pilot line to bridge the gap between UKBIC’s larger scale offering and small-scale demonstrators available elsewhere. Funding is also being used to support the construction of a new battery development laboratory, a clean and dry zone, and cell cyclers. Opened in July 2021, the Coventry-based facility can be accessed by organisations with existing or new battery technology, or companies looking at entering the industry. UKBIC doesn’t retain customer IP. UKBIC is part of the £610m Faraday Battery Challenge, which is delivering a research and innovation programme that covers "Lab to Factory" development, cutting-edge research, national scale-up infrastructure, and skills and training. UKBIC’s construction was part-funded through the West Midlands Combined Authority and was delivered through a consortium of Coventry City Council, Coventry and Warwickshire Local Enterprise Partnership and WMG, at the University of Warwick. UKBIC is part of the UK Research and Innovation (UKRI) funded Electrification Skills Network (ESN). ESN’s purpose is to create a comprehensive framework for electrification skills in the UK. Other key partners in the initiative include Coventry University, Enginuity, the University of Warwick, and the Electric Revolution Skills Hub. ESN aims to bridge the gap between employers, accrediting organisations, and skills providers.
Australian businesses are a step closer to accessing world-leading battery manufacturing scale-up facilities, thanks to an agreement signed today between the UK Battery Industrialisation Centre (UKBIC) and Powering Australia. UKBIC is a £130 million ($250 million) national battery manufacturing scale-up facility based in Coventry, UK that was established by the UK Government through the Faraday Battery Challenge to help companies bridge the gap between battery technology showing promise at laboratory scale and move them towards successful mass production. The agreement is intended to strengthen collaboration in battery research, technology and innovation between Australia and the UK and aligns with the “Statement of Intent” signed by the Albanese Government in April 2023. The Statement is intended to promote collaboration on critical minerals, strengthen international supply chains, meet net zero objectives, remove barriers to adoption of new technology and help create the jobs and the workforce of the future. CEO Shannon O’Rourke said reaching the agreement with UKBIC is a key milestone for the five-month-old Powering Australia team whose work is helping to operationalise the intergovernmental agreement with tangible action and accelerate the development of Australia’s battery industry in partnership with other nations. “We are delighted to have reached this agreement with the UKBIC team, less than six months into our formation as Powering Australia which is very much aligned to the Statement of Intent. Our organisation was established to help Australian businesses succeed in clean-tech manufacturing and being able to access world scale common user facilities like the UKBIC is major win,” said Shannon. UKBIC’s facility covers 20,000 sqm and has extensive equipment covering battery production from mixing and coating, to calendering, slitting cylindrical and pouch cell assembly, and formation, ageing, testing, as well as module and pack assembly. UKBIC Managing Director Sean Gilgunn said: “This is a great first step between the two organisations to encourage cooperation between the UK and Australia in battery technology. We’re looking forward to helping Powering Australia with its vision, and, in the future, to welcoming Australian companies that want to use our state-of-the-art facilities.” The two organisations will work together on strategic projects that offer mutual benefit and will engage in the exchange of skills and expertise to help both nations develop their respective battery industries further. Notes to editor: To arrange an interview, please email richard.robinson@ukbic.co.uk or phone +44 (0) 7503 628892 UKBIC is the UK’s national manufacturing battery development facility, providing manufacturing scale-up and skills for the battery sector. The purpose-built facility is where businesses develop their battery manufacturing processes at the scale they need to move to industrial production and where those working in the industry can develop new skills by working on the production line, alongside UKBIC’s specialist teams. Created with an initial investment of £130m, an additional £74m has now been committed by UK Research and Innovation to enhance the facility by installing a new pilot line to bridge the gap between UKBIC’s larger scale offering and small-scale demonstrators available elsewhere. Funding is also being used to support the construction of a new battery development laboratory, a clean and dry zone, and cell cyclers. Opened in July 2021, the Coventry-based facility can be accessed by organisations with existing or new battery technology, or companies looking at entering the industry. UKBIC doesn’t retain customer IP. UKBIC is part of the £610m Faraday Battery Challenge, which is delivering a research and innovation programme that covers "Lab to Factory" development, cutting-edge research, national scale-up infrastructure, and skills and training.  UKBIC’s construction was part-funded through the West Midlands Combined Authority and was delivered through a consortium of Coventry City Council, Coventry and Warwickshire Local Enterprise Partnership and WMG, at the University of Warwick.
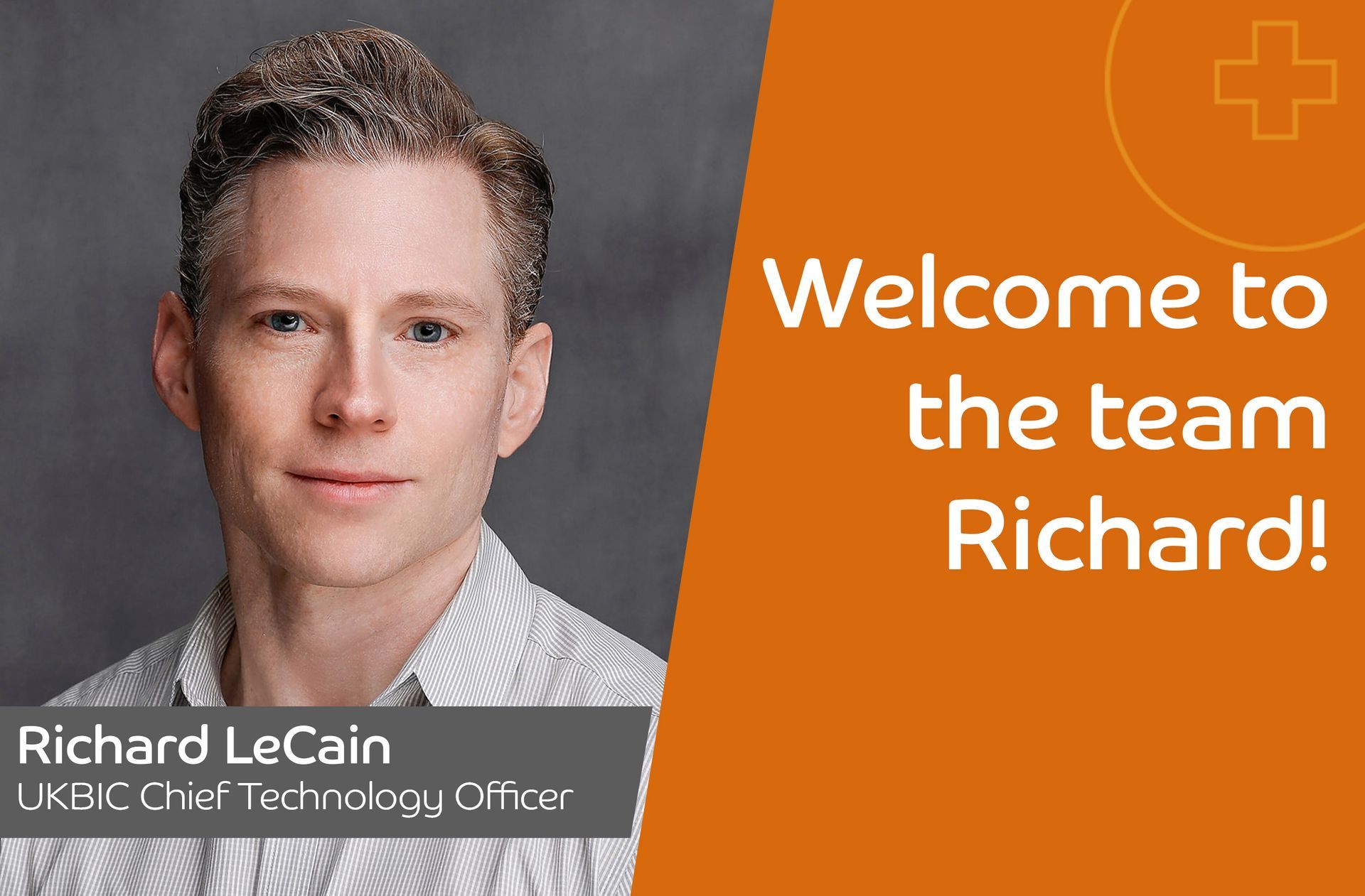
The UK Battery Industrialisation Centre (UKBIC), the national battery manufacturing facility providing manufacturing scale-up and skills for the battery sector, has appointed Richard LeCain as its new Chief Technology Officer (CTO). Richard will report into Sean Gilgunn, UKBIC’s Managing Director, and will sit on the executive team with responsibility for technical process design, product development and R&D activities across the business. Richard has more than 20 years of experience working in the battery industry, having previously held technical and leadership positions at A123 Systems and Britishvolt, where he was Director of Cell and Process Engineering. Richard began his career in batteries at Lithium Iron Phosphate pioneer (LFP) A123 Systems in the US as a process engineer where he developed LFP cells in cylindrical and pouch formats for energy storage applications such as power tools, medical devices and automotives, eventually becoming the head of cell design for low voltage applications. As Director of Cell and Process Engineering at Britishvolt, Richard and his team worked closely with UKBIC and WMG, at the University of Warwick, to quickly develop an energy dense 21700 cell for customer evaluations. Most recently, he was Director of Cell Development at US-based silicon anode company, GDI, where he worked on integrating 100% silicon anodes into lithium-ion cells for high energy density and fast charging applications. Richard has worked in battery plants across the world transferring processes and designs from the lab into manufacturing. Sean Gilgunn said: “We’re very excited with the appointment of Richard to the role of CTO. Richard’s vast expertise and experience will be hugely beneficial to our customers and employees alike, as our customers develop and refine their battery products as they move along their challenging scaleup journeys.” Richard, who will join UKBIC on 19 August, added: “UKBIC is a world class facility and I’m delighted to be joining them at this exciting time. I’m looking forward to helping companies with getting a foot on the scale-up ladder, as customers move from research and development through to volume manufacturing. From my previous engagement with UKBIC on the customer side with Britishvolt, I saw firsthand how well UKBIC could make cells and I’m excited to be part of that team now.” UKBIC is part of the £610m Faraday Battery Challenge, which is delivering a research and innovation programme that covers "Lab to Factory" development, cutting-edge research, national scale-up infrastructure, and skills and training. -ends- Notes to editor: To arrange an interview, please email richard.robinson@ukbic.co.uk or phone +44 (0) 7503 628892 UKBIC is the UK’s national manufacturing battery development facility, providing manufacturing scale-up and skills for the battery sector. The purpose-built facility is where businesses develop their battery manufacturing processes at the scale they need to move to industrial production and where those working in the industry can develop new skills by working on the production line, alongside UKBIC’s specialist teams. Created with an initial investment of £130m, an additional £74m has now been committed by UK Research and Innovation to enhance the facility by installing a new pilot line to bridge the gap between UKBIC’s larger scale offering and small-scale demonstrators available elsewhere. Funding is also being used to support the construction of a new battery development laboratory, a clean and dry zone, and cell cyclers. Opened in July 2021, the Coventry-based facility can be accessed by organisations with existing or new battery technology, or companies looking at entering the industry. UKBIC doesn’t retain customer IP.  UKBIC’s construction was part-funded through the West Midlands Combined Authority and was delivered through a consortium of Coventry City Council, Coventry and Warwickshire Local Enterprise Partnership and WMG, at the University of Warwick.
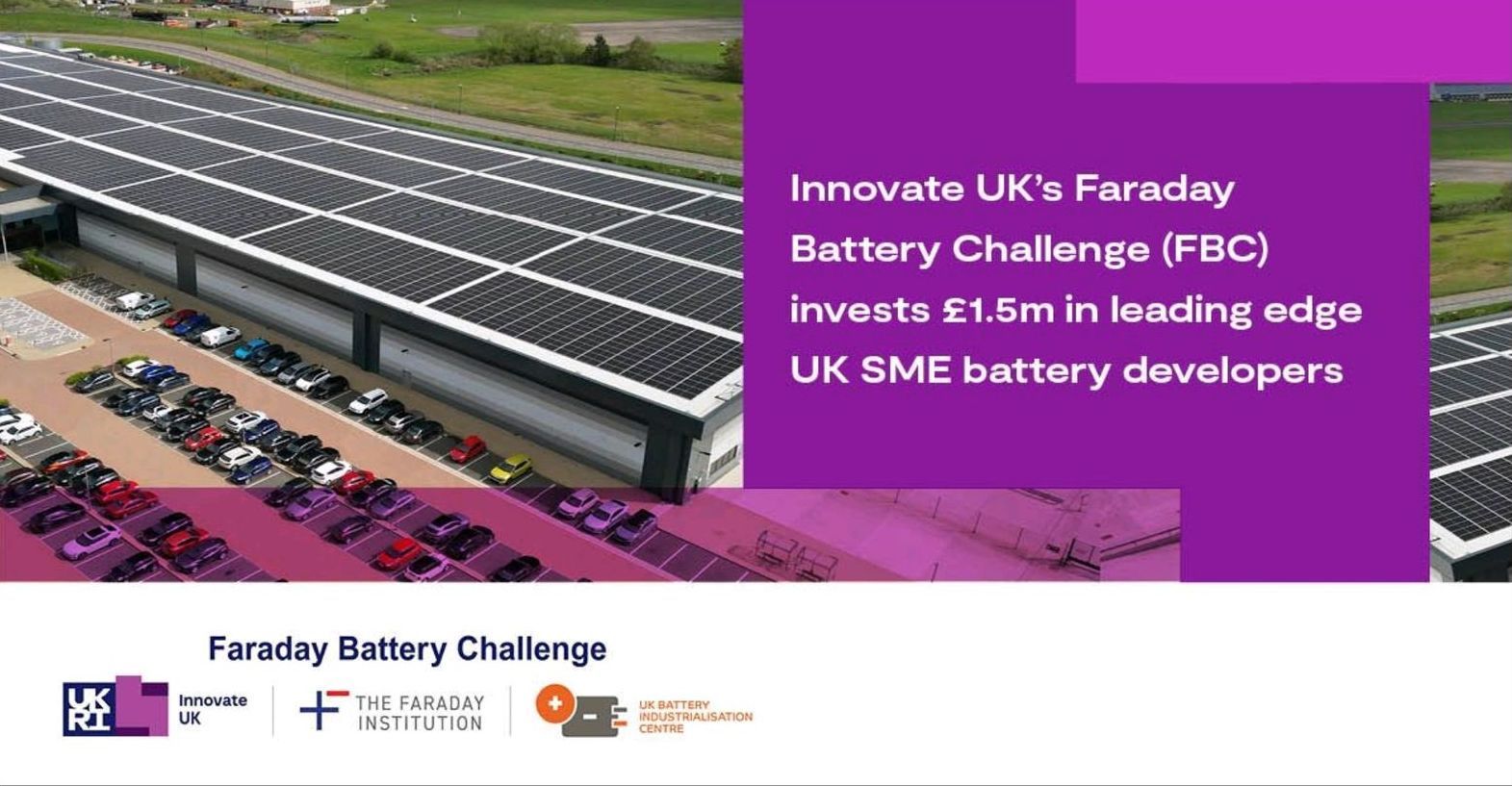
Funding will be used to develop innovative battery manufacturing, demonstration, scale-up and recycling projects. Small and medium sized (SME) battery developers from across the UK are to benefit from £1.5 million in funding from the Faraday Battery Challenge (FBC), delivered by Innovate UK. Projects involve cylindrical and pouch cell technologies and will bring advanced lithium titanate oxide (LTO) battery technology and a new cathode active material (CAM) to the UK for the first time.
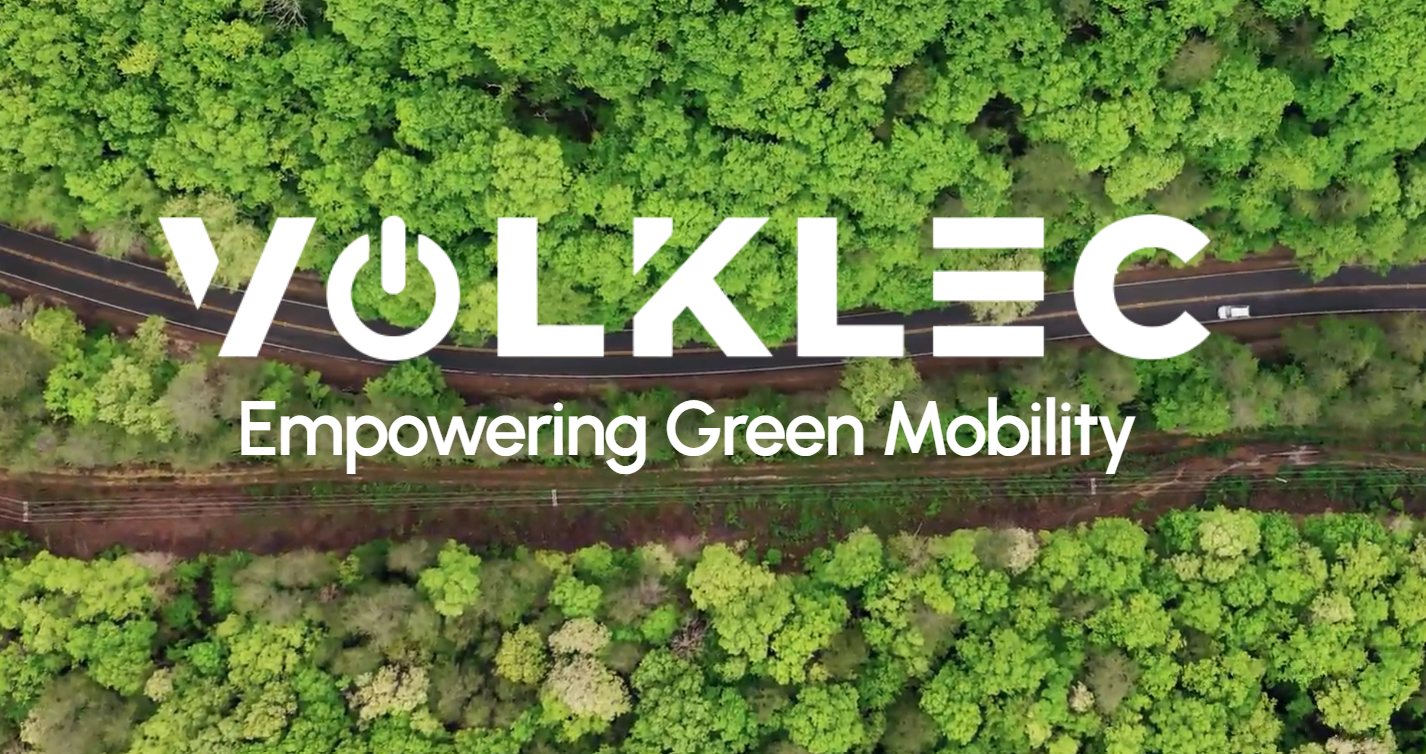
New EV battery brand, Volklec is established in the UK Backed by UK-based investment company, Frontive Group, Volklec represents significant investment in engineering and manufacturing in Coventry, the epicentre of the UK automotive industry Volklec batteries will be in development at UKBIC – the UK Battery Industrialisation Centre Coventry, UK, 15 May 2024 – Volklec, a new UK manufacturing business making batteries for electric vehicles, is launched today. Based in Coventry in the West Midlands, with the vision of Powering Electrified Mobility, it is set to manufacture sustainable batteries for on-road, off-highway and track vehicles. In an innovative UK technology collaboration, Volklec is working with UKBIC, the UK Battery Industrialisation Centre and national manufacturing development scale-up facility, which also provides skills for the growing EV battery sector. Volklec, working with UKBIC, will develop batteries to meet the attribute requirements of the UK automotive market, in particular the diverse array of small volume and niche vehicle manufacturers. Volklec’s product development and rapid route to scale-up provides a critical component in the roadmap to giga-scale production. The collaboration will directly create jobs in the West Midlands and contribute directly to building world-class battery R&D, process and manufacturing capability in the UK. Imran Khatri, Volklec Founder, said: “Volklec has been many months and significant investment in the making, established to help the UK’s decarbonisation drive. As a proud investment in the UK, our initial focus is on the automotive industry, providing security of supply to the sector, then we intend to look at the broader electrification markets as well.” Sean Gilgunn, UKBIC Managing Director, said: “We’re delighted to welcome Volklec to UKBIC and to become their launch base here in the heart of the UK automotive industry. Our purpose-built facility is where businesses can develop their battery manufacturing processes at the scale they need to move to industrial production. This agreement marks the start of Volklec’s journey to create a battery with the potential to scale up to significant volumes in the coming years, and we are proud to support the business in the initial phase of their development. Manufacturing cells at volume is vital to ensuring the UK prospers from the energy transition towards Net Zero, and this agreement further demonstrates the unique value of UKBIC to the battery ecosystem.” ENDS ABOUT FRONTIVE GROUP Frontive Group is an investor, incubator and advisor, providing solutions to grow businesses and support investors with the aim of driving sustainable change. The company’s vision is to achieve social change through investments that build a sustainable future with a focus on both environmental and social impact. Frontive Holding was founded in 2016, founding and developing numerous businesses internationally. The Group has expanded with the creation of Frontive Services (2020) – offering specialist investment solutions for high net worth individuals and family offices; and Frontive Japan (2021) – launched to support investment and business development in the Asia-Pacific region. For further information contact: media@volklec.com
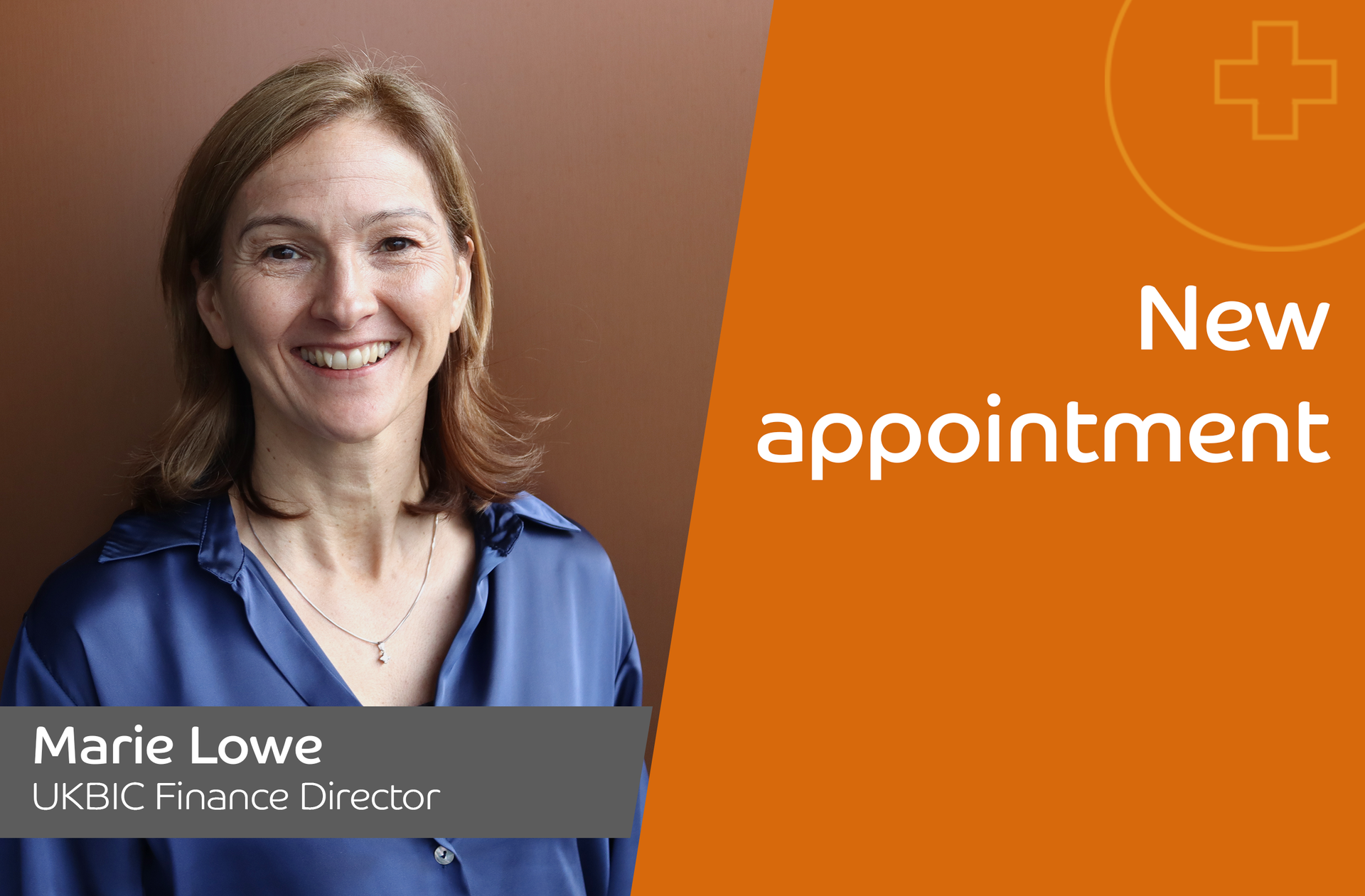
The UK Battery Industrialisation Centre (UKBIC), the national battery manufacturing scale-up facility, has appointed Marie Lowe to the post of Finance Director and Company Secretary. Marie brings a wealth of experience to the company, having held senior financial positions in engineering, automotive, and medical technology companies in the UK and North America. Marie, who begins her new role on April 1, first joined UKBIC as Financial Controller in March 2023. Ma rie will be responsible for developing, implementing and overseeing UKBIC’s financial reporting and will become part of the company’s executive team and its Board. She will lead financial operations and strategy, playing a key role in supporting the centre's ambitious goals to accelerate the UK's development of battery technology and manufacturing. Marie said: “This is a hugely exciting time to be working in the battery industry and at UKBIC. I’m really looking forward to joining the executive team and board and taking on the additional re sponsibilities this role involves.” Sean Gilgunn, UKBIC’s Managing Director, added: “I’m excited to welcome Marie to the post of Finance Director, which will also see her join the executive team. Since joining UKBIC last year as financial controller, she has shown a strong blend of professionalism, experience and expertise, coupled with a strong track record of delivery, which makes her an ideal for the role." Coventry-based UKBIC is a key part of the Faraday Battery Challenge, a UK Government programme to fast track the development of cost-effective, high performance, durable, safe, low weight and recyclable batteries.
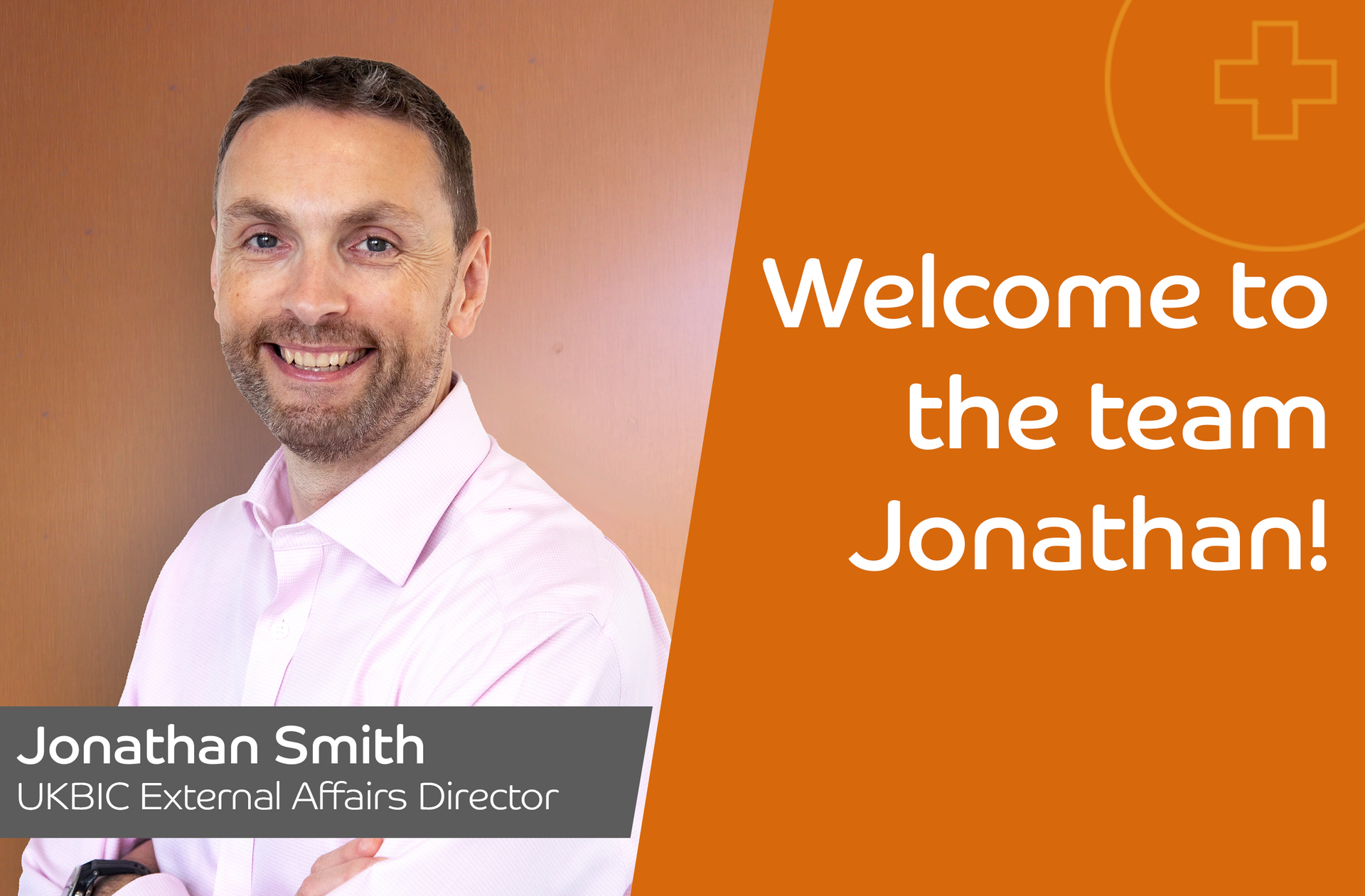
The UK Battery Industrialisation Centre (UKBIC), the national battery manufacturing scale-up facility, has appointed Jonathan Smith to the post of External Affairs Director. Jonathan previously headed up the press teams for FTSE100 Severn Trent Water, E.ON UK and Alstom. During a career spanning more than 20 years, he has led or worked on a wide range of activities and initiatives, including public relations campaigns, internal communications, investor relations, mergers and acquisitions, joint venture communications, and events. Highlights include leading internal and external communications around half and full year reporting to the City, creating programmes and campaigns to support the rollout of new trams and tramlines in Nottingham, leading the issues response during plans to build a new power station in Kent, and being part of a joint venture communications team which helped to build what was then, the world's largest offshore wind farm (the London Array). Jonathan will be responsible at UKBIC for government relations, stakeholder management, communications, public relations, social media, website, marketing and events, and will also work as part of UKBIC’s Executive Team. Jonathan added: “I’m delighted to be joining UKBIC at a time when the battery industry in the UK is growing in importance. There’s a huge amount to be done and I’m really looking forward to finding out all about the facility, our customers, and the wider industry.” Sean Gilgunn, UKBIC’s Managing Director, added: “I’m excited to be welcoming Jonathan to the post of External Affairs Director. Jonathan’s wealth of experience will be hugely important as UKBIC develops its capabilities in what is a fast growing battery sector.” Coventry-based UKBIC is a key part of the Faraday Battery Challenge, a UK Government programme to fast track the development of cost-effective, high-performance, durable, safe, low-weight and recyclable batteries.
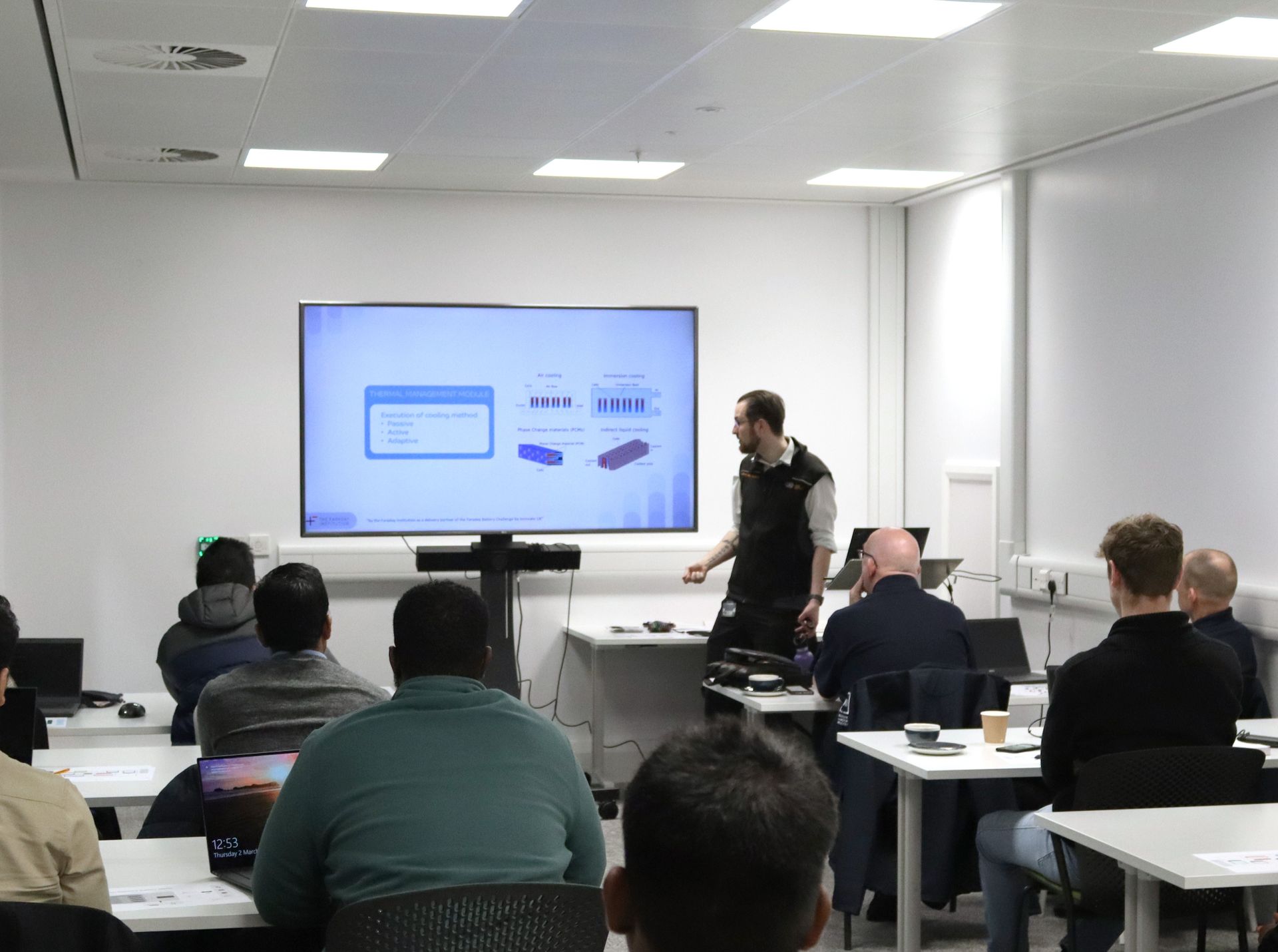
The UK’s national battery manufacturing facility, the UK Battery Industrialisation Centre (UKBIC), is to hold its first publicly available training course for anyone interested in battery manufacturing. The two-day long introduction to battery manufacturing course is open to technicians, managers, researchers, investors, or anyone interested in gaining practical knowledge of the growing battery sector. Delegates will be able to listen to specialists introduce the fundamentals of the battery manufacturing process, hear about the materials required, and the technologies available. They will also be given the chance to tour the state-of-the-art facility and see the giga scale battery manufacturing equipment used in the facility. Future training courses will include ‘Introduction to Designing Sustainable Batteries’, ‘Familiarisation of Battery Module and Pack Design’, and ‘Substance Awareness.’ Jonty Deeley-Williamson, the Head of Learning and Development at UKBIC, said: “With the transition to zero emission vehicles well underway, the need to develop a skilled workforce for the growing UK batter sector is key to unlocking a Net Zero economy. This training course – which will be the first of many - will contribute to this development. We’ve already delivered specialist training to several different organisations, so to be able to deliver our first bookable training course, is a great step for the organisation.” Coventry-based UKBIC, which provides manufacturing scale-up facilities and skills for the battery sector, is a key part of the Faraday Battery Challenge, a UK Government programme to fast track the development of cost-effective, high-performance, durable, safe, low-weight and recyclable batteries. To book a place on the ‘Introduction to Battery Manufacturing’ course, which is being held on 12 and 13 March:
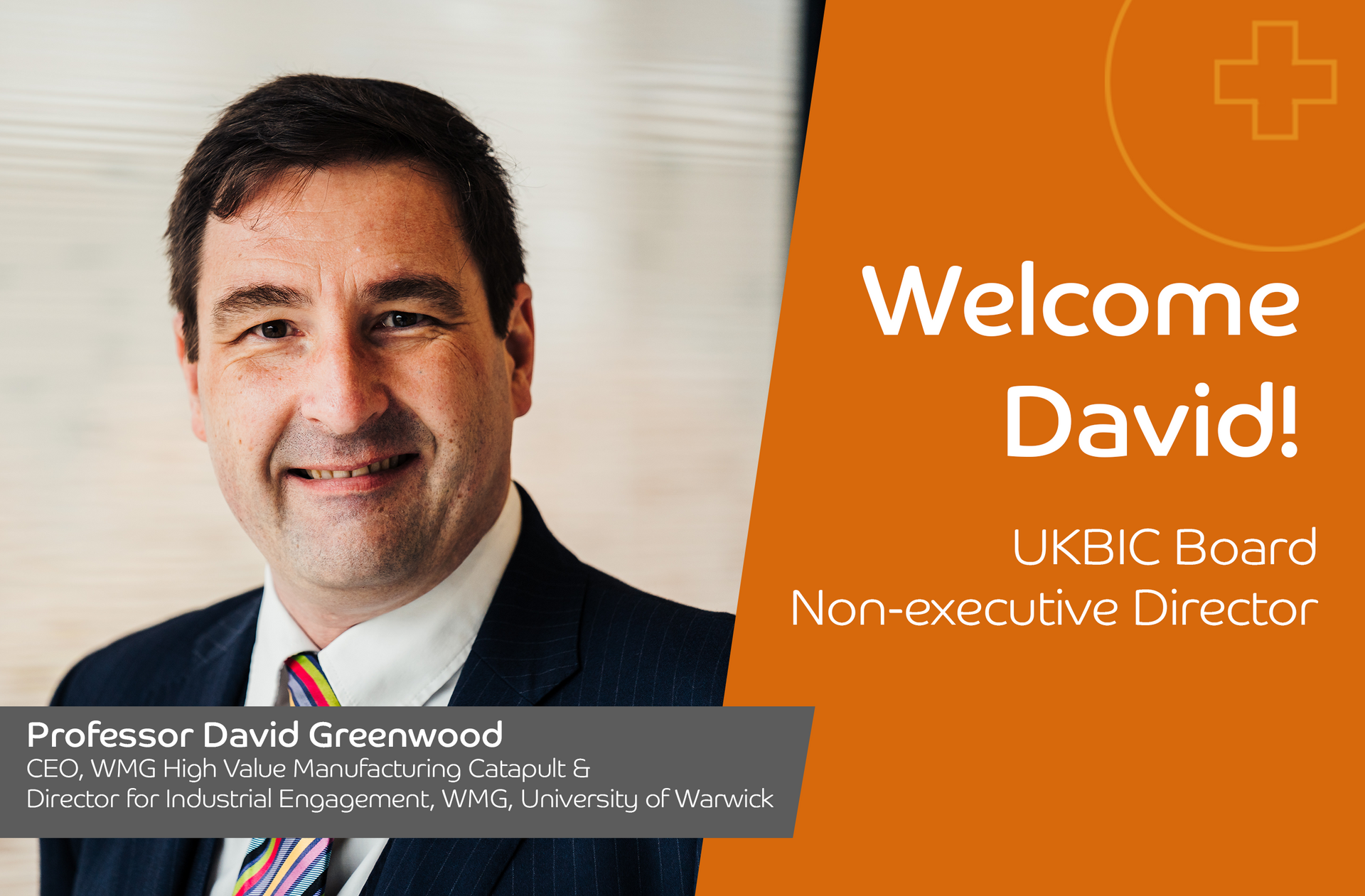
The UK Battery Industrialisation Centre (UKBIC), the national battery manufacturing scale-up facility, has appointed Professor David Greenwood, the CEO of the WMG High Value Manufacturing Catapult and the Director for Industrial Engagement, at WMG, University of Warwick, to the board of UKBIC. David previously led the Energy Directorate at WMG where he led a team of over 200 researchers and engineers, working on a wide range of projects on electrification of transport, spanning several fields, including cars, trucks, boats, off highway machinery, aircraft and motorcycles. Sean Gilgunn, UKBIC’s Managing Director, said: “We are delighted to welcome Professor David Greenwood to UKBIC’s board of directors. His wealth of experience and leadership in battery technology, coupled with his working knowledge of UKBIC, will undoubtedly elevate our capabilities and further strengthen our value to our customers.” Professor David Greenwood added: "I am honoured to join the board of UKBIC and to help UKBIC navigate the complex battery industry. With both AESC and Agratas committed to developing gigafactories in the UK, this is an exciting time to be joining UKBIC’s board.” David moved into academia after 20 years in industry latterly as Head of Hybrid and Electric Systems for engineering consultancy Ricardo UK Ltd. His research spans batteries, electric motors, power electronics, and the integration and control of these for propulsion and energy applications. Professor Greenwood holds advisory and board positions for the Advanced Propulsion Centre, Innovate UK (Faraday Battery Challenge), and the Faraday Institution, and he is a Fellow of the Royal Academy of Engineering. Coventry-based UKBIC is a key part of the Faraday Battery Challenge, a UK Government programme to fast track the development of cost-effective, high-performance, durable, safe, low-weight and recyclable batteries.

Construction work now underway on roof top solar farm on UKBIC The UK Battery Industrialisation Centre (UKBIC), the national battery manufacturing development facility, is set to revolutionise the way it generates energy with an innovative project which will transform its roof into a solar farm capable of generating a peak output of 2.8MW of clean, renewable electricity. In addition to the solar farm, the project will see the creation of two 2MWh Battery Energy Storage Systems (BESS) which will give the facility greater flexibility over when it uses energy, allowing solar energy generated throughout the day to be used overnight. Construction work is set to commence in March 2024. Once fully operational, the new Vital Energi installation will significantly help to reduce the facility’s carbon footprint by 555,000kg per year. Funding for the solar farm is being provided by UK Research and Innovation, via the Faraday Battery Challenge, delivered by Innovate UK. The FBC is a £610m investment programme which supports world-class scientific technology development and manufacturing scale-up capability for batteries in the UK. Sean Gilgunn, UKBIC’s Managing Director, said : “The installation of a solar farm on our roof will be fantastic for UKBIC. This latest investment from UKRI will help us to reduce our carbon intensity and demonstrate good industry practice by making the battery industry greener. The initiative will help to reduce our energy bills and help towards the UK’s goal of achieving net zero by 2050.” Simon Jones, Vital Energi’s Regional Manager for Solar, added , “It’s only right that a world leader in battery development should harness the latest technology and UKBIC are making a significant investment in their green energy future. This project will not only substantially drive down their carbon emissions but will also deliver long-term energy savings and bring stability to their energy costs. “UKBIC’s size means that their roof is a fantastic resource which can be used to house almost 5,000 solar panels across the roof space of its 18,500m2 facility, generating a peak output of 2.8MW, and will be a fantastic technical achievement once completed.” Work is already underway on the solar farm with completion scheduled for the fourth quarter of 2024.
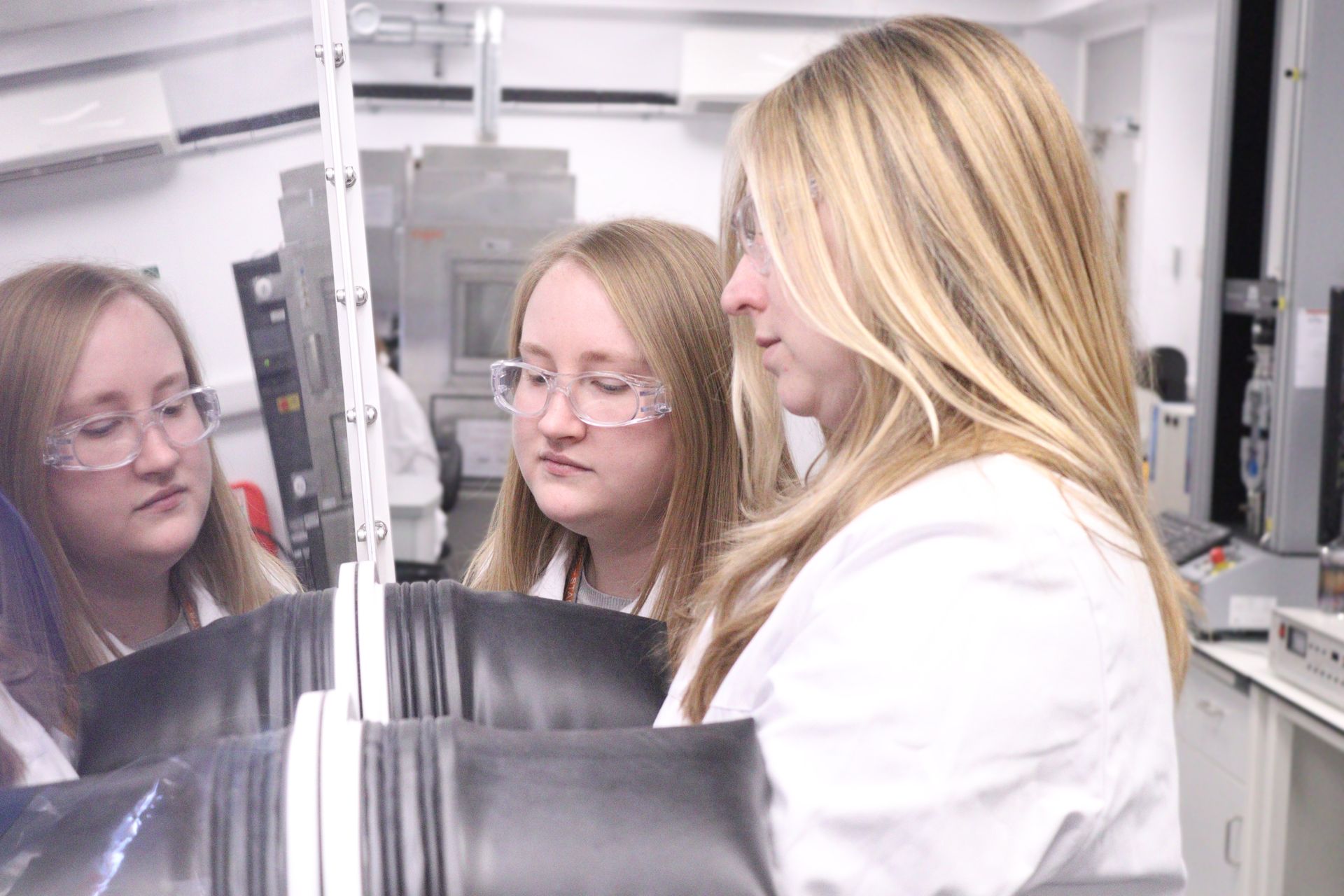
Construction work is now underway on the UK Battery Industrialisation Centre’s (UKBIC) new innovative battery laboratory, which is due to come online during 2024. The enhanced laboratory will boost UKBIC’s capabilities in key areas of battery materials characterisation, cell analysis and forensic activities to support manufacturing development. The laboratory – building on the national facility’s existing testing capabilities - will enable customer materials and cells manufactured and developed on site to be analysed and tested in real-time; and will use a broader array of techniques to provide the lineside data required throughout the scale-up journey. UKBIC’s new 320m 2 battery laboratory space will be four times the size of the facility’s existing testing laboratory. It will enable characterisation of the products that are processed on UKBIC’s existing volume manufacturing line – and will also support the new flexible development line which is due to come online in 2025. This new flexible line will bridge the gap between UKBIC’s existing industrialisation line and earlier Technology Readiness Level (TRL) kilogramme-scale R&D pilot lines available elsewhere. The new capability will have five key areas of focus for manufacturing development: Characterisation – for analytical analysis including material properties such as morphology, crystal structure, elemental and material components. Chemical and physical processing – for the preparation of samples for characterisation and handling of more hazardous samples. Forensics – for the teardown of cells to investigate cell properties and failure modes. Electrochemistry – for advanced electrochemical analysis of manufactured cells including extended cycling and electrochemical impedance spectroscopy. CT Scanner – This enables non-destructive analysis of cells to understand issues and potential failure modes without the need to physically teardown the cell. Funding for the new laboratory is being provided by UK Research and Innovation, via the Faraday Battery Challenge, a £610m investment programme which supports world-class scientific technology development and manufacturing scale-up capability for batteries in the UK. Sean Gilgunn, UKBIC’s Managing Director, said: “The new battery laboratory will be a fantastic resource for our customers in the analysis of battery cells and their components during process development. Being able to better understand the materials and the issues that can occur during the manufacturing scale up process will help our customers develop their battery technologies much more efficiently. Having the capability available on site will be an incredible resource for UKBIC.” Tony Harper, Director of the Faraday Battery Challenge, added: “Having this additional on-site resource will further optimise the industrialisation process for users. Technology developers require significant amounts of continual feedback and data as they develop and scale new manufacturing processes towards commercial production. Having real-time access to this new lineside equipment at UKBIC further enhances the UK’s position in supporting effective battery technology scale-up.”
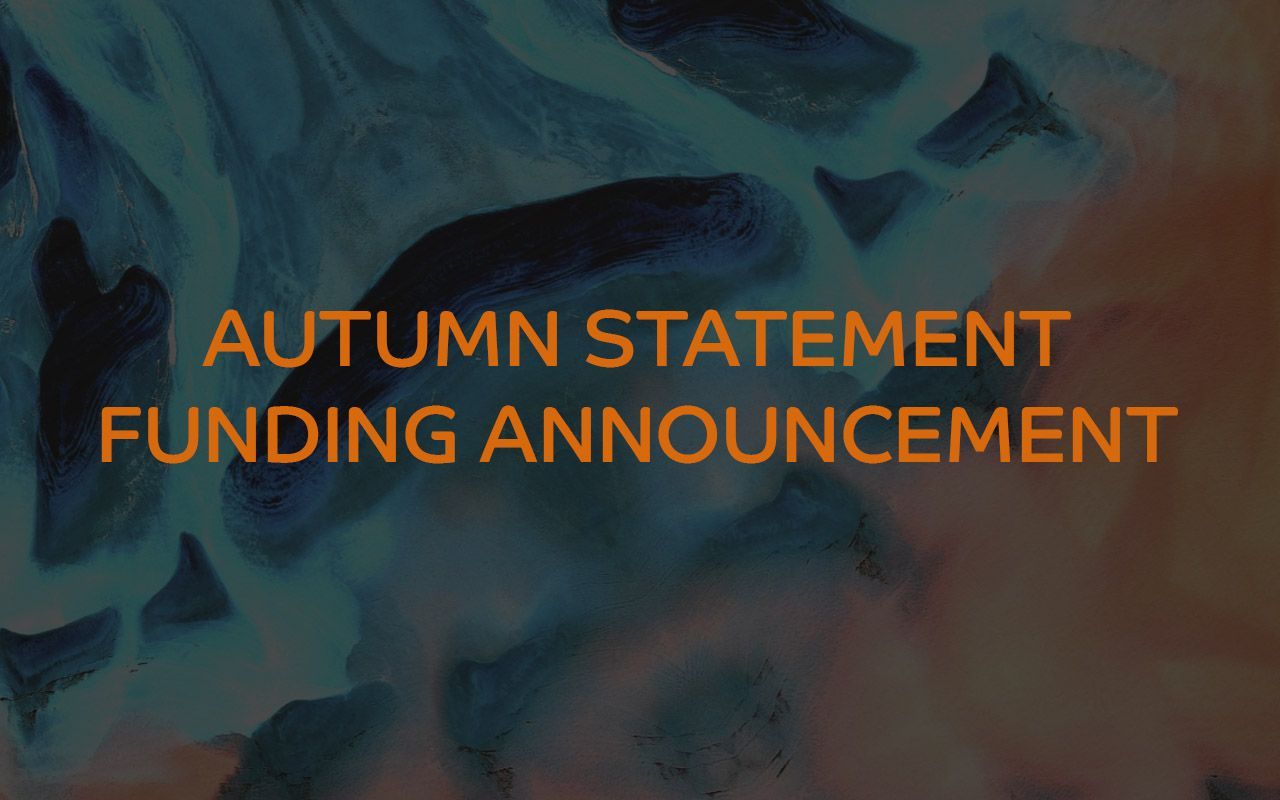
The UK Battery Industrialisation Centre (UKBIC) has secured a further £38m in funding to upgrade the facility’s scale-up capabilities to support innovation projects for high-tech developers and users of battery technologies. The UK Battery Industrialisation Centre (UKBIC) has secured a further £38m in funding to upgrade the facility’s scale-up capabilities to support innovation projects for high-tech developers and users of battery technologies. The new funding, announced as part of the Autumn statement, is principally for UKBIC’s innovative flexible scale-up line, and builds upon the £36m already committed by Faraday Battery Challenge in May. Preparatory work on construction of the facility is already underway. The new funding for the national battery manufacturing scale-up facility will enhance its offering to customers and enable activities including: Additional electrode production equipment to be installed as part of UKBIC’s new flexible scale-up line. The installation of a flexible 800m2 clean & dry Industrialisation space for new manufacturing process demonstration. Development of advanced digital manufacturing capability to transform how data is analysed for innovative products and processes being scaled up at UKBIC. The new flexible scale-up line will bridge the gap between UKBIC’s existing volume industrialisation line and kilogramme scale demonstrator lines available elsewhere. The new capability, which is expected to be operational during 2025, will provide battery developers with an increasingly cost-effective route to market, enabling companies to move from R&D through to large-scale production, without having to use overseas facilities. The funding (announced today) is being provided by UK Research and Innovation, as part of the UK Government’s £610m Faraday Battery Challenge, a national investment programme which is delivered by Innovate UK. The Challenge supports world-class scientific technology development and manufacturing scale-up capability for batteries in the UK. The new developments include: A secondary electrode line will offer new modular equipment capacity for coating, drying and calendering of electrodes, allowing more innovative processing methods to be developed and trialled alongside existing customer scale-up activities. The creation of a specialist 800m² flexible industrialisation space will provide a dedicated clean and dry room environment, which can be subdivided for different use cases, for customers to develop their own individual processes or machinery under carefully controlled environmental conditions. The introduction of advanced digital manufacturing at UKBIC will provide customers with real-time knowledge transfer by giving access to data analytics, advanced machine learning, and tools for learning and visualisation increasingly required by technology developers, through the process of continually understanding, developing and improving. The funding will enable companies to better understand new data in real-time, but also provide a vital foundation for future developments in smart manufacturing for the battery industry. Tony Harper, Director of the Faraday Battery Challenge, said: “This new funding will help make UKBIC’s world-class scale-up facilities an even more attractive proposition to domestic and global battery developers. UKBIC’s flexible scale-up line, in addition to the new dedicated industrialisation space, and the introduction of digital manufacturing capability will further help position the UK and UKBIC as the place to go for battery development and scale-up.” Sean Gilgunn, UKBIC’s Managing Director, added: “This latest funding announcement is fantastic news for UKBIC and the battery industry. The investment in the new equipment and capability will mean that many more customers will be able to use the facility seamlessly develop battery manufacturing through to large-scale demonstration. The added introduction of digital manufacturing at the facility will provide customers with an even better data-driven understanding of their manufacturing processes, a capability which customers will increasingly expect as the industry evolves.” The Coventry-based facility, which opened in July 2021, is used by organisations with new or existing battery technologies and provides battery manufacturing scale-up and skills for the battery sector.
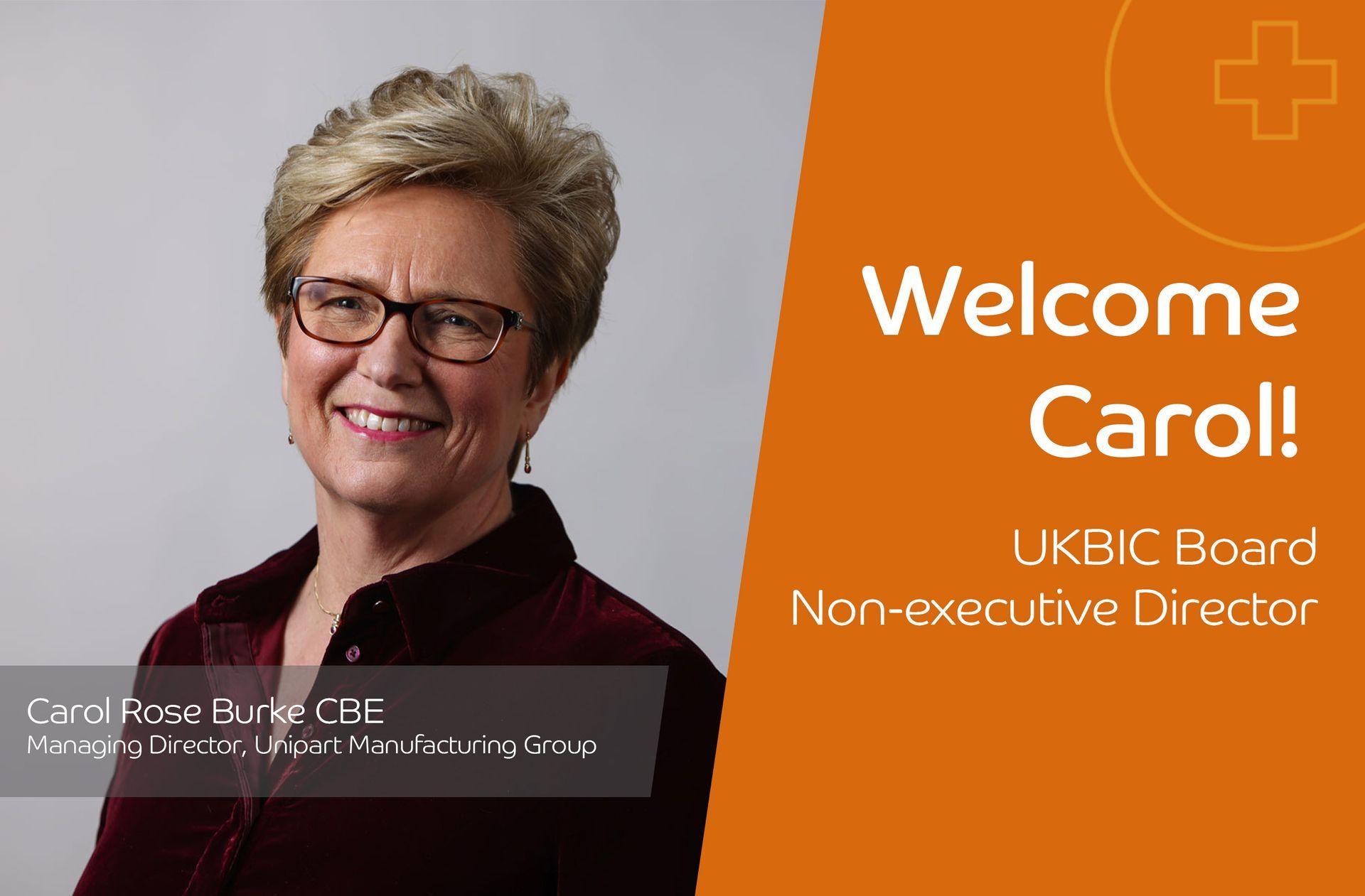
The UK Battery Industrialisation Centre (UKBIC), the national battery manufacturing scale-up facility, has appointed Carol Rose Burke CBE, the Managing Director of Unipart Manufacturing Group (UMG), to its board as a non-executive director. Having joined Unipart in 1994, Carol is one of the UK’s leading advocates for manufacturing and engineering, and is responsible for UMG’s ‘Manufacturing Partner’ strategy, created to support the automotive sectors shift away from the internal combustion engine to alternative forms of propulsion. One of UMG’s most recent projects has brought together their expertise in Tier 1 manufacturing, with WAE Technologies’ design, to create Hyperbat Limited. This joint venture has successfully begun manufacturing batteries for the world’s fastest supercar, the Lotus Evija. Sean Gilgunn, UKBIC’s recently appointed Managing Director, said: “I am delighted with Carol’s appointment to the board. With a career spanning more than 30 years, her experience and insight will be invaluable to us as we develop our capabilities in the battery industry. Carol’s experience in bringing new technologies to market, and ultimately transferring this expertise into non-automotive sectors, will be a fantastic asset to UKBIC and the wider battery industry.” Carol Rose Burke CBE added: “As a passionate advocate for manufacturing and engineering in the UK, I’m delighted to be joining the board of UKBIC. With the transition to electrification and the global move to zero emission vehicles well underway, and with AESC and Tata Group committed to building battery manufacturing plants in the UK, this is a really exciting time to be joining UKBIC.” Coventry-based UKBIC is a key part of the Faraday Battery Challenge, a UK Government programme to fast track the development of cost-effective, high-performance, durable, safe, low-weight and recyclable batteries.
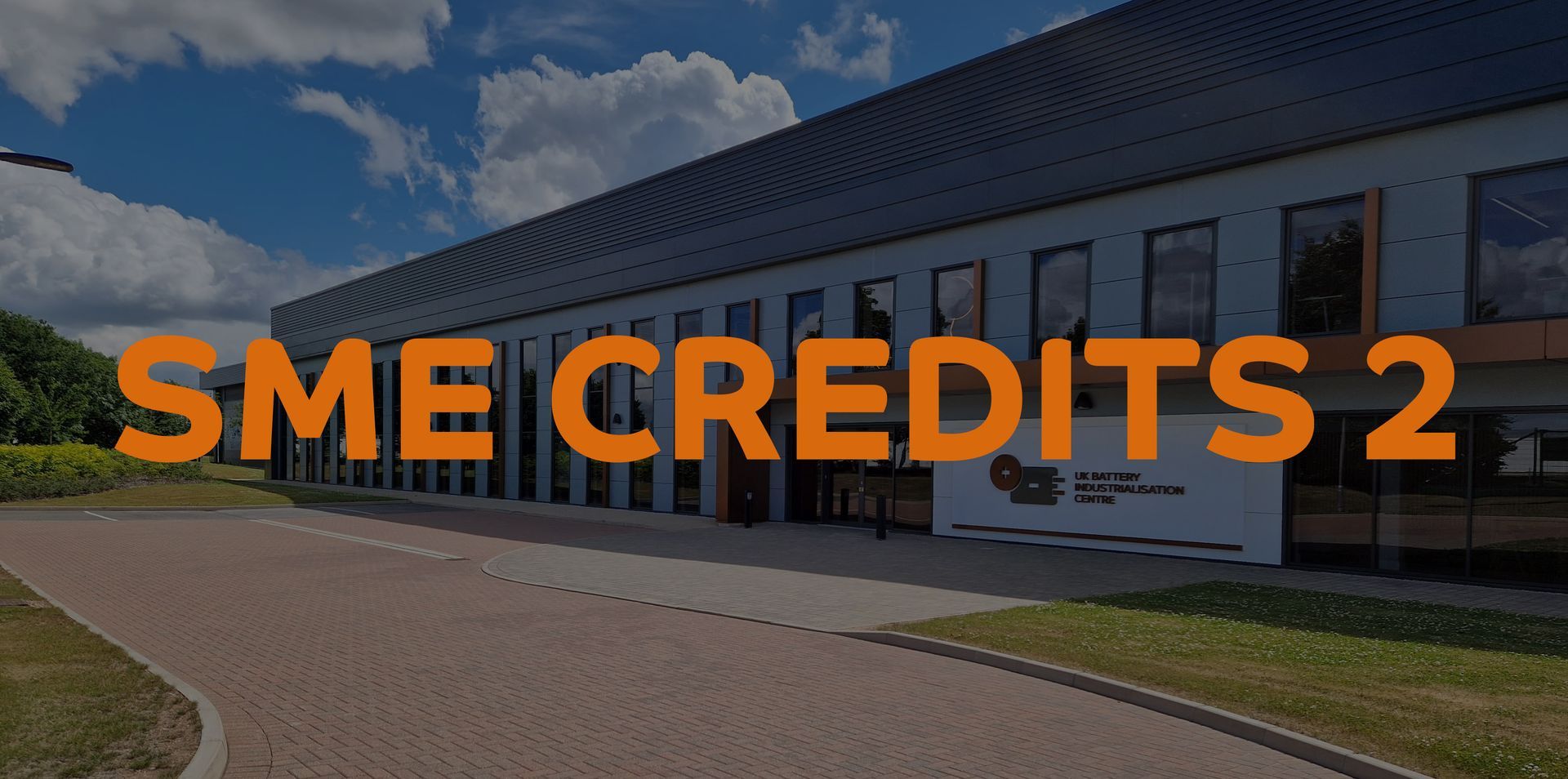
UKRI’s Faraday Battery Challenge, delivered by Innovate UK will invest up to £1.5m in innovation scale up projects in January 2024 to fund UKBIC SME credit Round 2. Building on the success of the first SME Credit competition in May of this year, the new competition will: support small to medium sized enterprises (SMEs) research and development for the scale-up of battery technologies within the UK support small to medium sized enterprises (SMEs) to access the UK Battery Industrialisation Centre (UKBIC) and demonstrate technologies at suitable scales to customers increase engagement with UK Battery Industrialisation Centre (UKBIC) move UK battery innovations from technological potential towards commercial capability, including scalability and design for manufacture develop and secure material and manufacturing supply chains for battery technologies in the UK Important information: Funding support for eligible costs will be confirmed once the formal call is published. Competition timeline (dates TBC): 29 November 2023, Pre-competition engagement event at UKBIC facility January 2024, Competition opens January 2024, Online Competition Briefing event March 2024, Competition closes July 2024, likely start dates for projects End of March 2025, all projects must have been completed Pre-competition Engagement Event UKBIC are hosting a pre-competition event, allowing you to learn more about our facility and talk to our Business Development Team about how to apply. Pre-competition engagement event, 29 November 2023 at UKBIC Facility in Coventry: Introduction to Faraday Battery Challenge Introduction to UKBIC and scope of facilities (especially companies new to using UKBIC) Bidding for SME Credits programme Benefits of SME Credits UKBIC timeline to support competition 1-2-1 discussions with UKBIC team of project idea
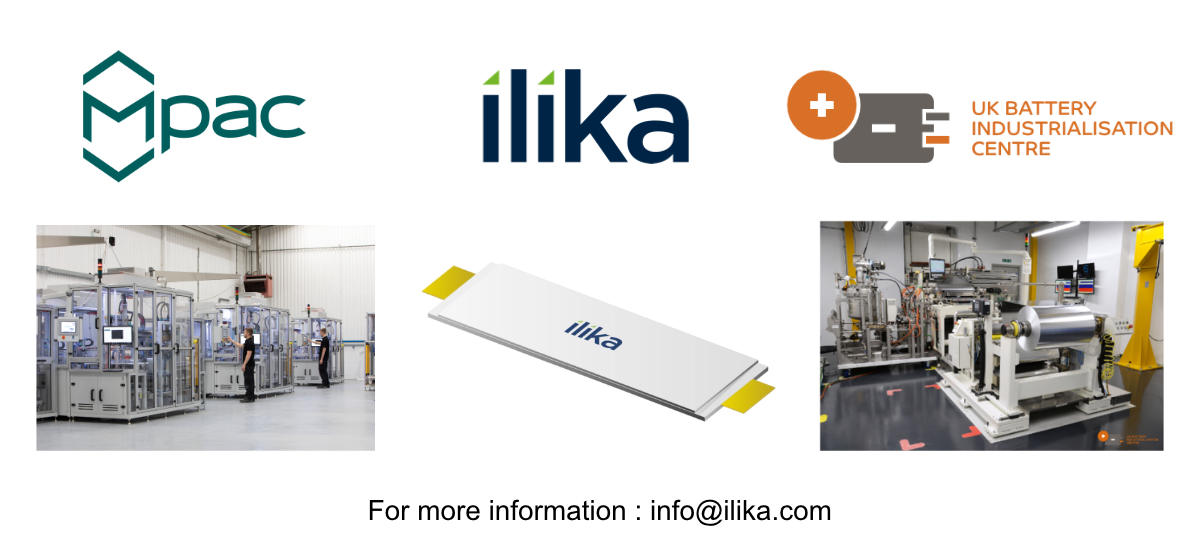
Ilika, a pioneer in solid-state battery (SSB) technology, is pleased to announce it is leading a 16-month, £2.7 million Automotive Transformation Fund (ATF) project, partnering with Mpac Group plc (Mpac) and the UK Battery Industrialisation Centre (UKBIC). Codenamed SiSTEM and commenced 1 October 2023, the project will develop a 1.5MWh SSB assembly line capable of delivering Ilika’s A-sample SSB pouch cells to automotive OEMs and Tier 1s. Additionally, UKBIC will undertake physical trials to demonstrate Ilika’s SSB electrodes at GWh scale. The UKBIC facility, based in Coventry, UK, provides the missing link between battery technology, which has proved promising at laboratory or prototype scale, and successful mass production. SiSTEM follows on from the successful BUS100 programme , which concluded that part of Ilika’s SSB process could in principle take place using some of the equipment used for lithium-ion batteries (LIB) manufacturing, such as that present at UKBIC. In SiSTEM, UKBIC’s formulation and coating lines will be trialled with Ilika’s SSB chemistry, in order to verify the expectations from BUS100. It is indeed very important, in order to enable adoption of SSB, that the manufacturing of this novel technology can re-use equipment invested in by the LIB industry as much as possible. In fact, feasibility study SOLSTICE (a collaboration between Ilika and Comau) concluded that there exist no barrier to scaling-up SSB and that over 2/3 of the required tools already exist in LIB factories. Mpac is a global engineering and service provider of automation and packaging solutions. They design, precision engineer and manufacture high-speed automation solutions within key sectors including Clean Energy. In SiSTEM, Ilika and Mpac will be working closely to design, build and commission the SSB assembly line which is expected to be fully operational by H1 2025. It was indeed concluded in projects BUS100 and SOLSTICE that assembly of SSB pouch cells may differ somewhat to that of LIB: this project will design the required automated tools for pouch cell assembly, which will be used by Ilika for the production of A-samples but will also be the blueprint for future scale-up. Project SiSTEM will run in parallel with Project HISTORY , which will finalise the technical development of Ilika’s prototype automotive A-sample SSBs. The ATF is a UK funding programme created to support large-scale industrialisation. Up to £850 million of funding will be invested in developing a high-value end-to-end electrified automotive supply chain in the UK. The fund is highlighted as an important mechanism to reach targets in UK Government’s 10-Point Plan for a green industrial revolution and its Transport Decarbonisation Plan. Graeme Purdy, Ilika CEO, stated: “Project SiSTEM builds upon previous ATF support in Project BUS100 which found that with minor adaptations, Ilika’s electrodes could in principle be produced in volume on the UKBIC lines. Project SiSTEM will undertake those physical trials, proving Ilika’s technology can be successfully scaled. Our collaboration with Mpac will see the development of a scaled SSB assembly line which will be capable of delivering A-sample automotive pouch cells for testing in 2025. This is an important step in Ilika’s roadmap, enabling us to engage closer with OEM’s as we start to deliver SSB cells into their test programmes.” Julian Hetherington, Director of the Automotive Transformation Fund, said: “We are delighted to be able to support Ilika’s project seeking to validate higher-scale SSB manufacturing processes and which utilises the world-class facilities at UKBIC to demonstrate roll-to-roll coating of solid state materials. SSB technologies have the potential to be transformational in vehicle battery pack design due to their stable nature and open up applications possibilities at higher safe operating temperatures.” Adam Holland, Chief Executive Officer at Mpac Group plc expressed his enthusiasm: “We are thrilled to announce our new partnership with Ilika and UKBIC after the successful award of the prestigious ATF grant for Project SiSTEM. Mpac is a market leader in complex automation, and we are eager to leverage our expertise in developing a cutting-edge innovative solution that will enable the reliable assembly of solid state batteries. This project not only demonstrates our commitment to technological advancement but also aligns with the UK government's vision for a cleaner and more sustainable world." Sean Gilgunn, Managing Director of UKBIC said: “ We’re delighted to be working with Ilika on trials to support the development of the Company’s solid state battery technology. Being able to scale up and demonstrate manufacturing innovation for battery technologies at UKBIC is a valuable resource for the UK’s growing battery sector. ”
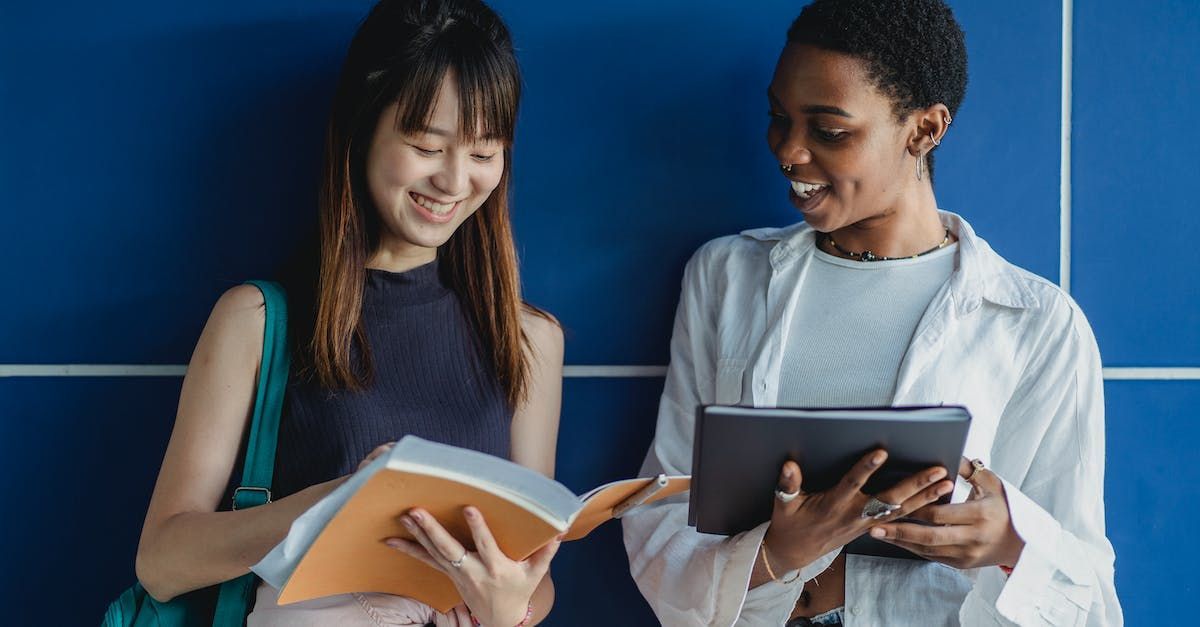
Sharing expertise in electrode slurry characterisation for coating scale up optimisation. A Faraday Institution industry fellowship has been set up to facilitate the sharing of expertise between the UK Battery Industrialisation Centre (UKBIC) and the Energy Materials Group at the University of Birmingham, led by Professor Emma Kendrick and Dr Carl Reynolds. Prof Kendrick is work package leader on the Faraday Institution’s Nextrode project investigating smarter slurry cast electrodes. The fellowship will facilitate the sharing of knowledge in the areas of electrode slurry characterisation and modelling. It will improve the ability to predict the rheology of electrode slurries as they are scaled up from lab to production scales, so reducing coating line dial-in times, scrap rates and improving product quality. The aims of the 12-month fellowship are to: Further develop the understanding of how formulation impacts slurry and coating processability. Determine best practice for slurry characterisation. Understand the impact of slurry rheology of moving from 1 litre, 10 litre and 220 litre mix. Provide rheological parameters as inputs to computational fluid dynamics (CFD) models that can be used to predict slurry coat-ability and inform initial process parameters for production. Transfer knowledge of slurry characterisation to UKBIC. For UKBIC the fellowship will additionally: Further populate UKBIC’s database of input parameters used for CFD modelling and future AI designed cell optimisation tools. Enable the organisation to develop a competitive baseline for manufacturers to test their new technologies against. Further mitigate the risk of scale-up for future technology developers using UKBIC facilities allowing them to reach market more quickly. Ensure that UKBIC’s customers, who use its electrode capability, advance the development of their slurries for industrialisation. The ongoing work will help UKBIC to bring in teams to assist in the analyses of slurries and coatings to minimise coating defects and other potential downstream process issues. Researchers at the University of Birmingham (and Nextrode project) will benefit from the collaboration by further developing: An understanding how parameters scale up onto manufacturing lines. Experience in tailoring research for manufacture. Exposure to CFD modelling and simulation Ameir Mahgoub, Head of Product Engineering at UKBIC, said: “The ongoing collaboration between UKBIC and Nextrode is helping to tackle real industry challenges and de-risk barriers to scale-up. The collaboration demonstrates the Faraday Battery Challenge’s role in marrying research, innovation and scale-up to deliver positive impact for the UK battery industry. It further supports UKBIC’s mission to be the place to go for battery industrialisation. The project will enable UKBIC’s electrode customers to benefit from the knowledge we’ve learnt in the development and coating of their slurries.” The Faraday Institution and UKBIC are both key delivery partners for the Faraday Battery Challenge at UK Research and Innovation, which is delivered by Innovate UK. The Challenge is making the UK a science and innovation superpower for batteries, supporting the UK's world-class battery facilities along with growing innovative businesses that are developing the battery supply chain for our future prosperity. Its aim is to build a high-tech, high-value, high-skill battery industry in the UK.
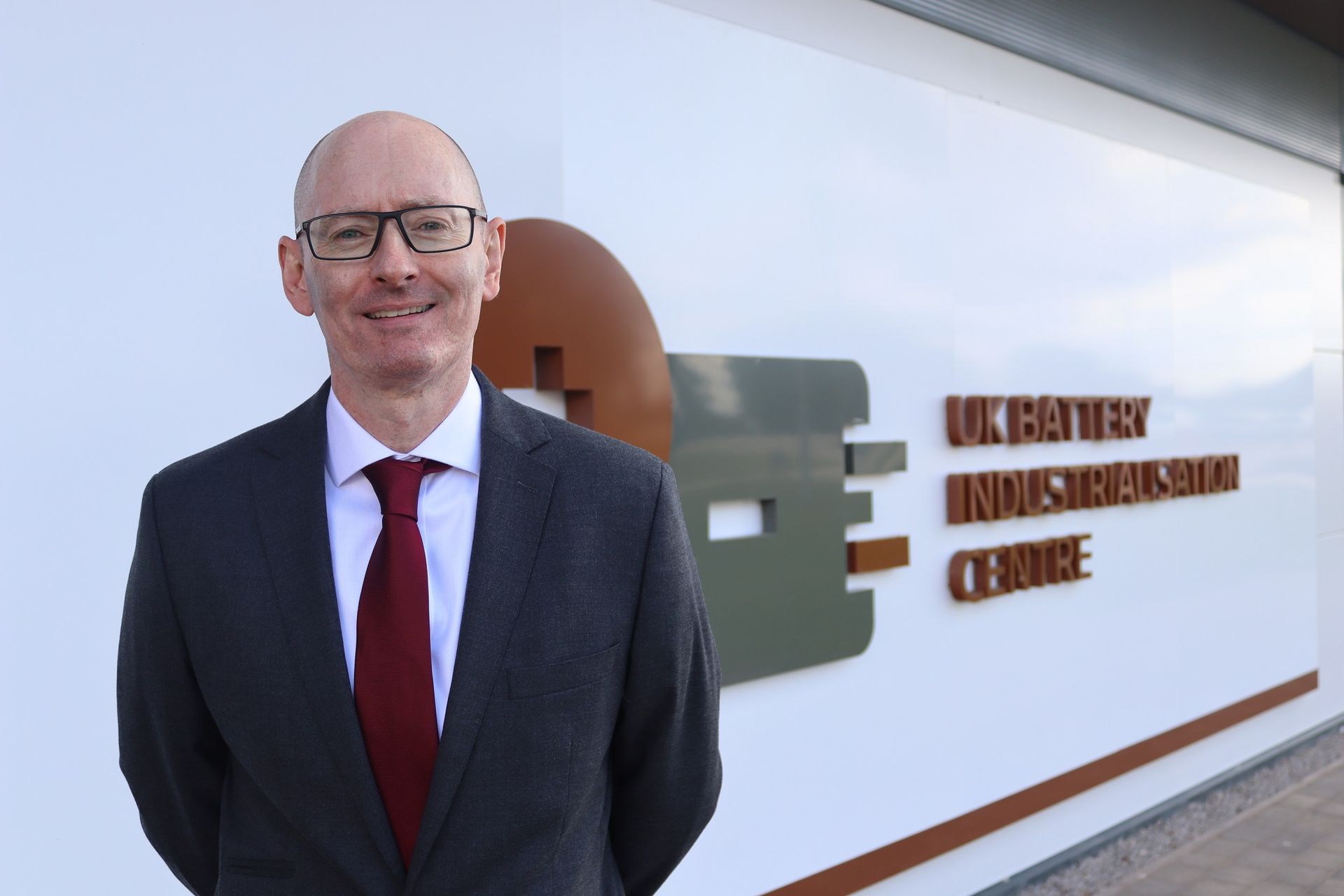
Sean Gilgunn appointed UKBIC's new Managing Director The UK Battery Industrialisation Centre (UKBIC), the national battery manufacturing scale-up facility, has appointed Sean Gilgunn as its new Managing Director. Sean, who will take up the post at the Coventry-based £130m facility in October, joins UKBIC from Johnson Matthey where he has worked across various business areas, most recently as Global Procurement Director, Strategy & Operations. Prior to this, Sean was based in Poland as General Manager and President of the Board of Directors for JM Battery Systems, a leading manufacturer of batteries across a wide range of applications. He has also spent a number of years leading global business units and key accounts focusing on critical markets including South Korea, China and South East Asia more broadly. Sean was appointed by the UKBIC Board to lead the organisation, following the announcement in April that incumbent, Jeff Pratt, will be leaving at the end of his appointment in September 2023. UKBIC is a key part of the Faraday Battery Challenge, a UK Government programme to fast track the development of cost-effective, high-performance, durable, safe, low-weight and recyclable batteries. Sean, the incoming Managing Director, said: “I am really pleased to have been appointed to the role of Managing Director for UKBIC. The opportunity to lead an organisation whose work is pivotal to the UK’s ambition to create a strong and sustainable battery manufacturing industry is truly unique. I am excited by the opportunity to drive forward UKBIC’s strategy in supporting the growing industrial opportunity for battery production at scale, and to work with our partners across the UK ecosystem to ensure we are providing the right environment for businesses to thrive.” Richard Moon, Chairman of UKBIC’s Board and Director of Property Services & Development, Coventry City Council, commented: “I’m delighted that Sean has taken on the role of Managing Director at UKBIC. He brings an impressive background in strategic and operational leadership, which includes more than 20 years of international commercial and management experience in the B2B battery systems, automotive and chemical sectors. It’s this experience which will be vital in guiding the organisation forward in the years ahead.” Tony Harper, the Faraday Battery Challenge’s Director, added: “This is a hugely exciting time for Sean to be joining UKBIC. With the global transition to zero emission vehicles well underway, and with the commitment from AESC and Tata Group to build battery manufacturing plants in the UK, we are seeing strong signs that the UK is on the right path to delivering a world class battery industry. I’m delighted that Sean will be leading UKBIC to enable manufacturing opportunities as part of our joined-up ecosystem.” -ends-
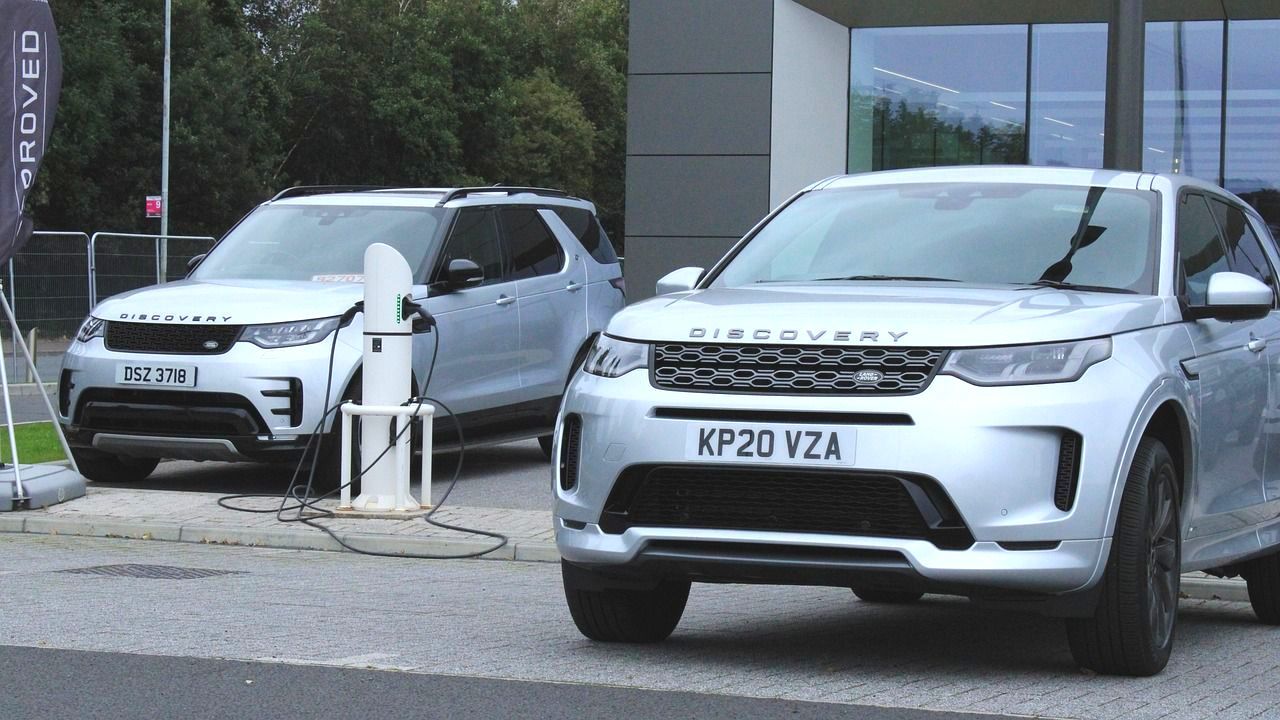
UKBIC's Managing Director, Jeff Pratt, said: "The announcement is a significant landmark for UK industry, including the automotive sector and its supply chain, as well as the construction industry and other sectors planning to source batteries for electrification. The new gigafactory, at 40GWh, will be one of the largest in Europe, and the creation of direct and indirect jobs will significantly boost employment and economic opportunity and bring vital long-term stability for the future of UK automotive. “Today’s news, coupled with last year’s gigafactory investment announcement from AESC in Sunderland, sends strong signals to global investors and those working in the battery sector, that the UK is a country with a battery industry worth investing in. “UKBIC will continue to support companies who are looking to scale up battery production, up-skill their workforce and participate in the UK Government-funded Faraday Battery Challenge’s mission to build a high-tech, high-value, high-skill battery industry in the UK."
SME battery developers will share circa £1m through three projects to support research and development for the scale-up of battery technologies in the UK. Successful projects will enable complete cell development to proving electrode manufacturing with novel materials at scale. Three UK battery developers have been awarded £1 million in funding to support their scale-up journey from technological potential towards commercial capability. The three project winners were announced at the Battery Cells and Systems Expo, at the National Exihibition Centre (NEC) in Birmingham, they are: Addionics AMTE Power Nyobolt The small and medium sized enterprise (SME) battery developers were awarded the £1 million funding through the UK Research and Innovation (UKRI) funded Faraday Battery Challenge (FBC). FBC is a £541 million investment programme which supports world-class scientific technology development and manufacturing scale-up capability for batteries in the UK. Addionics Addionics project will utilise technology developed by Addionics for 3D current collector fabrication that has shown significant battery performance improvements The project will target complete cell development taking Addionics 3DCC material through mixing, coating, calendaring and slitting, up to cell assembly, formation and ageing. This will build on the success of their earlier Innovate UK-funded project. AMTE Power AMTE’s Power Cell Commercialisation (PCC) project will support their production yield improvement for the scale-up of their ultra high power (UHP) pouch cell in the UK. The UHP cell is a potentially market leading lithium nickel-cobalt-aluminum oxide (NCA) chemistry pouch cell, capable of up to 40C continuous discharge and 100C pulsed discharge, at an energy density of 150 Watt-hours per kilogram. The project will also help to further develop and secure material and manufacturing supply chains for battery technologies in the UK. Nyobolt Nyobolt is commercialising ultra-fast charging, high power battery technologies for applications ranging from power tools to automotive and is currently scaling production to meet customer demand. This project will optimise for quality and speed the giga-scale manufacturing at the UK Battery Industrialisation Centre (UKBIC) of Nyobolt’s electrode material. Supporting UK battery industry These projects will also enable UK competitiveness across the battery value chain by: supporting SME research and development for the scale-up of battery technologies within the UK supporting SMEs to access the FBC funded UKBIC, the UK’s national battery manufacturing development facility help demonstrate technologies at suitable scales to customers move UK battery innovations from technological potential towards commercial capability develop and secure material and manufacturing supply chains for battery technologies in the UK The three projects demonstrate a balance between specific technical, market and business requirements. Moving battery innovation from technological potential towards commercial capability, these projects aim to ensure that the UK can meet its net zero commitments in the required timescale. Innovative battery technology Claire Spooner, Challenge Deputy Director for the FBC, speaking at the Battery Cells and Systems Expo at the NEC, Birmingham, said: The UK is home to some of the most innovative battery technology companies in the world. For the UK to prosper from the transition to electrification, it is important that we not only develop the most advanced and highest performing batteries but that we also scale these technologies in the UK. These projects provide a crucial next step in the technology scale-up journey for AMTE Power, Addionics and Nyobolt. Utilising the world-class battery manufacturing facilities at the UK Battery Industrialisation Centre will enable them to de-risk the manufacturing process of their innovations at giga-scale and prove technology performance to their customers and investors. Developing the UK battery ecosystem  Naseer Ahmed, UKBIC’s Commercial Director, added: We are delighted that the Faraday Battery Challenge is supporting these home-grown battery developers with access to UKBIC. The creation of a home-grown cell supply chain is essential to the future of the UK battery sector, which is why this funding is absolutely vital. Only by nurturing, growing and developing the UK battery ecosystem can the industry become truly successful.
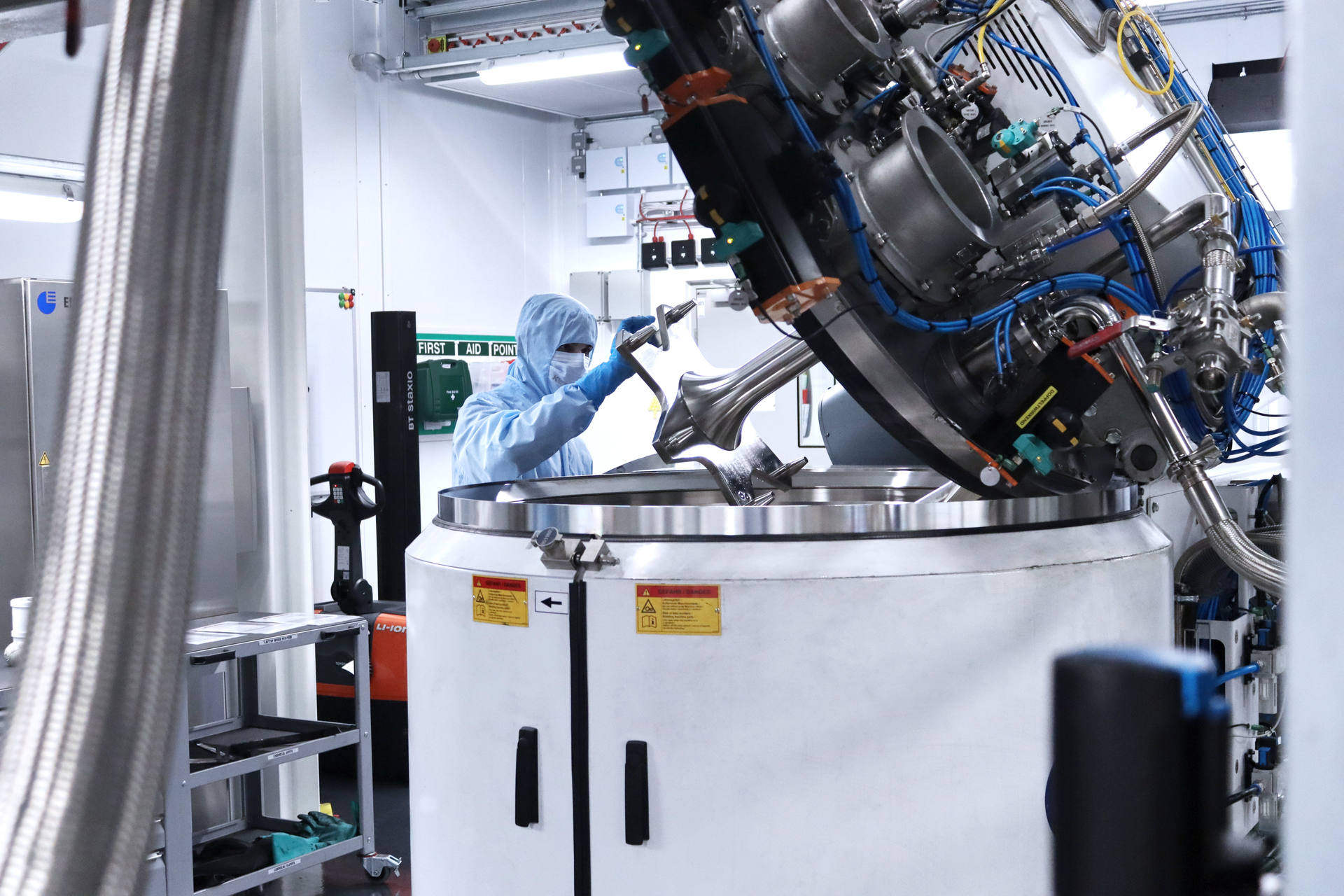
The UK Battery Industrialisation Centre (UKBIC), the UK’s national battery manufacturing scale-up facility, has secured £36 million in funding for the facility’s new Flexible Industrialisation Line (FIL.) The new line will bridge the gap between UKBIC’s Volume Industrialisation Line (VIL) and existing kilogramme scale demonstrator lines available elsewhere. Construction of the new flexible line is set to get underway in September of this year, with the equipment coming online during 2025. The new line will provide battery developers with a cost-effective route to market, enabling companies to move from R&D through to large-scale production, without having to take cell development outside of the UK. Once completed, FIL will be owned by UKBIC but operated jointly by UKBIC and WMG to facilitate effective transfer from research into industrialisation. Funding for the new line is being provided by UK Research and Innovation, as part of the UK Government’s Faraday Battery Challenge, a £541 million (€621.87 million) investment programme which supports world-class scientific technology development and manufacturing scale-up capability for batteries in the UK. Since it opened in July 2021, UKBIC has successfully supported 24 advanced scale up and industrialisation battery technology projects across numerous battery developers and end users, supported by its existing facilities and capabilities. Dr Ahmad Mohsseni, UKBIC’s Chief Technology Officer, who announced the initiative during a presentation at the The Battery Show Europe in Stuttgart, Germany, said: “The construction of this new facility will be hugely significant for UKBIC and the UK battery industry. Once built, this new Flexible Industrial Line, will provide companies with a unique platform to enable them to get a foot on the scale-up ladder, from Research & Development through to volume manufacturing. “Companies can find it incredibly difficult to source the volume of advanced materials required for early scale trial and demonstration – the smaller the quantity needed, the better for executing early-stage optimisation cycles and production trials. To date, we have mitigated the amount of material and time required for running our larger scale manufacturing equipment for early customers through developing techniques such as half-width coating, running at slower speeds and half mix batches of slurry, but more is needed to support industry with a truly cost-effective route to commercialisation.” Minister for Industry and Economic Security, Nusrat Ghani, added: “The battery industry will be essential in helping us grow the green economy of the future, and this funding secured by the UK Battery Industrialisation Centre forms part of the Government’s landmark support for the industry so far. The Centre’s new Flexible Industrialisation Line will provide a significant boost to both research and production for UK battery companies, helping to drive forward our ambition to make the UK a battery science superpower.” Tony Harper, Director of the Faraday Battery Challenge, commented: “When customers leave laboratories or pilot lines for product development, there is still a huge amount of process iteration required before cells can be successfully scaled at the cost, quality, and performance required for giga-scale production. “UKBIC’s existing Volume Industrialisation Line is ideally placed for the later stages of manufacturing process to validate that product can be made in volumes of tens of thousands and above. This is where it becomes cost-effective and representative of an industrial plant run, and therefore a vital part of the commercialisation process. The gap for the UK is in early production quantities, between the low hundreds and low thousands of cells, which is where our new line will come in.” Jeff Pratt, UKBIC’s Managing Director, added: “The scaling up of battery cells is notoriously difficult, time-intensive, and complex. When technology developers get to the point of trying to attract investors or customers, they are looking for high quality control and industrial standards, which is a key reason for turning to UKBIC. The challenge is that they may have a significant programme of product and process developments to be completed before they can continue. “Our specialist high-volume manufacturing equipment is perfect for those organisations in need of representative scale-up, but not necessarily for those organisations at an earlier technology readiness stage of their development. That’s where FIL, once built, will come in.” Professor David Greenwood, Director for Industrial Engagement and CEO of the High Value Manufacturing Catapult at WMG, said: “The new Flexible Industrialisation Line at UKBIC fills the strategic gap between Proof-of-Concept cells at WMG and full-scale manufacturing on the UKBIC Volume Industrialisation Line. This new facility will be operated jointly by UKBIC and WMG so as to bring the best battery science and technology together with the best manufacturing knowledge, allowing companies to manufacture sample batches of many thousands of innovative cells, accelerating commercial development.”
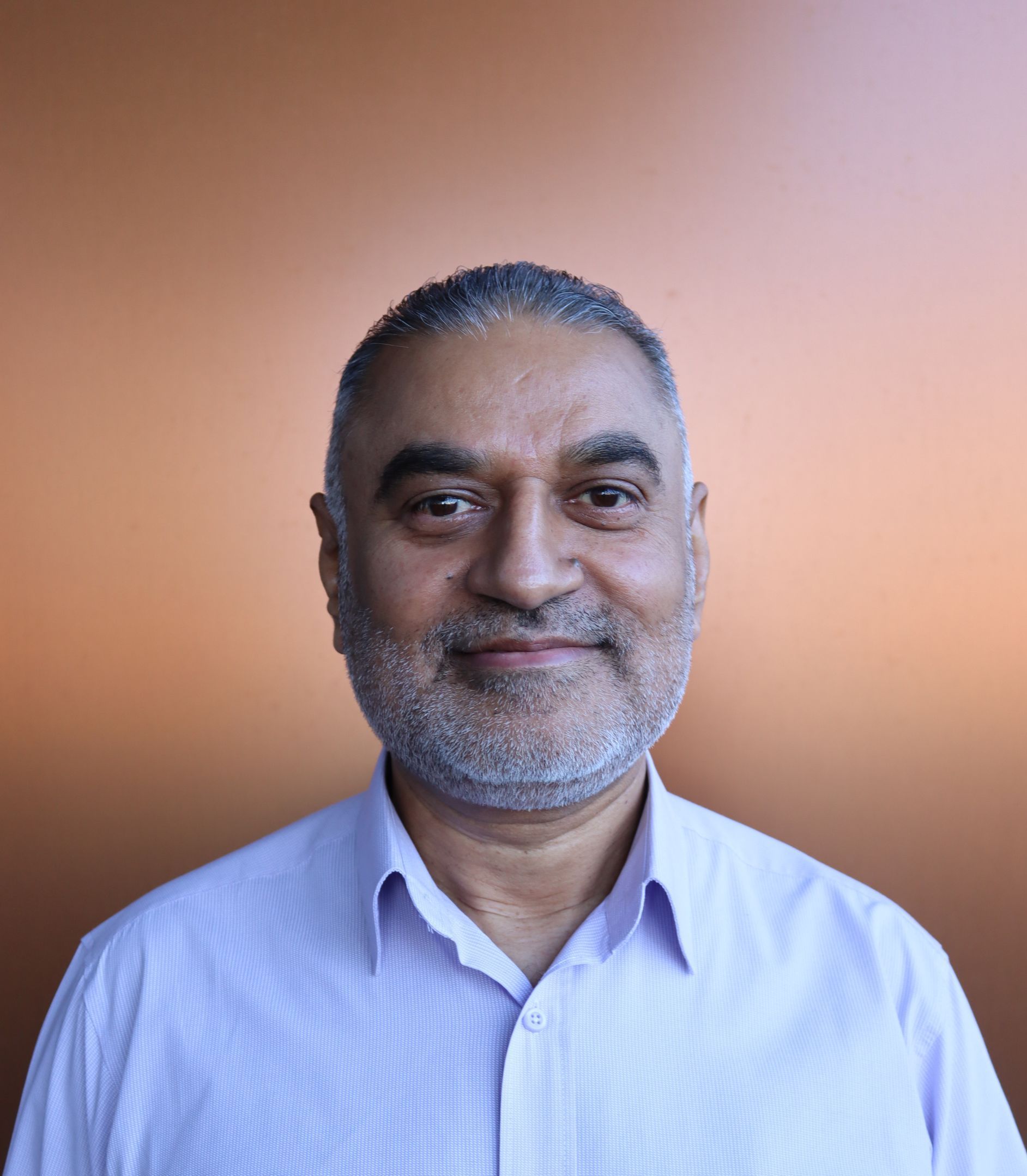
The UK Battery Industrialisation Centre (UKBIC), the national battery manufacturing scale-up facility located in Coventry in the West Midlands, has appointed Naseer Ahmed to the post of Commercial Director. Naseer, who joined UKBIC as Business Development Manager in June 2021, has previously worked in research, development and manufacturing organisations for a range of telecommunications, space and battery companies, including Ericsson, Fujitsu, Airbus Defence and Space and ABSL. The newly appointed Commercial Director, who will start in his new role on Tuesday May 1, will be responsible for business development, sales, and customer projects, and will also work as part of UKBIC’s Executive Team. Naseer Ahmed, UKBIC Commercial Director, said: “I’m delighted to have been promoted to the post of Commercial Director at UKBIC. Helping our customers get the most from working with UKBIC has the potential to have a huge impact on the growth of the UK battery sector, and I am looking forward to developing this further.” Jeff Pratt, UKBIC’s Managing Director, added: “I’m pleased that Naseer has taken the role of Commercial Director at UKBIC. Since joining the business in 2021, he has been a key player in our fantastic Business Development team, helping us to grow our commercial offering and supporting UKBIC’s customers in their scale-up journey.” UKBIC is a £130 million 20,000 square metre pioneering facility, which provides the missing link between battery technology, which has proved promising at laboratory or prototype scale, and successful mass production.  UKBIC is a key part of the Faraday Battery Challenge, a UK Government programme to fast track the development of cost-effective, high-performance, durable, safe, low-weight and recyclable batteries.
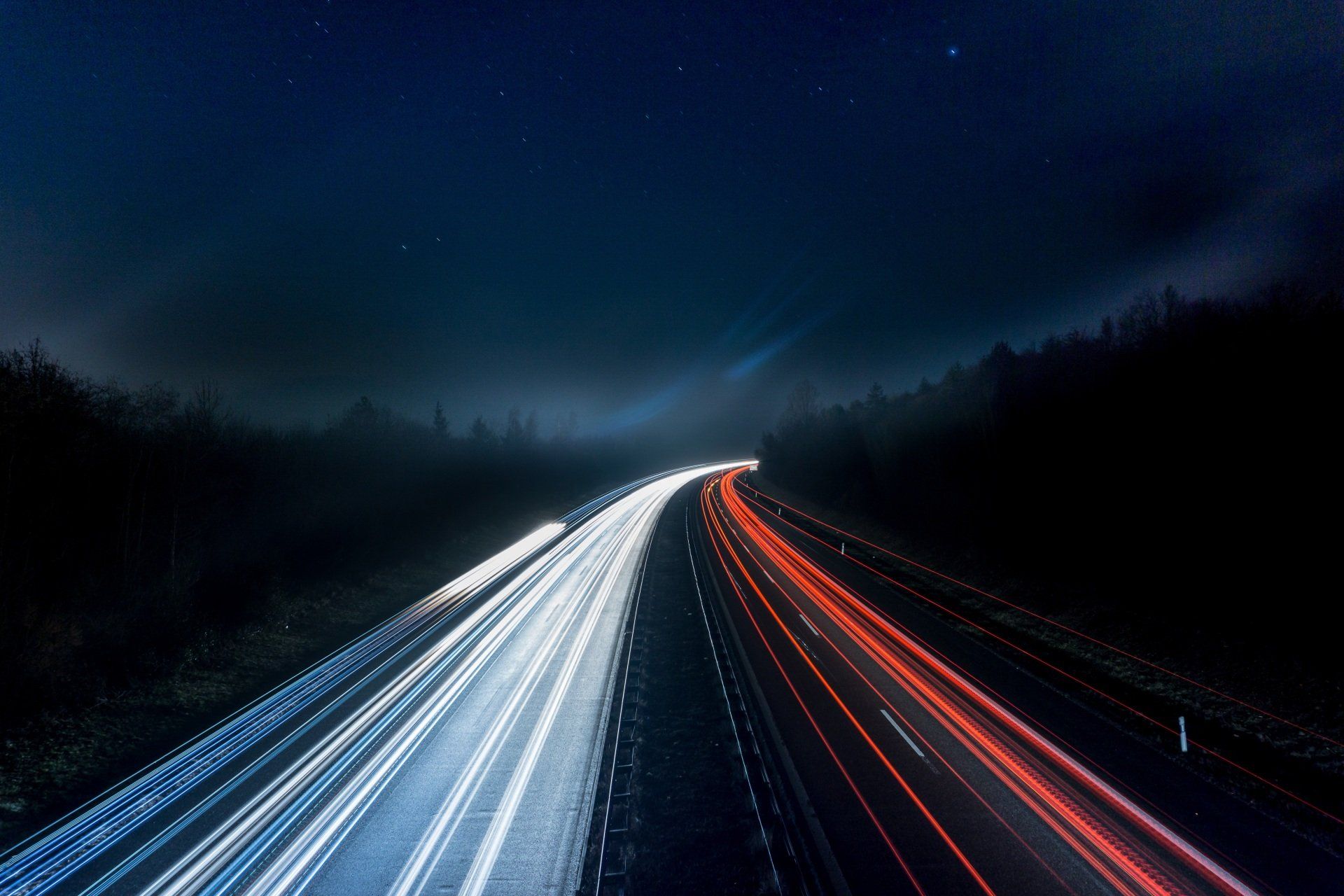
The UK Battery Industrialisation Centre (UKBIC) is on the hunt for a new Managing Director (MD), when its current Managing Director (MD), Jeff Pratt, steps down from the role later this year. The MD will leave UKBIC at the end of his five-year contract. Jeff joined UKBIC in June 2018 to oversee the development, delivery and launch of the £130 million facility as a new business, funded by government through the Faraday Battery Challenge. The pioneering facility is a key part of the Faraday Battery Challenge programme, which is being delivered by Innovate UK on behalf of UK Research and Innovation (UKRI), with the aim of building a high-tech, high-value, high-skill battery industry in the UK. UKBIC’s role is to support UK industry through the challenging scale-up and industrialisation of battery technologies into commercial production. UKBIC is the UK’s national manufacturing battery development facility, where businesses can develop their battery manufacturing processes at the scale they need to move to industrial production. Opened in July 2021, the unique facility bridges the gap between battery research and successful mass production, helping companies of any size to scale and commercialise their technologies. The facility was formally launched by the Prime Minister in July 2021. Since then, it has worked with a number of companies, providing capability and manufacturing facilities to support them in demonstrating their products at scale to de-risk investment in UK production. Richard Moon, UKBIC’s Chairman, said: “Since Jeff joined UKBIC as Managing Director, five years ago, he has overseen the successful delivery of the £130 million capital project, as well as establishment of the business from scratch and the growth of UKBIC from a small project team of around 10 people in 2018 to an operation of over 140 staff today. He has led the business through the unprecedented challenges presented by the Covid-19 pandemic over the last few years. Despite this, he has still managed to see UKBIC through to its launch in 2021 and the building of new business with the first customers since then. I am immensely grateful to Jeff for his dedication to UKBIC over the last five years and the vital expertise and experience he brought to the development of this unique facility.” Anyone wishing to apply for the role, should do so here .
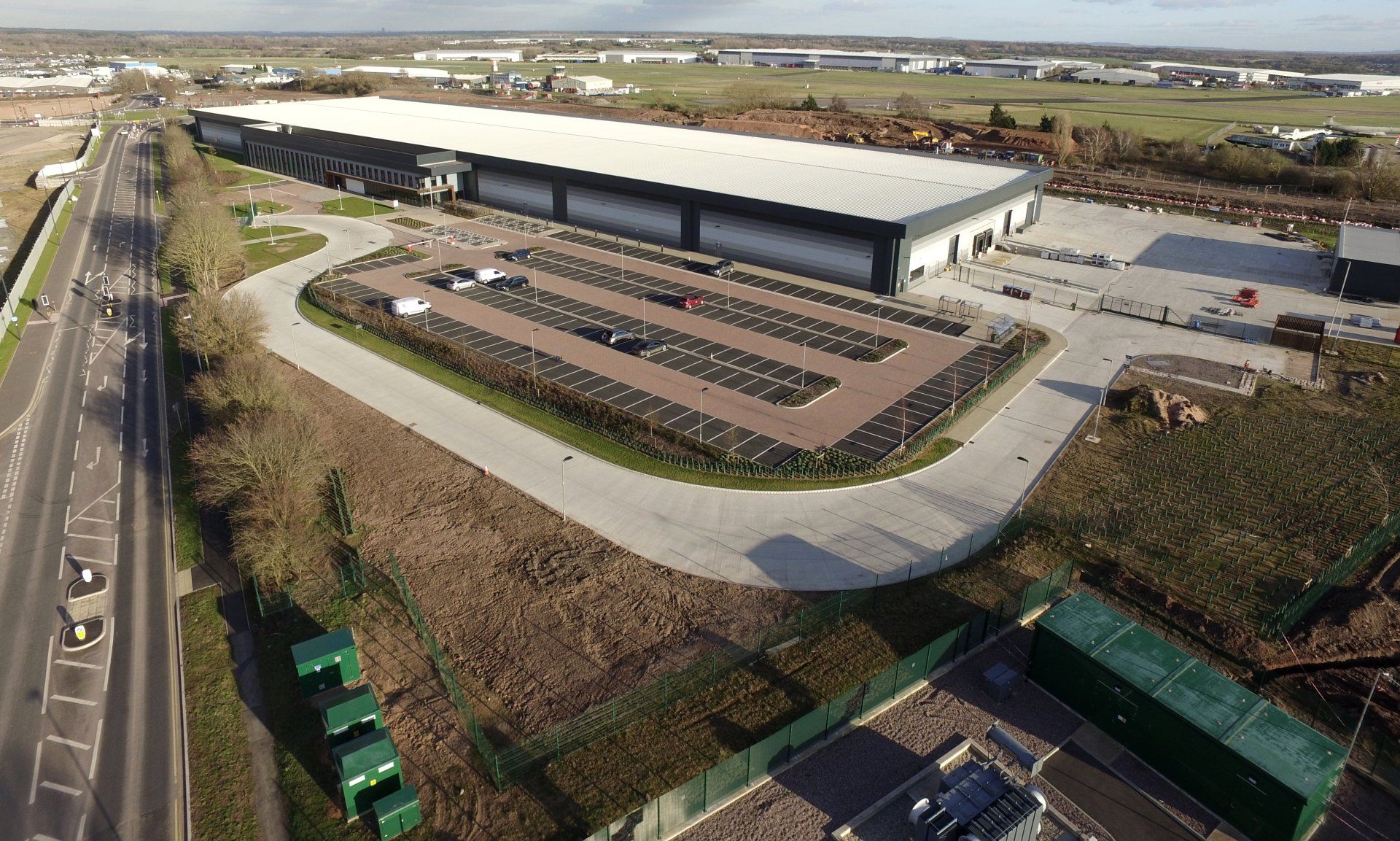
£1.5m up for grabs in competition to support SMEs working in the battery sector UK Research and Innovation has launched a new £1.5million competition to support UK small medium sized enterprises (SMEs) working in the battery sector. The competition provides SMEs with the opportunity to work with the UK Battery Industrialisation Centre (UKBIC), created to provide UK battery manufacturing scale-up and skills for the battery sector.
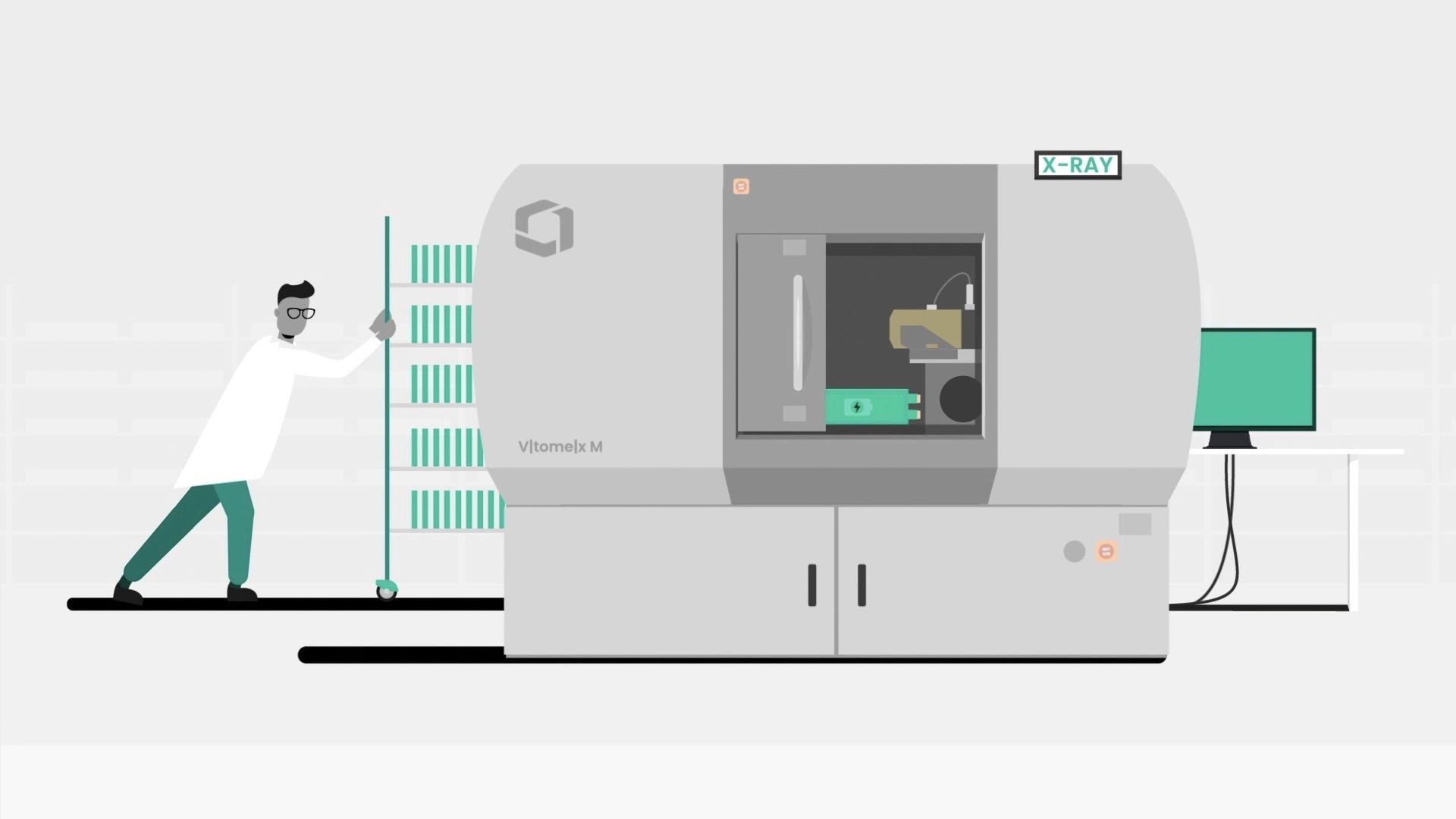
Waygate Technologies, a Baker Hughes business, and its partners, the UK Battery Industrialisation Centre (UKBIC) and PXL-ICE, are among the winners of the most recent round of the Faraday Battery Challenge funding competition led by UK Research and Innovation (UKRI), a public body sponsored by the British Department for Business, Energy and Industrial Strategy (BEIS). The consortium funding is for a feasibility study to look at ways of potentially increasing the yield and productivity of UK gigafactories with data based on advanced industrial computed tomography systems. If successful, this could eventually lead to the development of a digital twin* at UKBIC.
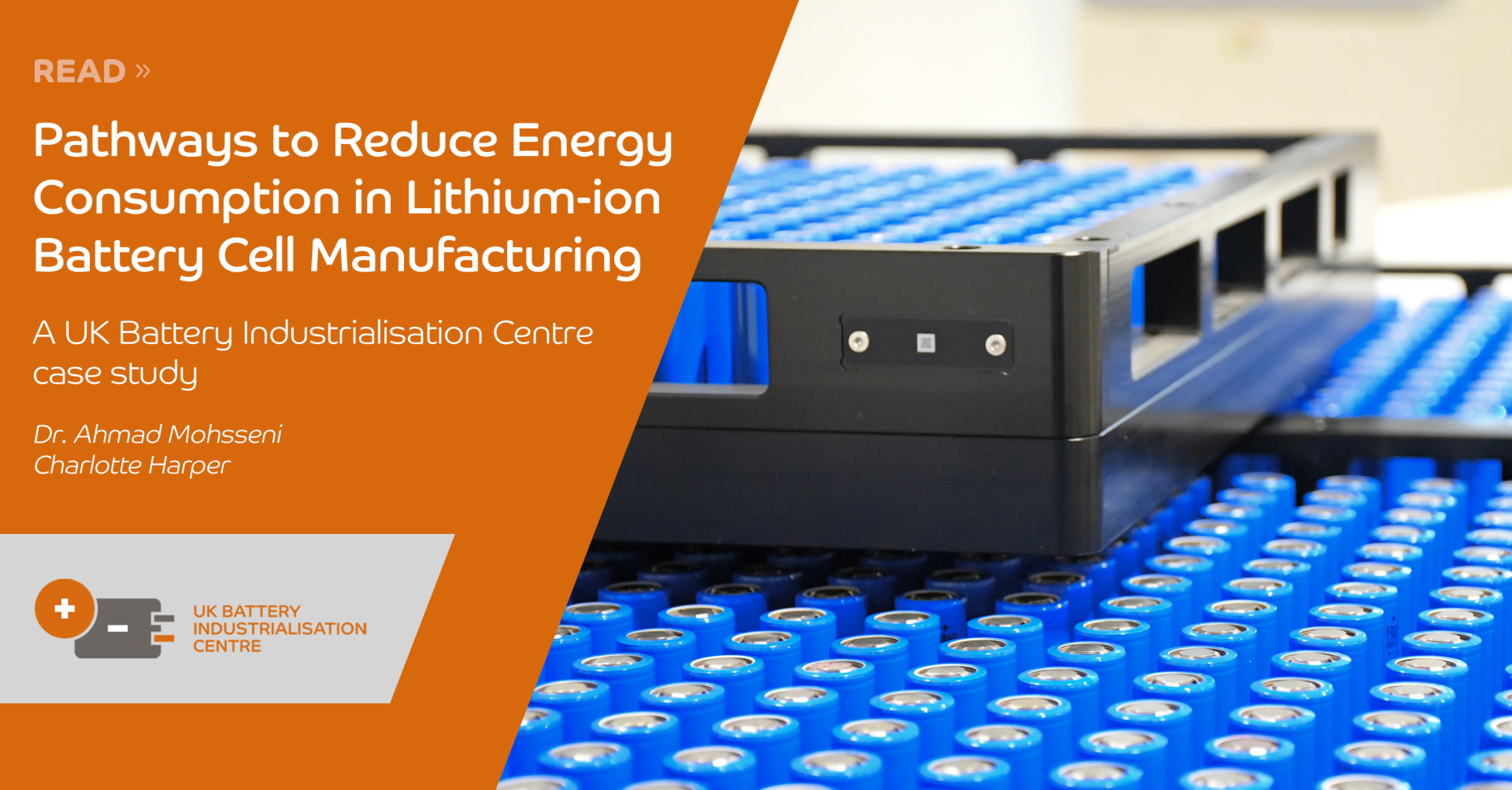
Demand for batteries is expected to grow significantly in response to decarbonisation targets and it is the battery manufacturing industry’s responsibility to reduce embedded carbon in their processes.
For the UK and Europe to compete globally in this sector, setting and achieving ambitious sustainability targets is crucial. For battery cell manufacturing (slurry mixing to formation/ageing), the largest contributor to carbon footprint is energy consumption.
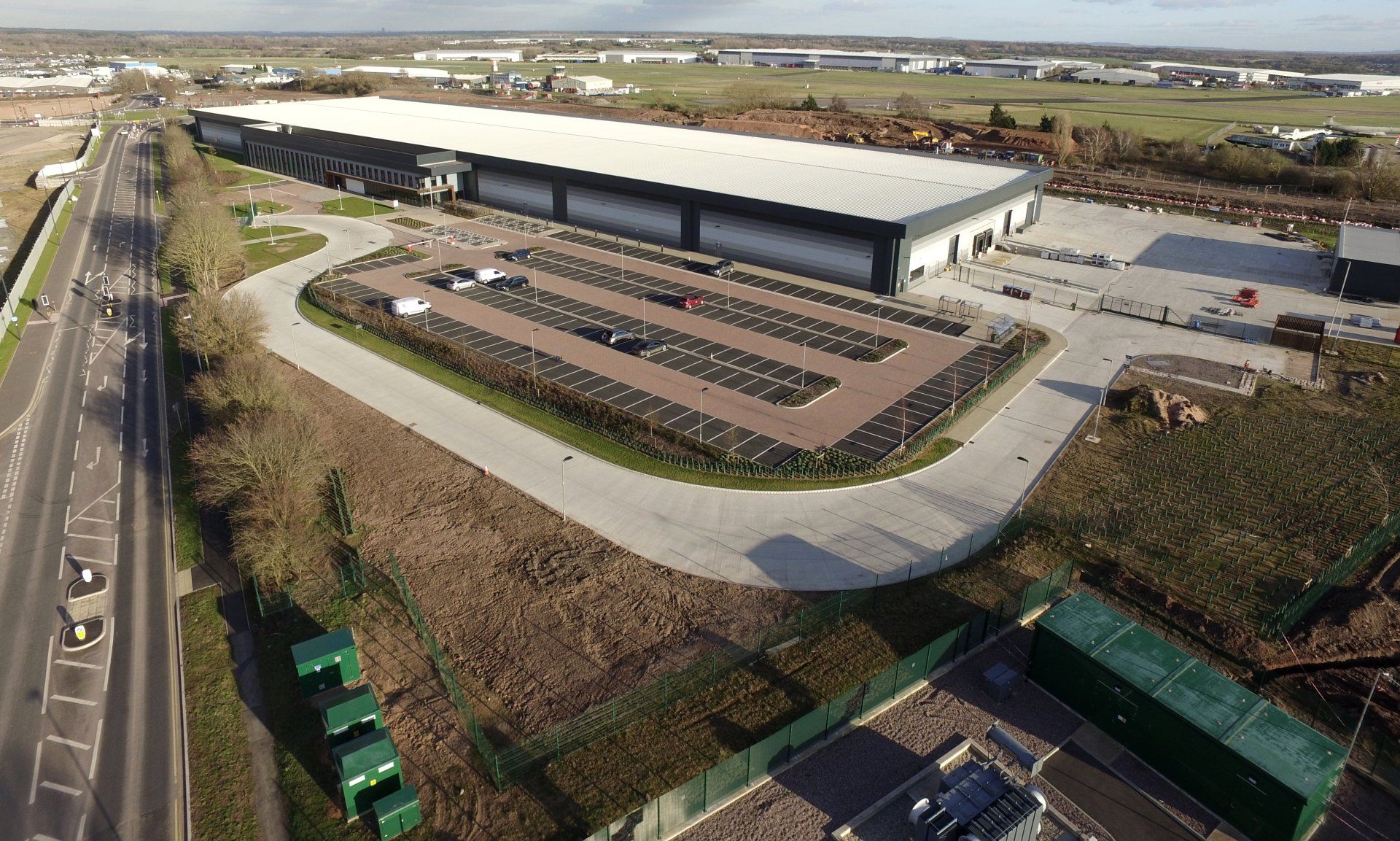
The UK Battery Industrialisation Centre (UKBIC) is a £130 million national battery manufacturing
scale-up facility which provides skills for the growing battery sector. The specialist manufacturing research facility celebrates its first anniversary today (Friday 15 July), marking 12 months since UKBIC was officially opened by the British Prime Minister, the Rt Hon Boris Johnson MP.
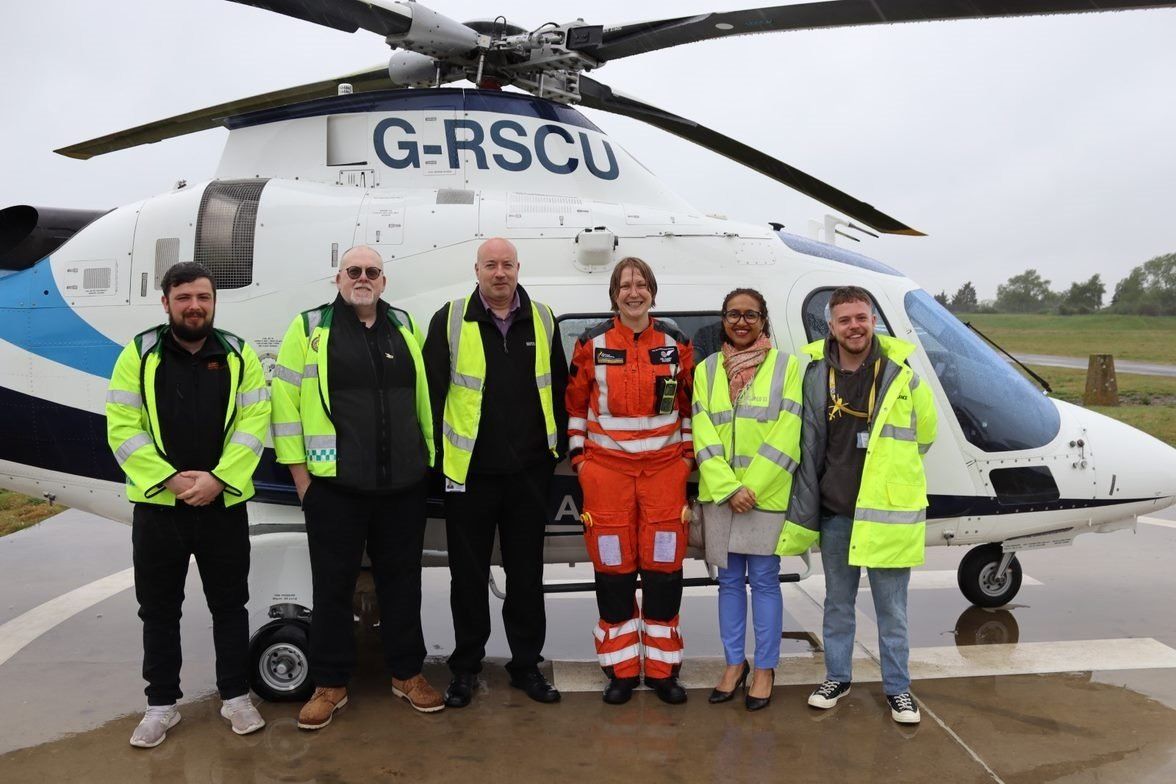
Good Samaritans from the UK Battery Industrialisation Centre in Baginton are aiming to raise £1,700 for the local air ambulance by climbing Snowdon. The party of 17 plan to walk to the summit using the popular Llanberis Path later this month (May 28) and raise the necessary funds to cover the cost of single flight for the helicopter.
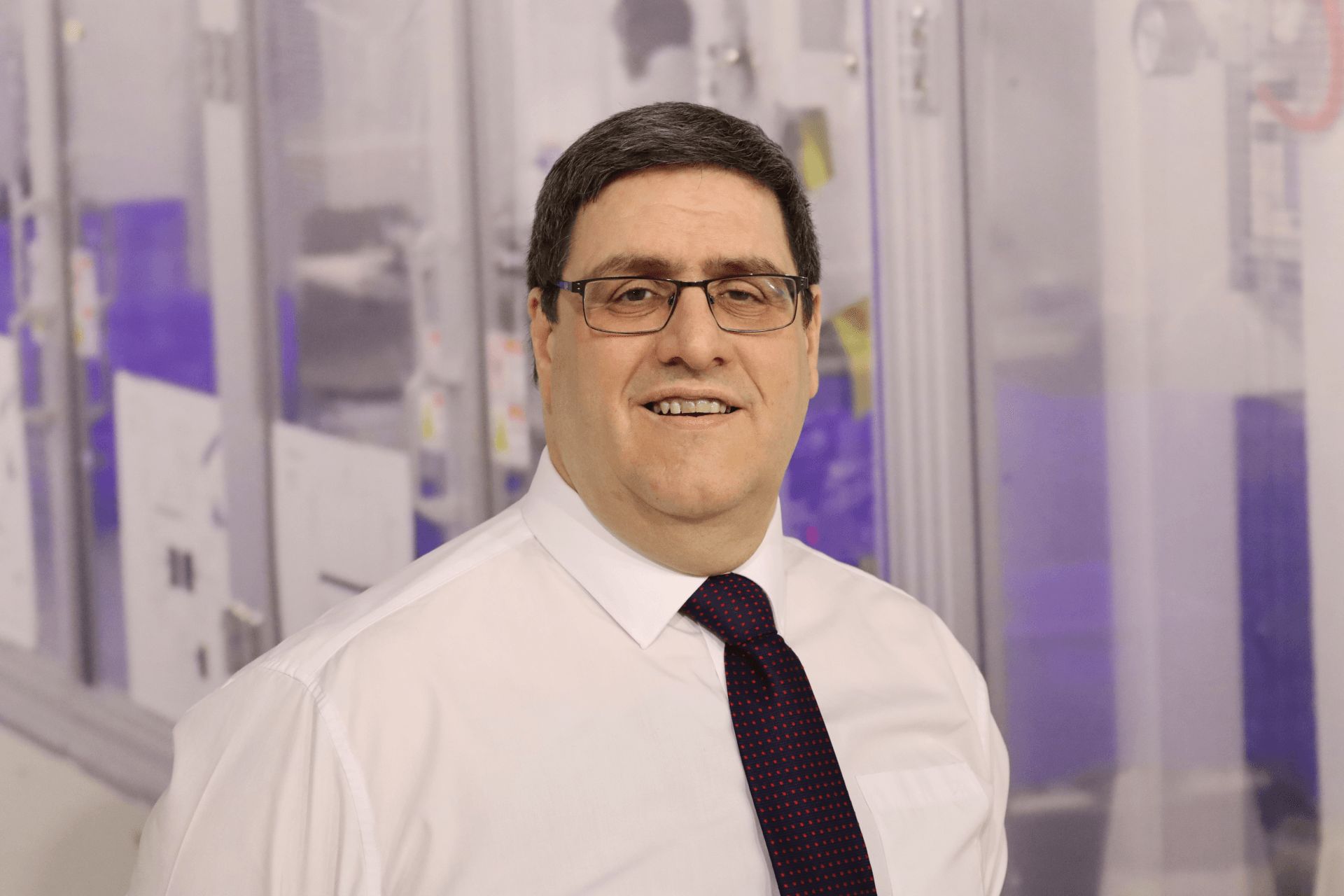
The UK Battery Industrialisation Centre (UKBIC) has appointed John Poli to the post of Manufacturing Operations Director. John is responsible for the facility’s manufacturing capability and is part of UKBIC’s Executive team, reporting to the Managing Director, Jeff Pratt. Before joining UKBIC, John ran his own engineering consultancy, specialising in manufacturing engineering. Prior to that he was Jaguar Land Rover’s Power Train Manufacturing Engineering Director, responsible for global engine, electric drive and battery manufacturing.
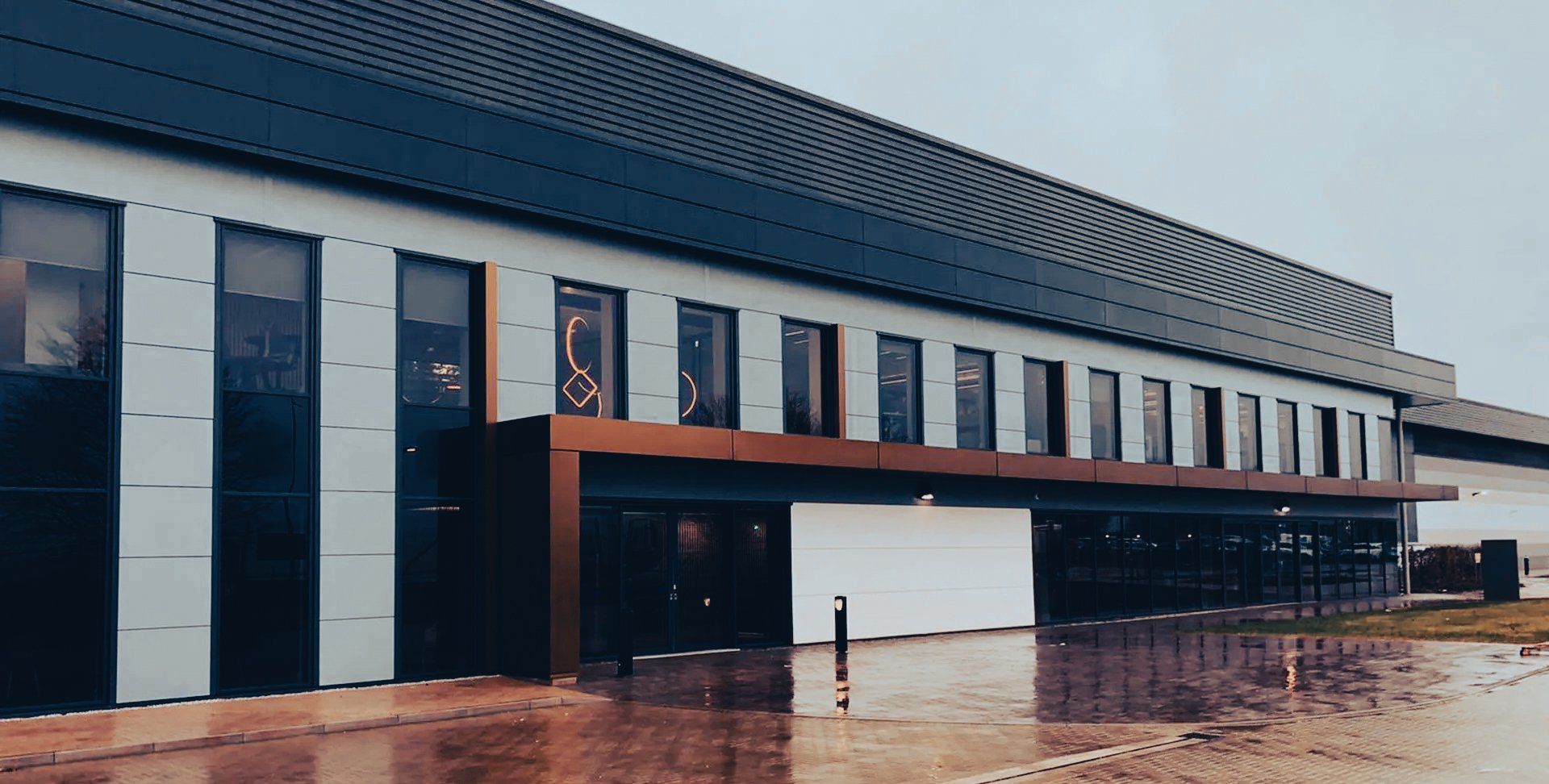
The UK Battery Industrialisation Centre (UKBIC) has achieved certification against an internationally recognised standard for its work in developing its Quality Management System (QMS). UKBIC, the national battery manufacturing development facility, has achieved certification against ISO 9001:2015 by BSI, the business improvement and standards company for the organisation’s QMS which supports the facility’s systems and processes.
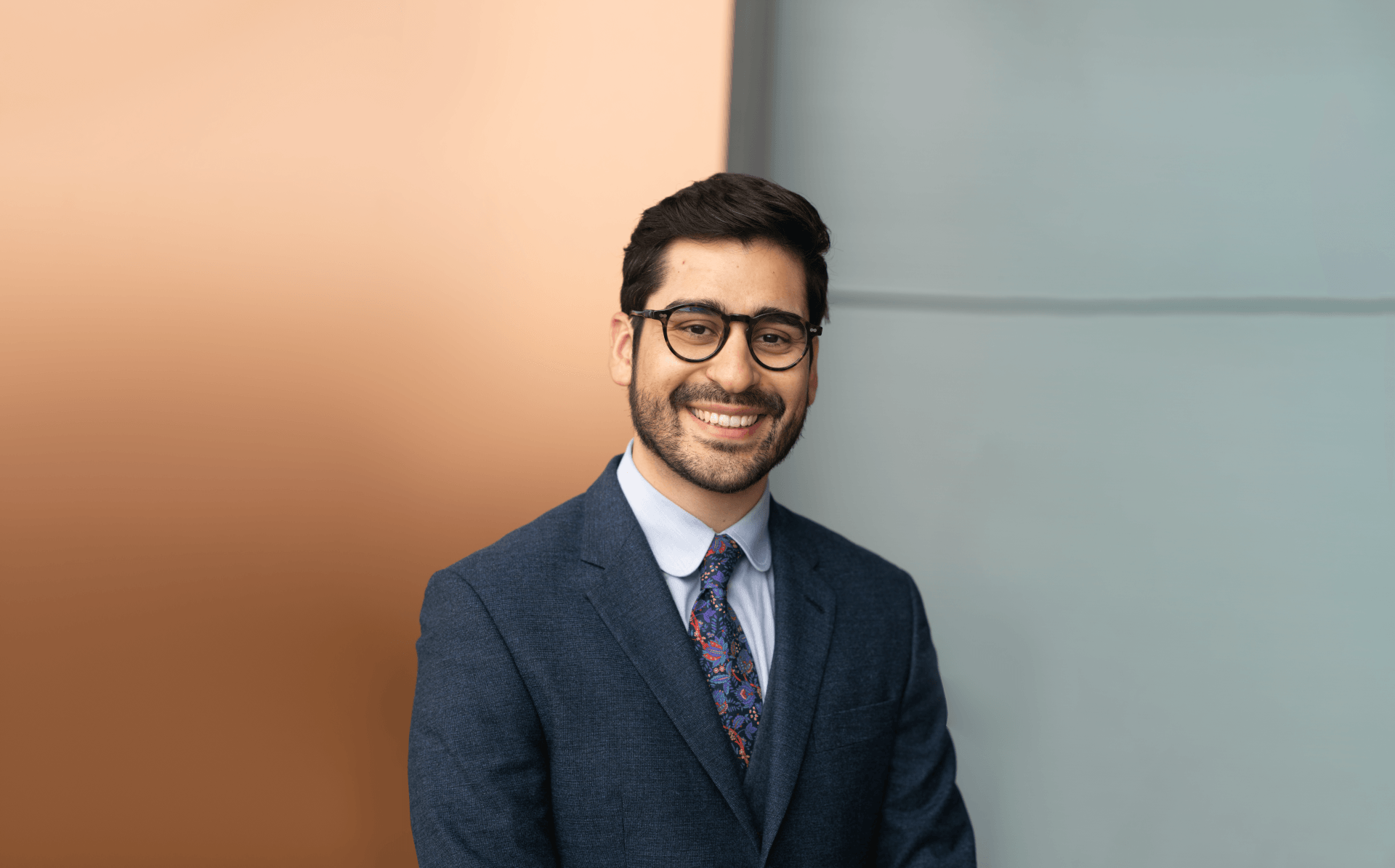
Dr Ahmad Mohsseni, Chief Technology Officer at UKBIC, has been made an Honorary Associate Professor at WMG. Dr Ahmad Mohsseni joined UKBIC in April 2019, where he sits on the executive committee – the team responsible for delivering and operating the Centre. Dr Mohsseni is responsible for Engineering and Quality specifically.
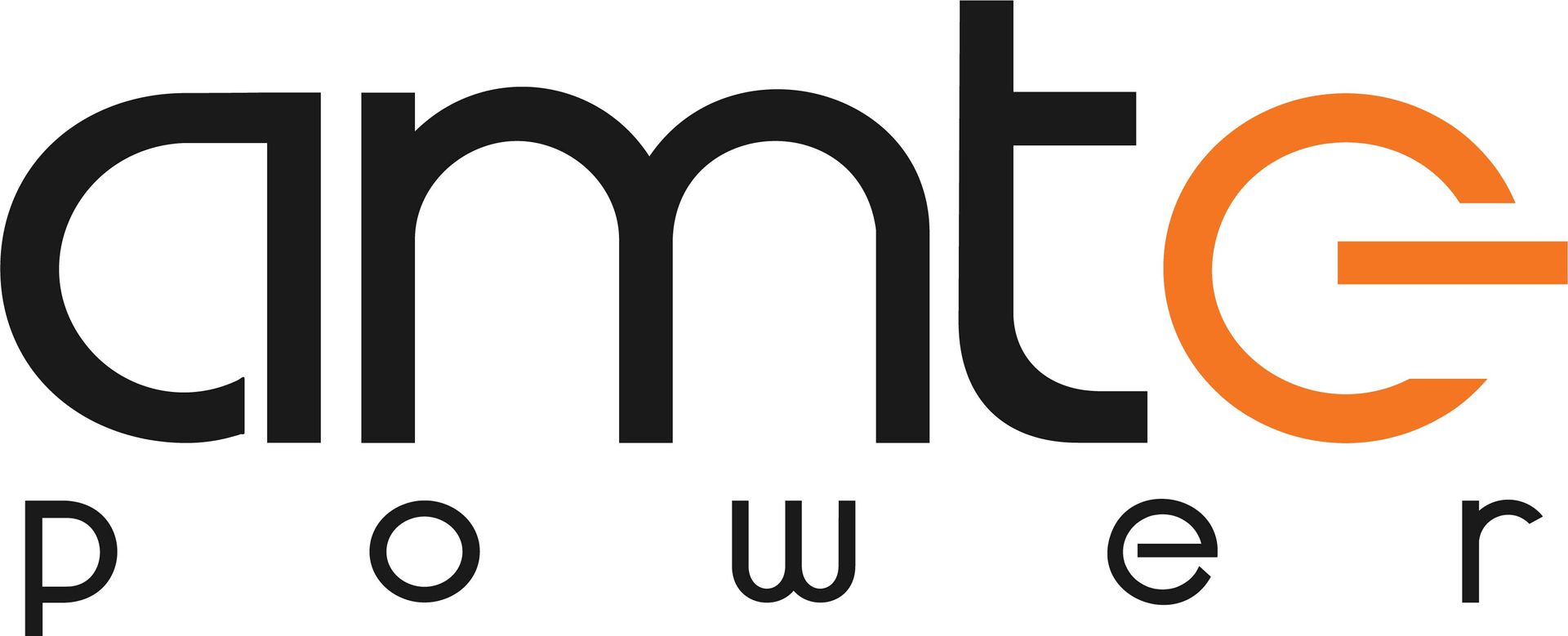
The Power Up project will combine Imperial College London’s research and UKBIC’s battery manufacturing capabilities, to bridge the gap from prototype to mass production. AMTE Power has secured a project from the Government’s Faraday Battery Challenge, worth £1 million, to develop a higher energy density variant of its Ultra High-Power (UHP) lithium-ion cell, with support from Imperial College London for battery modelling.
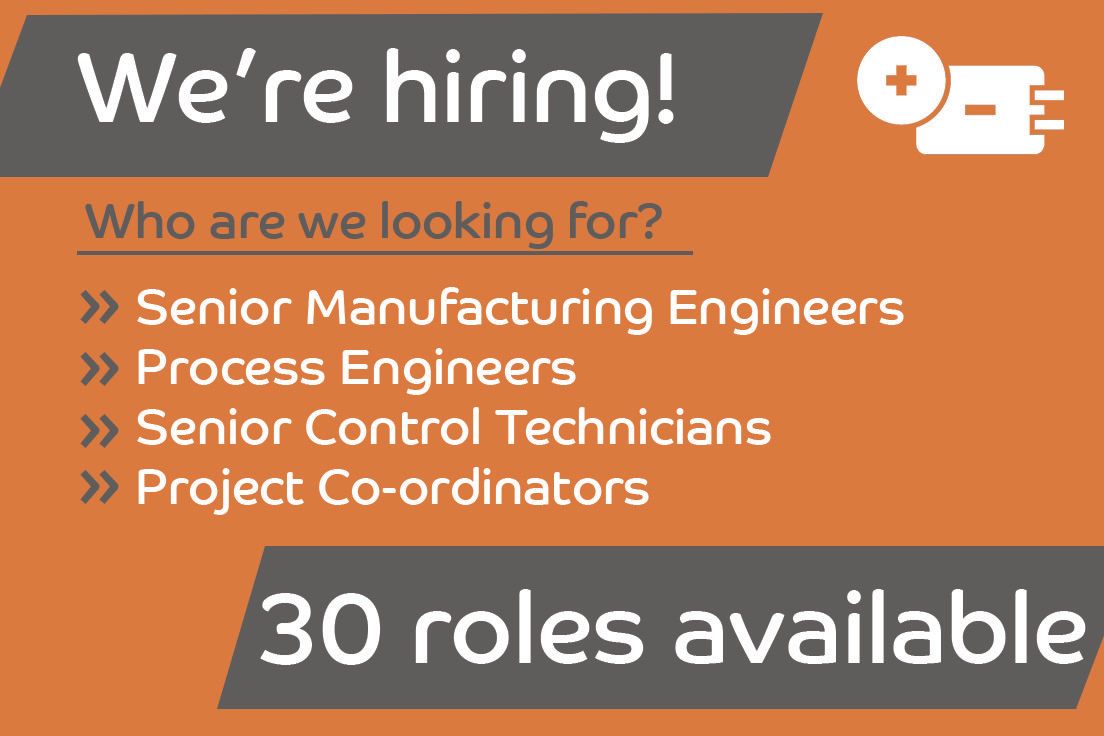
The UK Battery Industrialisation Centre (UKBIC), which was officially opened in July by the Rt Hon Boris Johnson MP, the Prime Minister, is set to add 30 new battery roles to support the first large customer projects it has secured. The new national battery manufacturing development facility in Coventry, which employs more than 80 engineers, technicians and back-office staff, needs to grow its workforce by 35 per cent so that it can fulfil its orders from the OEMs (original equipment manufacturers) and battery developers it is working with.
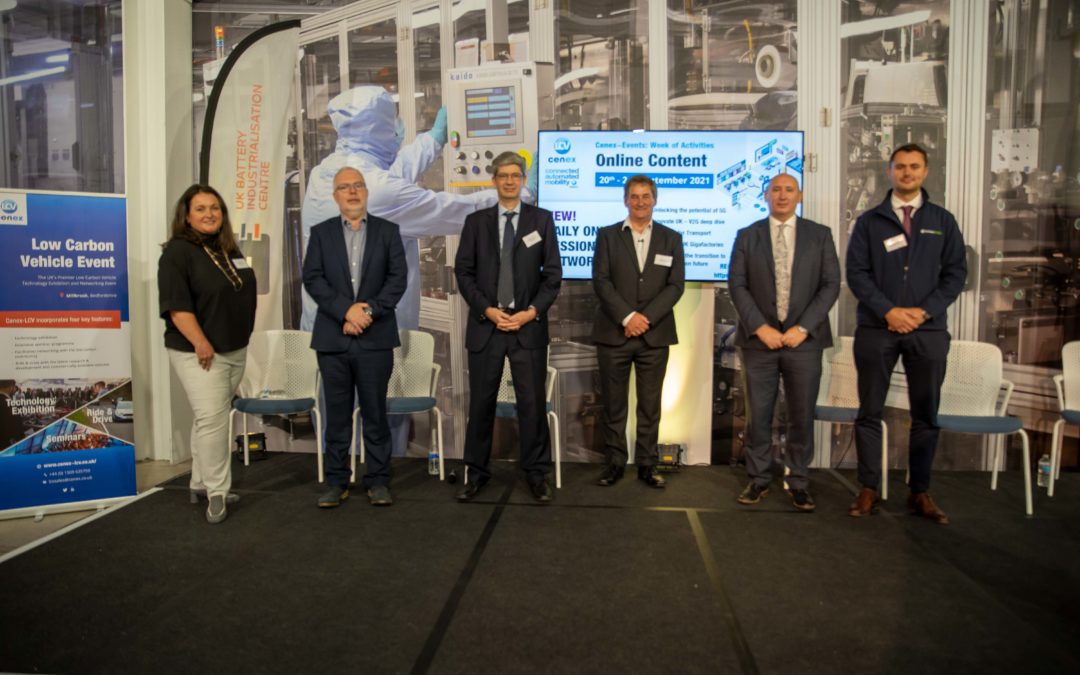
UKBIC has (today) hosted a seminar for Cenex’s 14th Low Carbon Vehicle event, on Developing UK Gigafactories. The seminar will be streamed online on Tuesday 21 September starting at 4pm and will then be available for a month. The seminar – the first time that LCV has held a physical session away from the main LCV conference – was recorded live in UKBIC’s main process hall. 
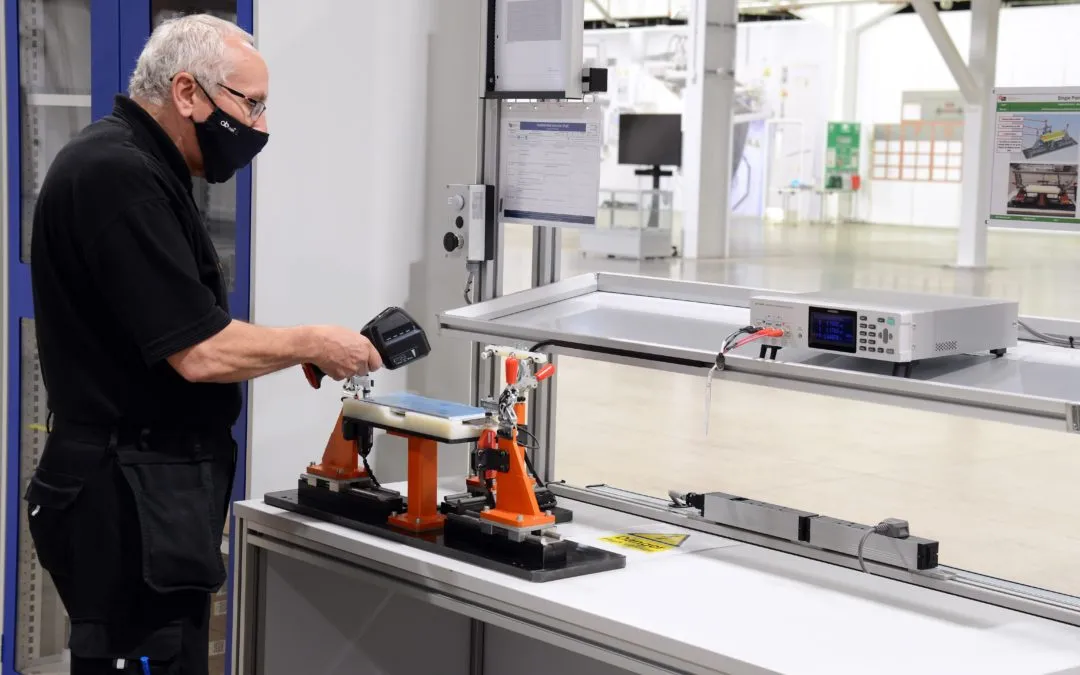
Until now, smaller manufacturing companies have missed out on the productivity benefits of digital technologies and data-driven solutions. Too many manufacturers don’t know where to start, and lack the skills required to deploy and use digital solutions. The costs are perceived to be high and the return on investment is unclear. Earlier this year, a consortium which included the UK Battery Industrialisation Centre (UKBIC) was awarded funding through the Government’s Manufacturing Made Smarter Challenge to tackle this problem by developing the Smart InforMation PLatform and Ecosystem for Manufacturing (SIMPLE). Project SIMPLE brings the benefits of digitalisation to manufacturers for whom the technology, skills, and business benefits are currently inaccessible. The project is delivering a platform that is fast to deploy, easy to use, cost-effective, and versatile. And it is being supported by an ecosystem that addresses skills and training requirements. 
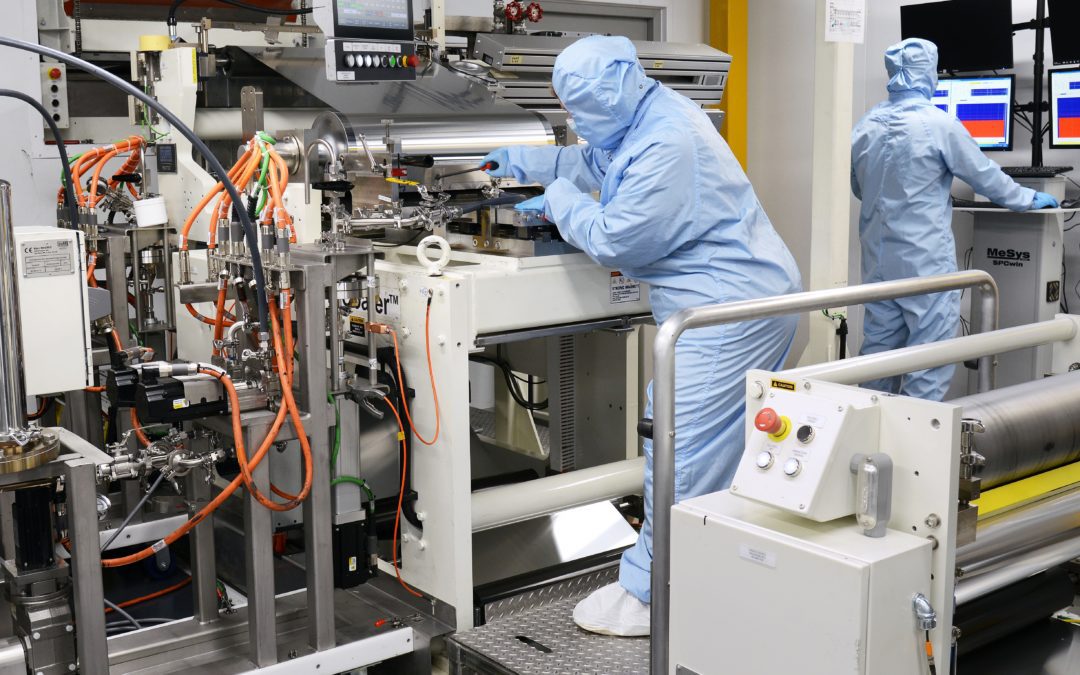
MOU signed between Johnson Matthey, Faraday Institution, Britishvolt, Oxford University, UK Battery Industrialisation Centre, Emerson & Renwick and University of Warwick. A consortium of seven UK-based organisations has signed a memorandum of understanding to combine ambitions to develop world-leading prototype solid-state battery technology, targeting automotive applications. Solid-state batteries offer significant potential advantages over conventional lithium-ion batteries and could be transformational in meeting the UK’s net zero commitments through the electrification of transport. The successful outcome of the collaboration would be to harness and industrialise UK academic capability to produce cells using highly scalable manufacturing techniques that leapfrog the cost-effectiveness and performance achieved elsewhere. 
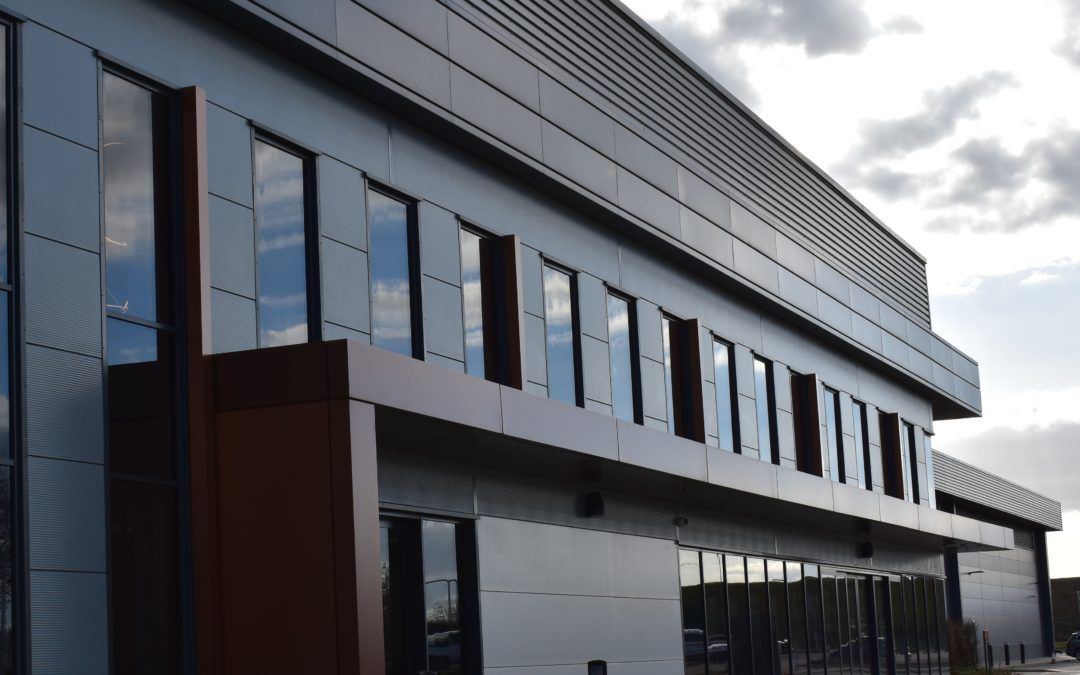
Innovate UK on behalf of UK Research and Innovation (UKRI) has announced a further investment of £10 million from the Faraday Battery Challenge to support collaborative R&D projects co-funded by industry and managed by UKRI. At least two of the 17 projects will use UKBIC, the pioneering battery manufacturing development facility UKBIC recently opened by the Prime Minister, to help deliver the projects.  UKBIC has been developed to support UK industry with development of battery technologies for future electrification. The facility is a key part of the Government’s Faraday Battery Challenge, created to fast track the commercialisation of cost-effective, high-performance, durable, safe, low-weight and recyclable batteries.
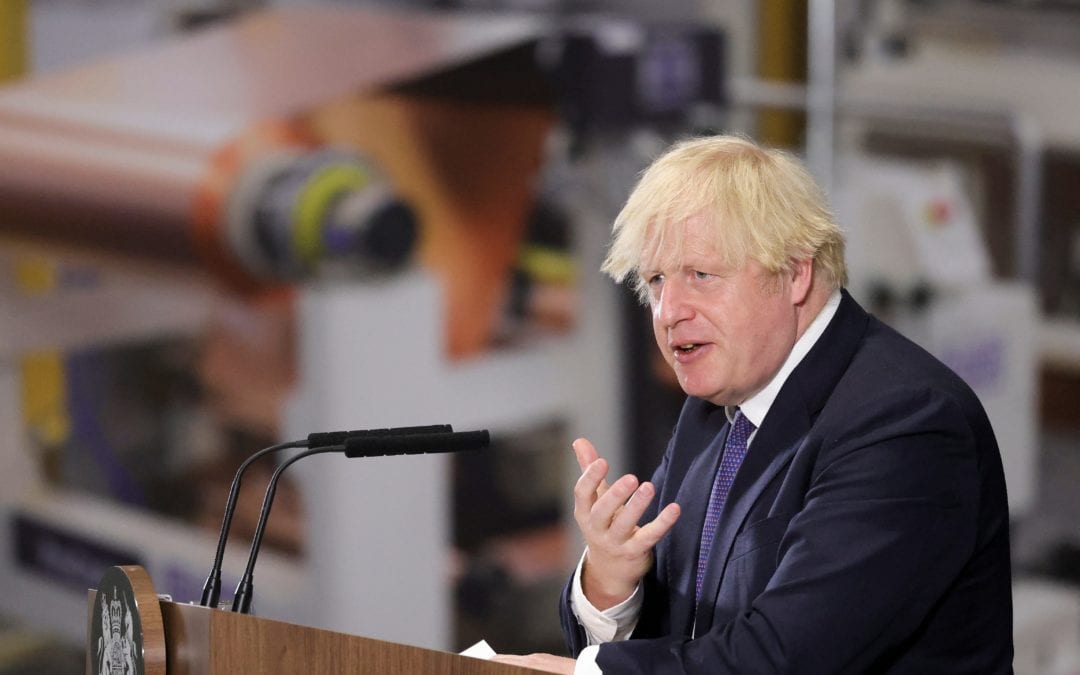
£130 million UK Battery Industrialisation Centre (UKBIC) opened by The Rt Hon Boris Johnson MP, Prime Minister. The £130 million UK Battery Industrialisation Centre (UKBIC) has today (15 July 2021) been officially opened by The Rt Hon Boris Johnson MP, Prime Minister. The Prime Minister formally opened the pioneering 18,500 square metre national battery manufacturing development facility during a visit to the UK City of Culture, Coventry, in the West Midlands.
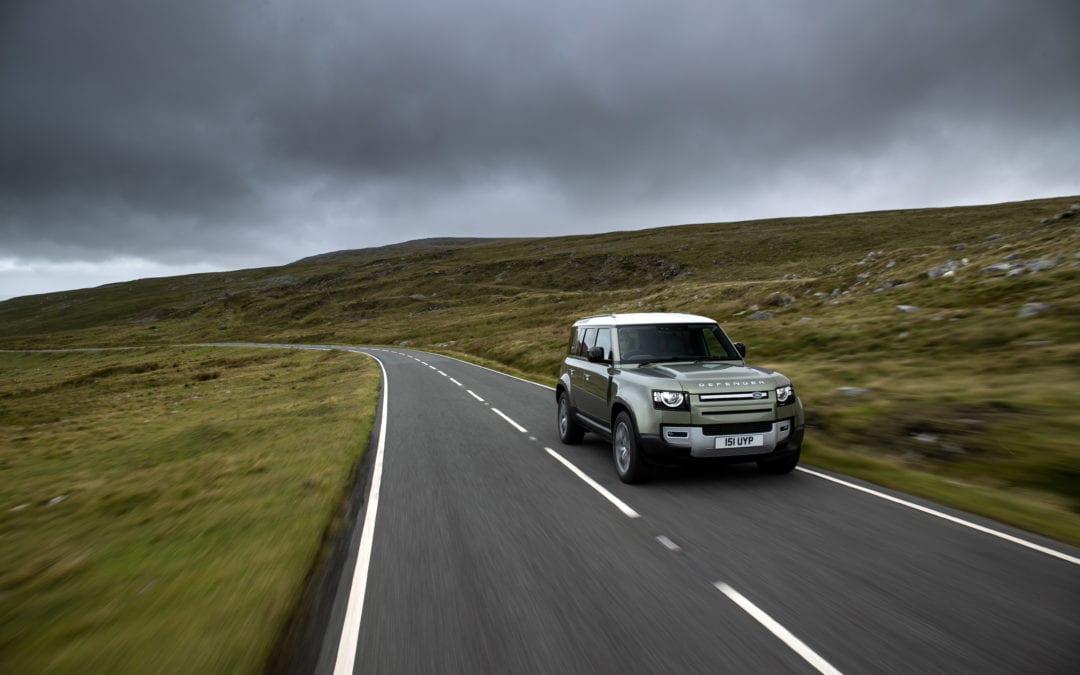
The FCEV concept is part of Jaguar Land Rover’s aim to achieve zero tailpipe emissions by 2036, and net zero carbon emissions across its supply chain, products and operations by 2039, in line with the Reimagine strategy announced last month. Jaguar Land Rover has announced hydrogen concept to be based on new Land Rover Defender Hydrogen fuel cell electric vehicle (FCEV) prototype to begin testing in 2021 Hydrogen FCEVs forecast to top 10 million by 2030 with 10,000 refuelling stations worldwide* Project part of company’s aim to achieve zero tailpipe emissions by 2036 and net zero carbon emissions across supply chain, products and operations by 2039
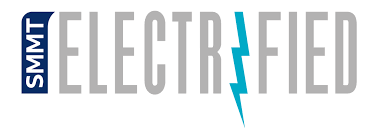
Ian Whiting, Commercial Director at the UK Battery Industrialisation Centre (UKBIC), is to take part in a panel discussion alongside speakers from ZF Group, Britishvolt, WMG and Advanced Propulsion Systems (APC) at the SMMT’s Electrified conference on Thursday March 25. Tata Consultancy Services, will be headline event partner for SMMT Electrified, alongside Auto Trader and BYD Europe. Chaired by Professor Dave Greenwood, Professor of Advanced Propulsion Systems, WMG, the other panellists will be Ian Constance, Chief Executive Officer, APC, Peter Lakie, Senior Vice President, ZF Group, and Isobel Sheldon OBE, Chief Strategy Officer, Britishvolt. The discussion will focus on building a robust and circular value chain to support the escalated production of electrified vehicles. Electrified will bring together industry leaders, government, media and key stakeholders from the energy, fleet and logistics sectors to discuss the latest developments in electrification; and will also explore what is required to create a sustainable transport system fit for today, and tomorrow. 
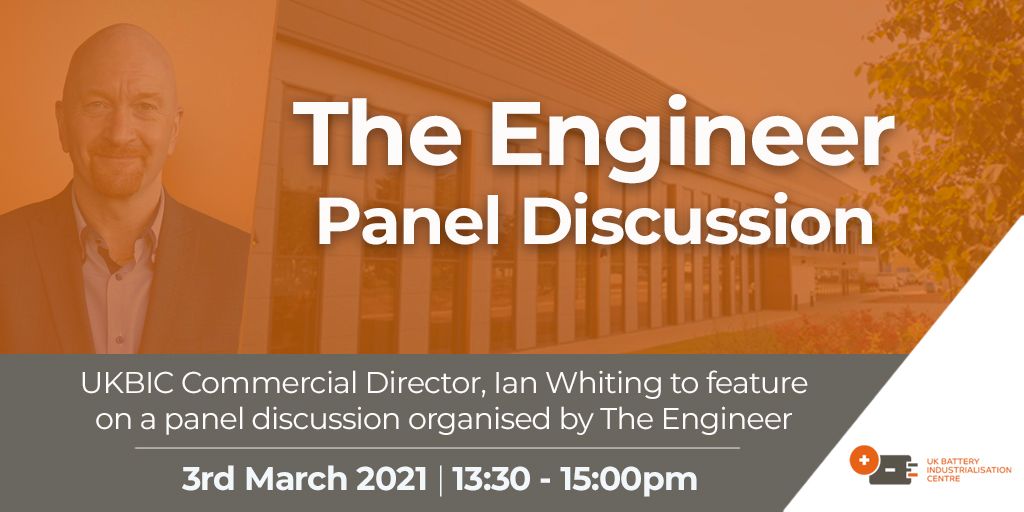
Ian Whiting, Commercial Director at the UK Battery Industrialisation Centre (UKBIC), is to participate in a panel discussion organised by The Engineer called ‘Industrialising Innovation – Accelerating the path to production.’ The event is being run in conjunction with the engineering consultancy Ricardo. The Engineer session, held on Wednesday March 3, will be chaired by The Engineer’s editor, Jon Excell. In addition to Ian, the other expert speakers will be Martin Starkey, Managing Director, Ricardo Performance Products; Graham Cooley, CEO, ITM Power; and Anthony Thompson – CSO, ISANSYS.
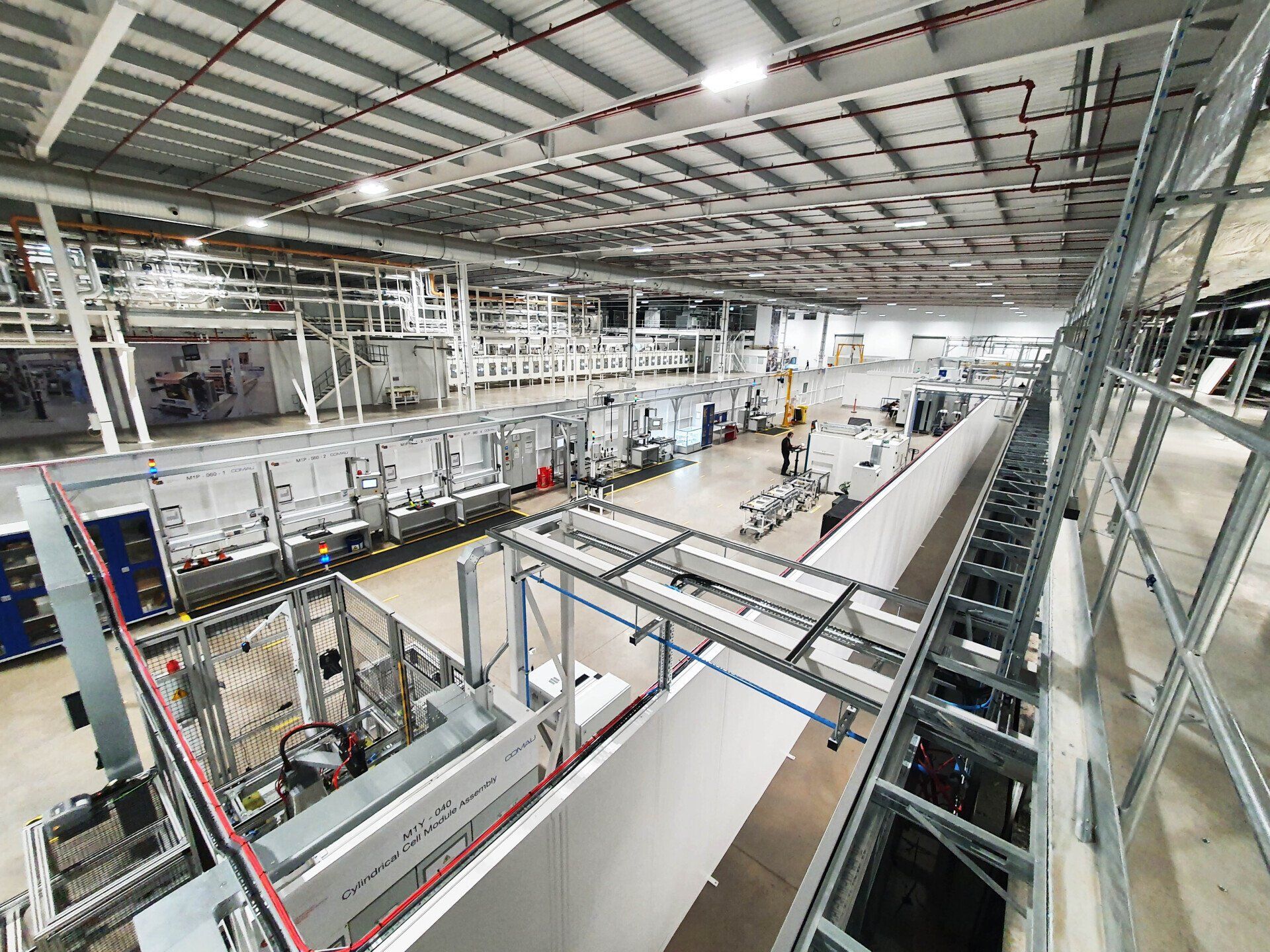
The £130 million UK Battery Industrialisation Centre (UKBIC) has moved a step closer to opening with the confirmation that the facility’s Module and Pack suite of specialist battery manufacturing equipment is now operational. The Module and Pack assembly line is the first of UKBIC’s innovative battery manufacturing equipment – sourced and supplied from leading manufacturers across the globe – to have been installed and commissioned at the publicly funded ‘open access’ 18,500 square metre battery development facility in Coventry. UKBIC’s highly flexible Module and Pack assembly line enables customers to test and produce low volumes of Cylindrical and Pouch cell battery technology. In addition, it has the capacity to produce 50 modules and 2.5 packs over every 8-hour shift.  The line has manual and automatic workstations; and has cylindrical cell ‘pick and place’ capability, for cell voltage testing and impedance, as well as the ability to place cells into a module in either combination of cell orientation.
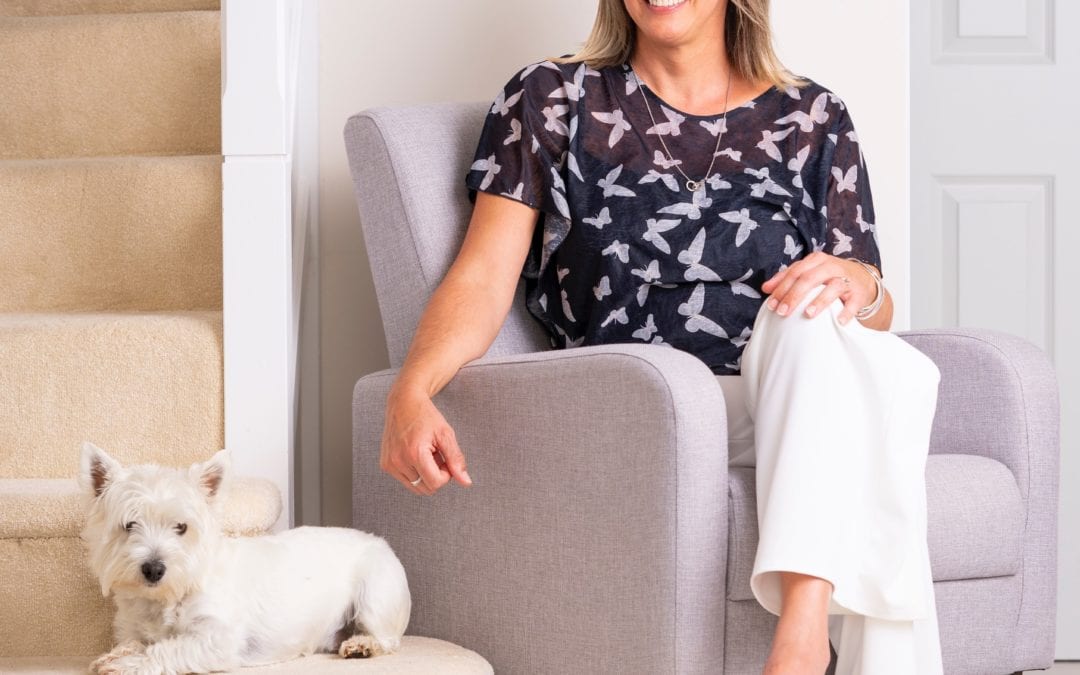
Isobel Sheldon awarded the OBE Jeff Pratt, UKBIC’s Managing Director, said : “We’re delighted that Isobel Sheldon has been awarded the Order of the British Empire (OBE) in Her Majesty the Queen’s New Year Honours list for her services to motor vehicle battery technology. The award recognises her work in the field of lithium-ion batteries and a career which has included working as Business Development Director for UKBIC, a battery production development facility to enable the scale-up of UK battery manufacturing. UKBIC is a key part of the Faraday Battery Challenge (FBC), a Government programme to fast track the development of cost-effective, high-performance, durable, safe, low-weight and recyclable batteries. 
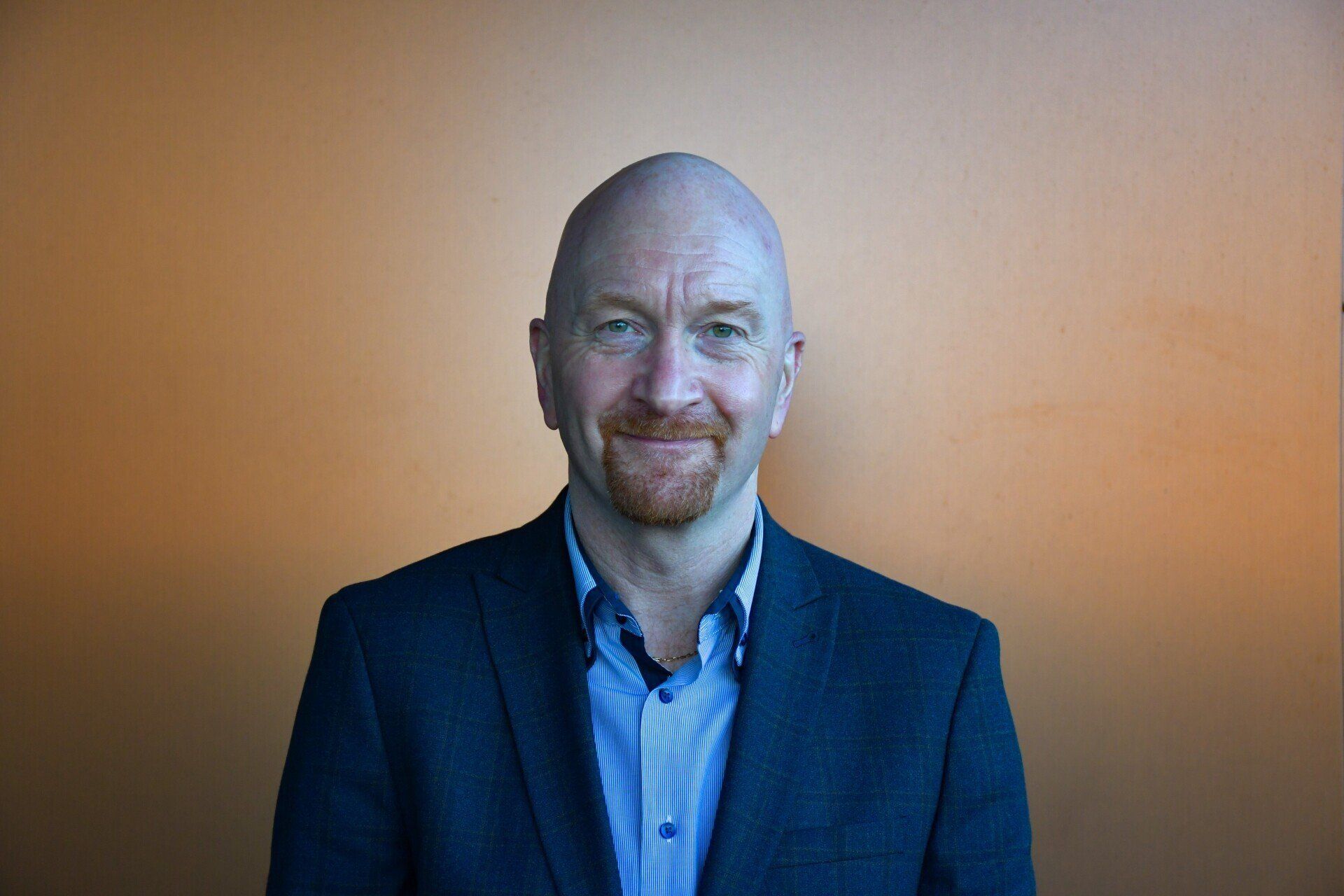
The UK Battery Industrialisation Centre (UKBIC), a soon to be completed battery production development facility near Coventry, has appointed Ian Whiting to the post of Commercial Director. Whiting, who has significant experience in business, the automotive, commercial and defence sectors, has previously worked for brands including AMTE Power, Ricardo and QinetiQ. His most recent role was as a freelance battery technology consultant.
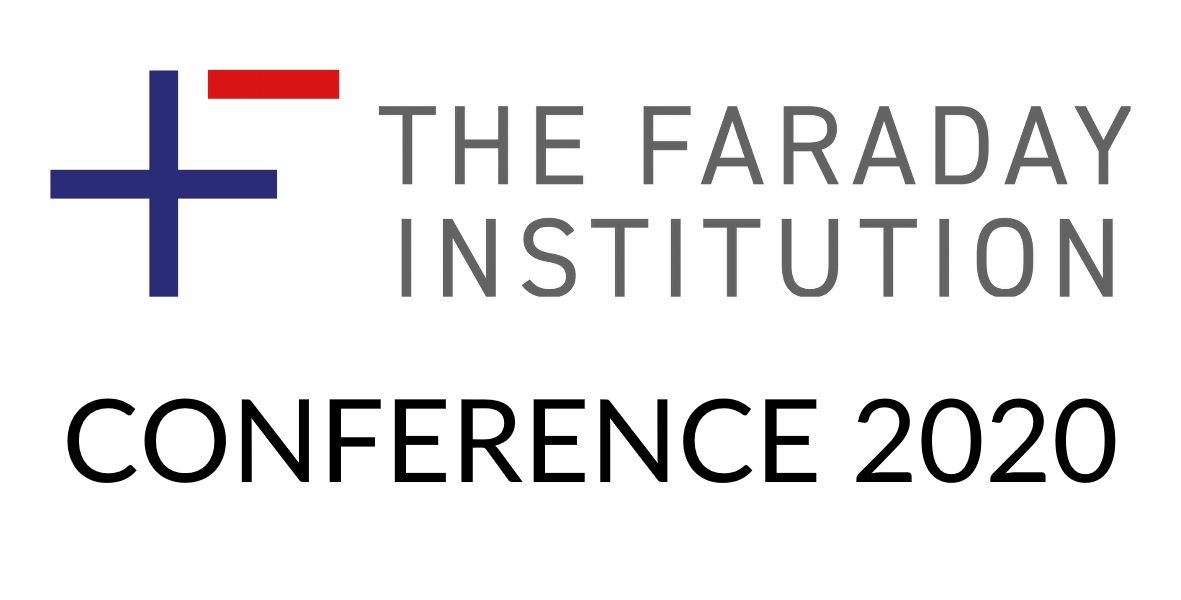
The £130 million UK Battery Industrialisation Centre (UKBIC), a unique battery production development facility which is due to be operational soon, is taking part in this week’s Faraday Institution conference. Dr Ahmad Mohsseni, UKBIC’s Chief Technology Officer, is part of a panel session on Thursday (26 November, 11am to 12.30pm) called Scale-Up of materials and processes.
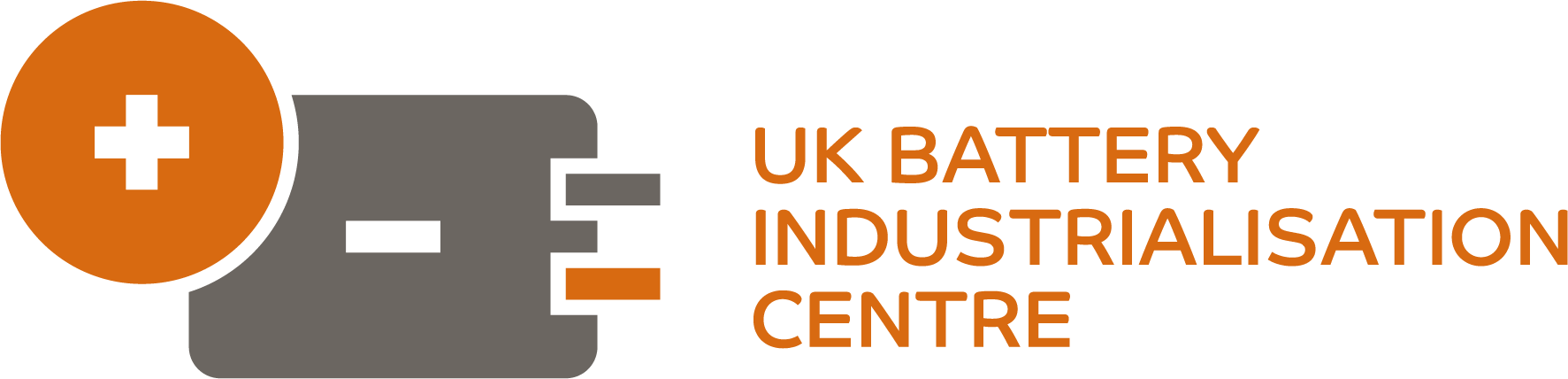
The £130 million UK Battery Industrialisation Centre (UKBIC) has updated the look and feel of its brand identity and refreshed its website. UKBIC is a pioneering concept in the race to develop battery technology for the transition to a greener future. The unique facility provides the missing link between battery technology, which has proved promising at laboratory or prototype scale, and successful mass production.
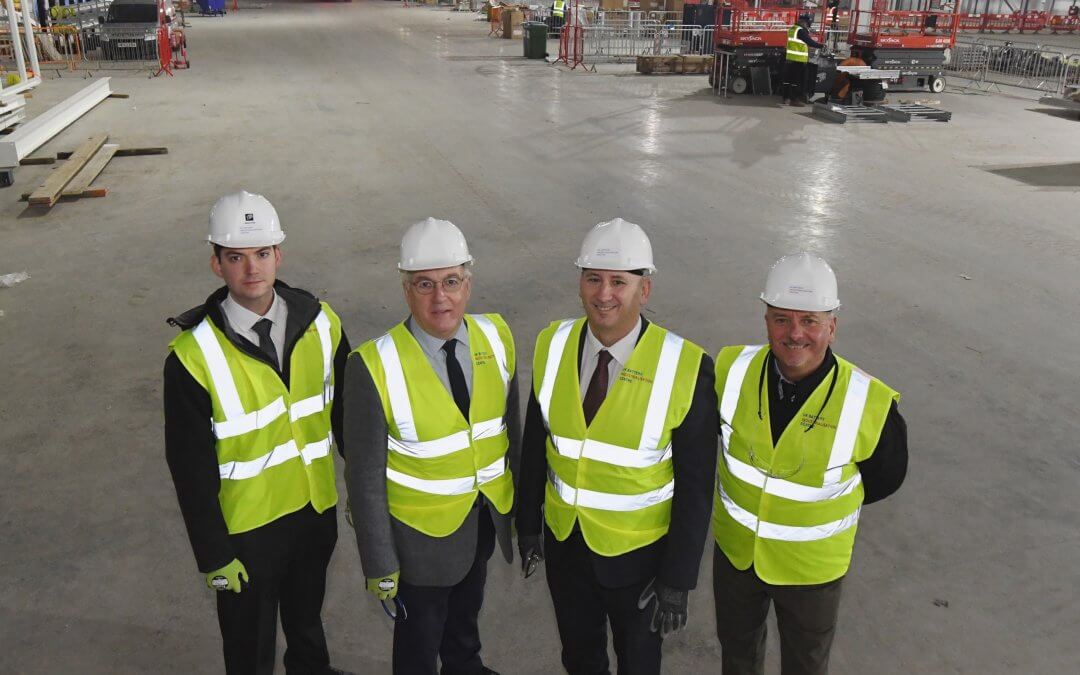
The practical completion of the new 18,000 sqm building has been achieved and phase two is now underway to add the production equipment, services and the internal finish which will be needed at the home of the UK’s new centre to help companies develop and scale-up production of the latest UK battery technology.
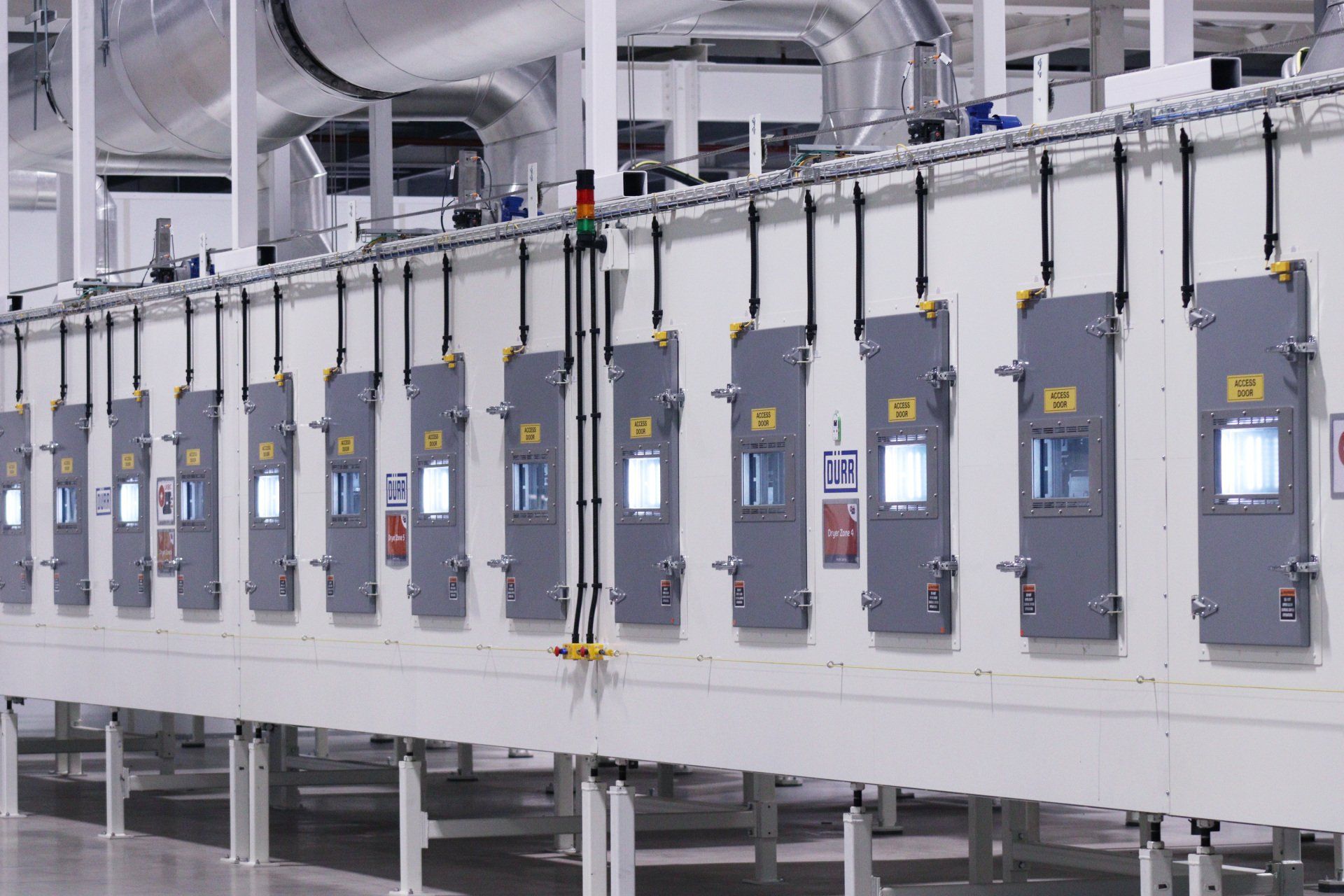
The first of more than £60 million of equipment has been delivered to the new £129 million UK Battery Industrialisation Centre (UKBIC) near Coventry which will open later this year. The practical completion of the new 18,000 sqm building has been achieved and phase two is now underway to add the production equipment, services and the internal finish which will be needed at the home of the UK’s new centre to help companies develop and scale-up production of the latest UK battery technology.
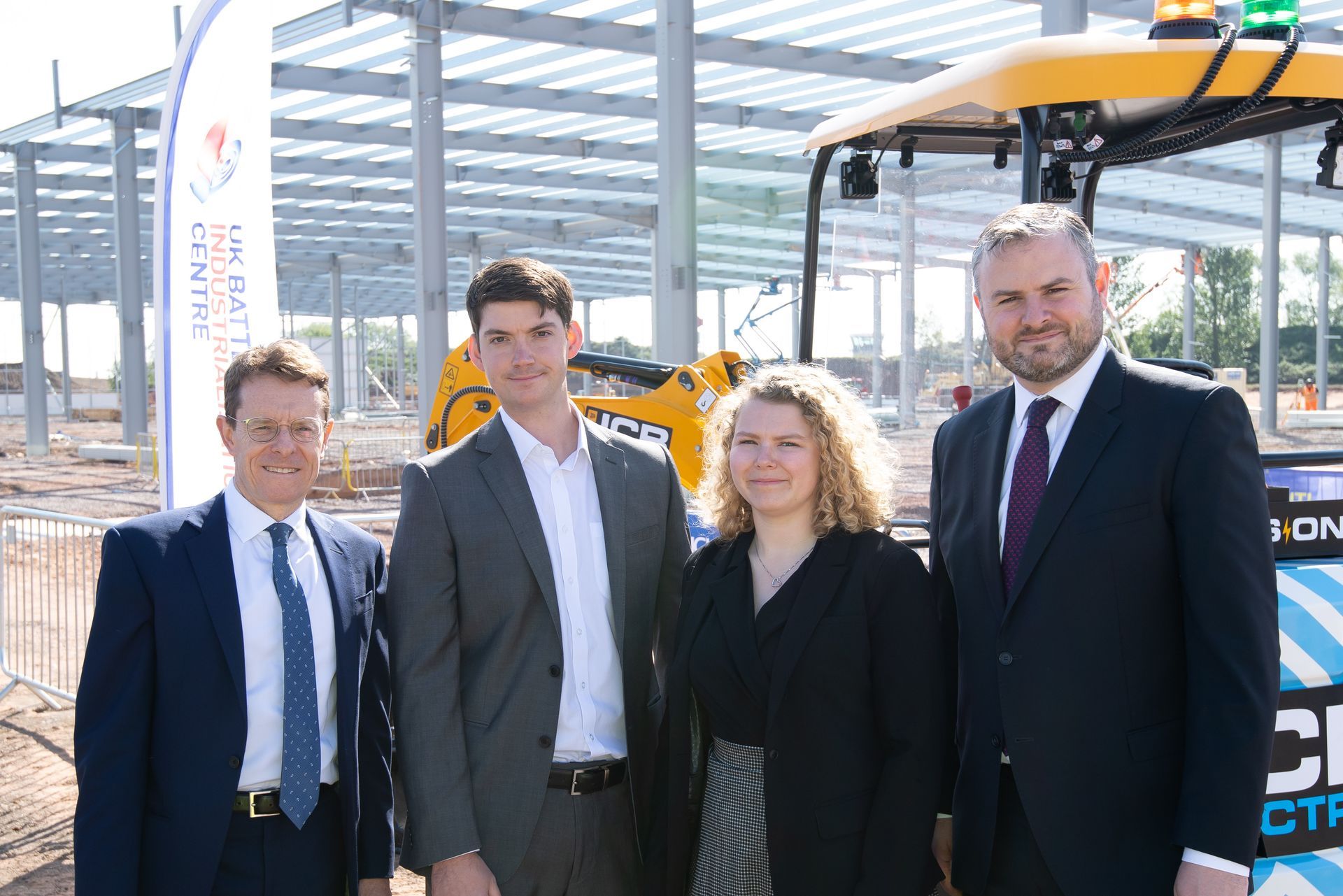
A £126m battery facility to keep the West Midlands at the forefront of the automotive industry has been supercharged by a £18m grant from the West Midlands Combined Authority (WMCA). The UK Battery Industrialisation Centre (UKBIC) in Coventry will be key in growing industrial battery manufacturing capability in the UK. The WMCA Board, chaired by Mayor Andy Street, has approved a repayable grant of £18m to help ensure UKBIC has the latest technology to attract top-tier automotive manufacturers and research and development companies.
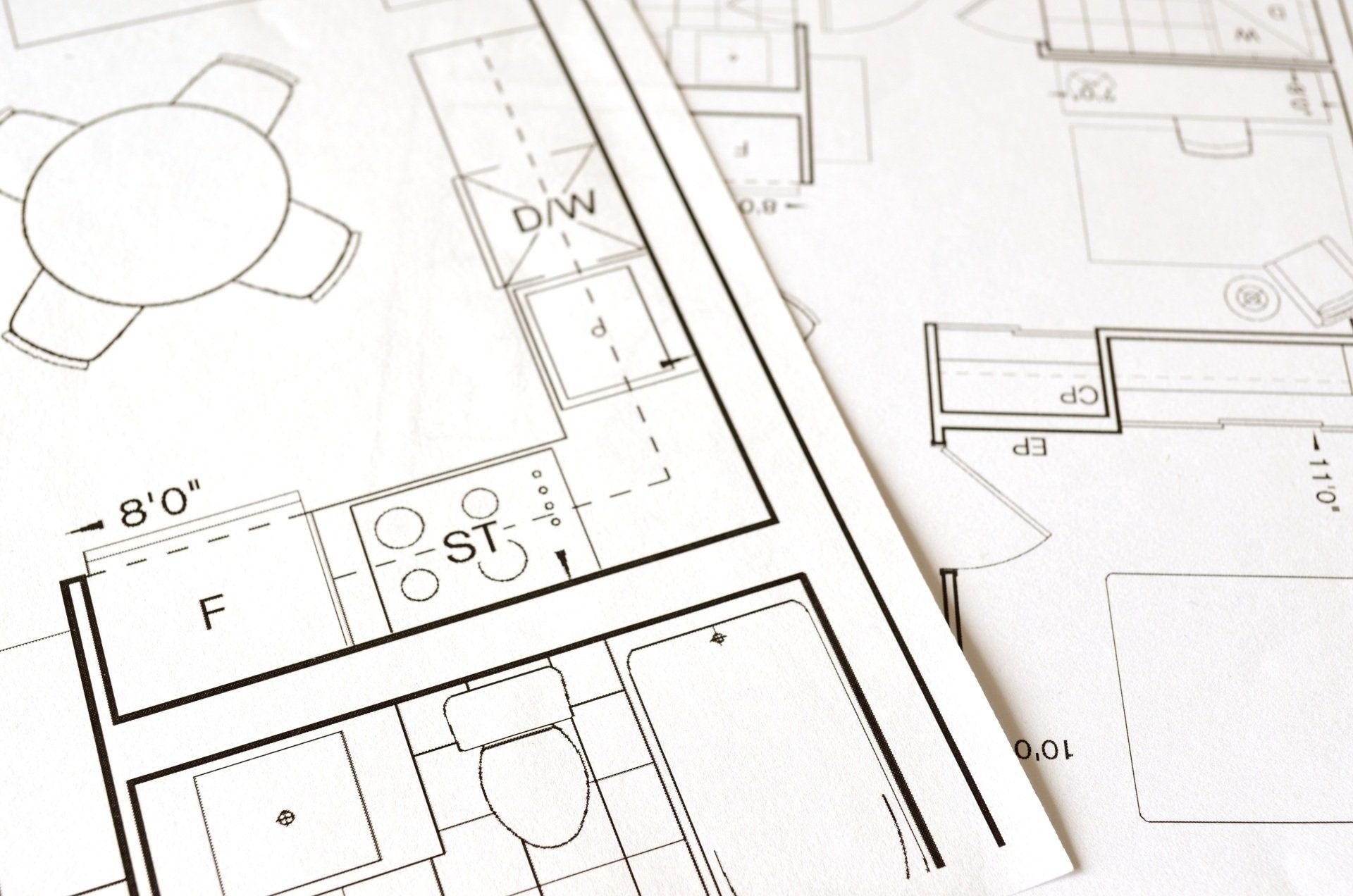
Planning consent has been granted by Warwick District Council to create the UK Battery Industrialisation Centre (UKBIC). Developers The Coventry & Warwickshire Development Partnership have been successful in their application to create a 193,750 sq. ft research and development facility near the A45/Festival Roundabout and A46/Tollbar Roundabout and at the junction of the A444 with the A4114/Whitley Roundabout in Coventry.
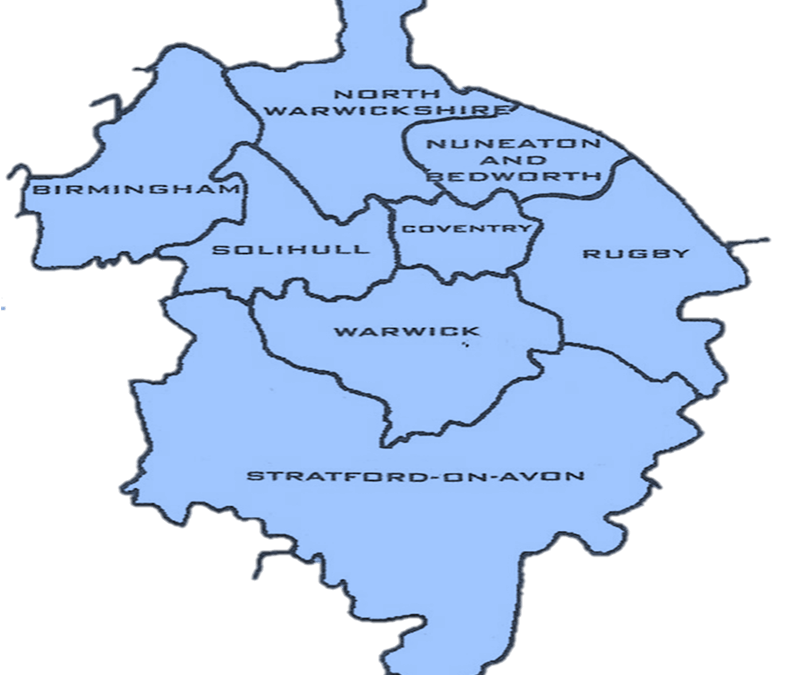
Developers The Coventry & Warwickshire Development Partnership have applied for planning consent to create a 193,750 sq ft research and development facility on land adjoining Rowley Road to the south of the A45. The new centre is a result of the region winning a national competition, with the successful joint bidding consortium consisting of Coventry City Council, Coventry and Warwickshire Local Enterprise Partnership and WMG, at the University of Warwick. The competition was led by the Advanced Propulsion Centre (APC) and supported by Innovate UK, to establish a new UK battery development centre.
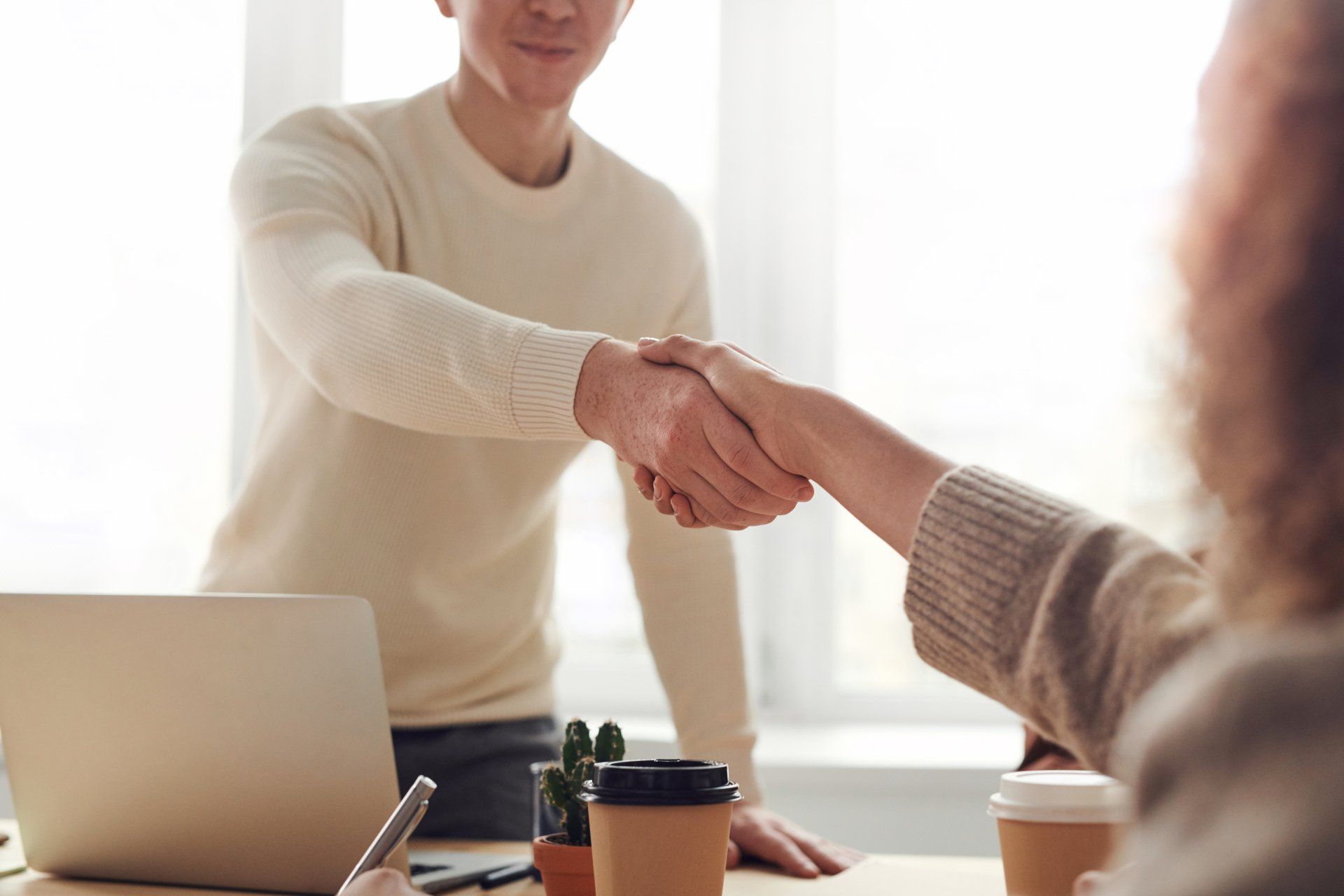
Recruitment is underway for a wide range of positions at the new £80 million UK Battery Industrialisation Centre (UKBIC). The innovative facility will be located in Coventry and Warwickshire as part of the Government’s Faraday Battery Challenge – a £246 million commitment over the next four years on battery development.
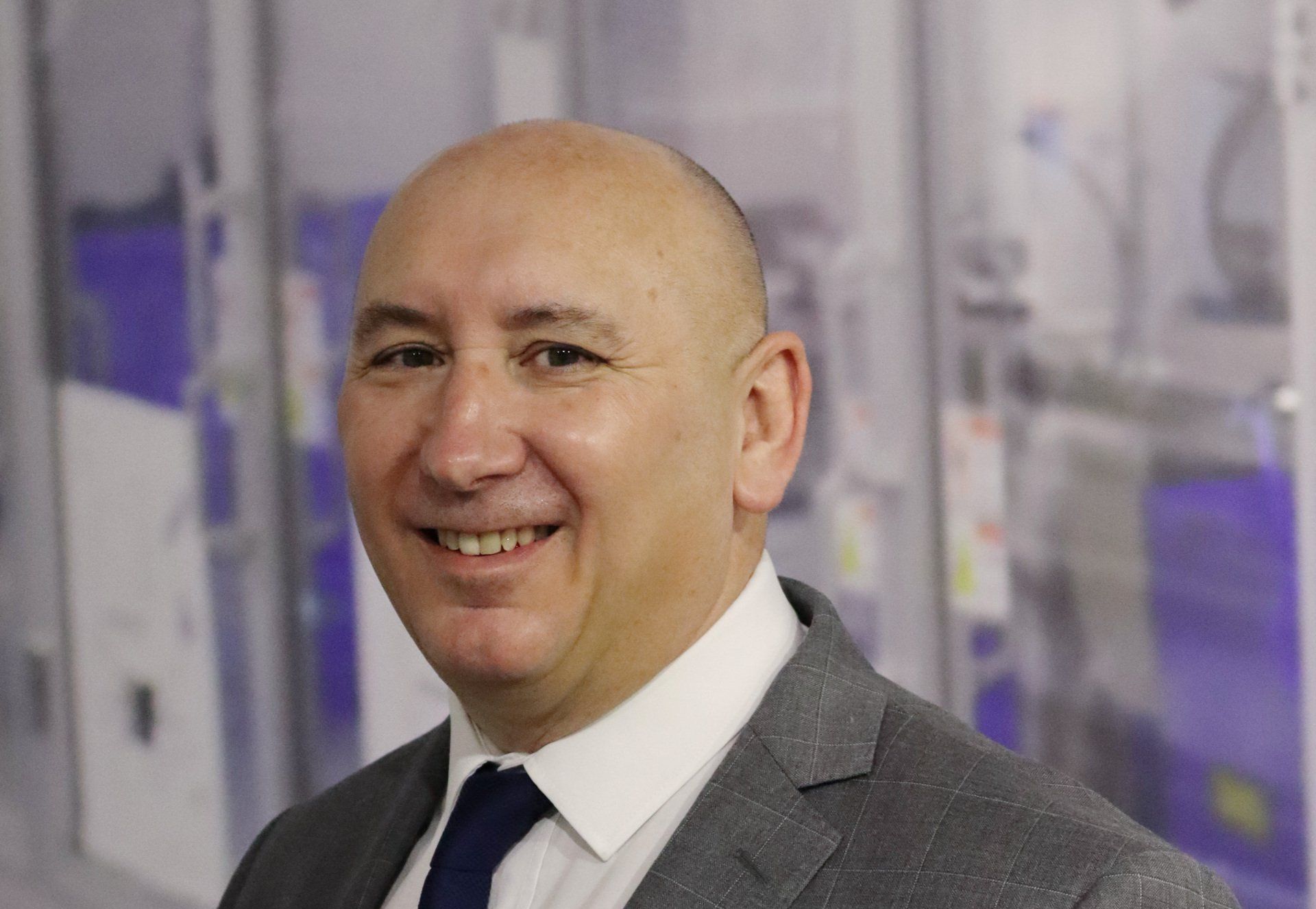
Jeff Pratt has been appointed Managing Director of the £80 million UK Battery Industrialisation Centre which is part of the Government’s Faraday Battery Challenge – a £246 million commitment over the next four years on battery development for the automotive sector. A national competition, which was led by the Advanced Propulsion Centre (APC) and supported by Innovate UK, to establish a new UK facility was won through a joint bid by WMG, at the University of Warwick, Coventry and Warwickshire Local Enterprise Partnership and Coventry City Council.