NG Bailey appointed principal contractor
NG Bailey’s Engineering division is delighted to have been appointed to support the creation of the UK’s new centre of excellence for battery technology, the UK Battery Industrialisation Centre (UKBIC).
The UK’s leading independent engineering and services business has been appointed as Principal Contractor for the prestigious £126 million development which will see the creation of a new facility to develop the latest electric car battery technology near Coventry.
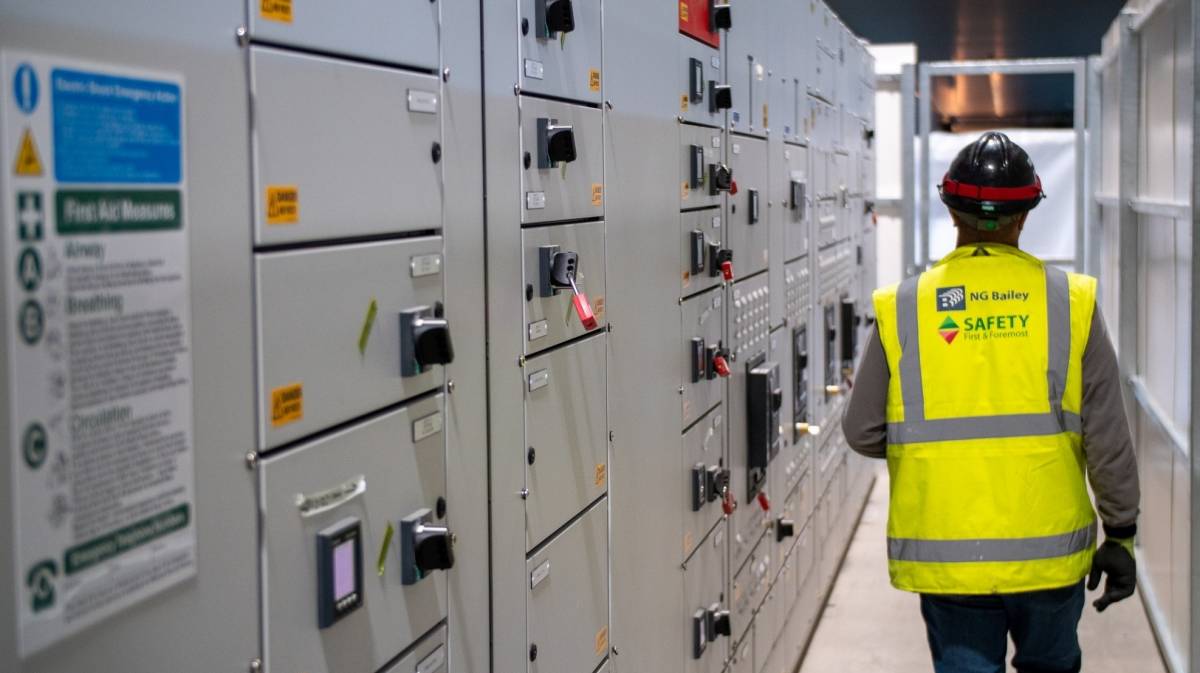
The contract, worth £14.6m to NG Bailey, is being delivered on behalf of a consortium of Coventry City Council, the Coventry and Warwickshire Local Enterprise Partnership and Warwick Manufacturing Group (WMG) at Warwick University.
The facility, which is backed by Government investment, provides a boost to the UK’s ambition to lead the world in the development of zero emission vehicles. When complete in early 2020 it will play a crucial role in enabling the UK to prepare its home-grown battery technologies for global competitiveness and will provide a stepping stone towards the creation of a UK ‘Gigafactory’ – a large scale battery technology factory for electric vehicles.
UKBIC will also provide practical training to upskill people in battery manufacturing and is part of the Government’s Faraday Challenge programme to develop cost-effective, high-performance, safe, low-weight and recyclable batteries.
Duncan Smith, NG Bailey’s Operations Director Midlands, said: “We are delighted to have been selected for this ground-breaking project. As well as showcasing our own design, engineering and offsite manufacture expertise, we are also supporting innovation and industry best practice to deliver a greener future for the UK.”
NG Bailey began work on site in October with the fast-paced project due to be completed in Spring 2020. The company will deliver all mechanical and electrical services for the development the majority of which – including more than 6km of pipework and 100 heavy-duty service modules – will be manufactured offsite at the company’s specialist facility in Bradford.
Offsite solutions include production of horizontal multi-service modules which will enable 56m to be installed every day and an innovative space-saving multi-service bridge structure which will help reduce the amount of space needed to house the building’s essential services and maximise useful production and working.
These techniques will also shift more than 17,500 hours of work away from site helping to create a safer working environment and reduce on-site congestion.
Duncan Smith added: “By being involved in the early stages of the project we have been able to incorporate innovative offsite solutions which will dramatically reduce the amount of time needed on site speeding up the construction and also deliver tangible benefits to the end users.
“We are creating a bespoke 20m long, 5m high ‘bridge’ structure which will house multiple services. The bridge will sit above the facility’s own plant and equipment meaning that useful production and working areas within the facility can be maximised.”
Jeff Pratt, Managing Director of UKBIC, said: “Phase one of the building shell construction has been completed and NG Bailey is due to start work on the second phase, so the build project is really starting to gather momentum.
“UKBIC’s open access process facilities will play a pivotal role in helping the UK to become a world leader in the design, development and manufacture of battery technology for electric vehicles and other applications. We are looking forward to working with NG Bailey on the next phase of creating our exciting new home.”
NG Bailey has sub-contracted Mossvale as their construction partner.
NG Bailey’s Offsite manufacture in numbers:
- 140 fully assembled heavy duty service modules (HDSM)
- 20M long, bespoke multiservice bridge freeing up production space in the facility
- 6 plant skids for both low temperate and chilled water
- 10 (HDSM) trench modules for mechanical and electrical services
- 3 floor standing multi-service heavy duty service modules
- Goal post frames for external compound services
- 10 Air Handling Unit valve assembly modules
- Loose pipe spooling for site installation
- 12 distribution board assemblies